Small- and medium-sized enterprises (SMEs) are turning to collaborative robots to increase flexibility on the plant floor, and companies are looking to improve the technology behind the robots. In a flexible robot cell, the installation and commissioning time is reduced by up to 90%.
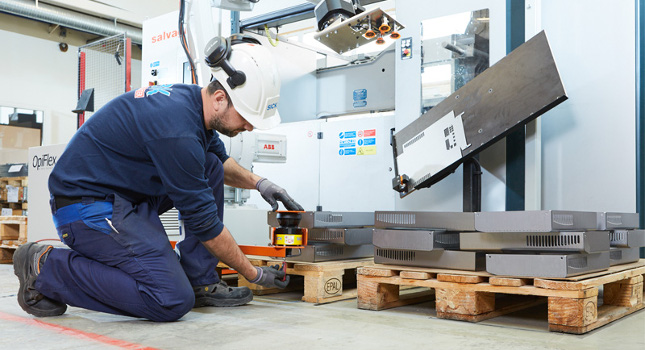
As collaborative robots rise in popularity, humans and robots are being brought into closer proximity. This increased collaboration is leading to a greater need for flexible and mobile automation that doesn’t require the use of safety fences. Small- and medium-sized enterprises (SMEs) are looking to automate small-series manufacturing production, but this has been a challenge using the traditional implementation of fixed and fenced robot cells.
Now, this level of automation is possible using flexible mobile robot cells with fenceless safety and easy robot programming. For example, Swedish robotics company, OpiFlex, developed a way to make large industrial robots more mobile.
With the help of a manual pallet forklift truck, lifting truck, or automated guided vehicle (AGV), the mobile robot can be moved to any relevant workstation in a production facility. It is docked and plugged into a previously installed platform and is ready for immediate use. This allows large robots to move and run at full speed.
Safe robotic options for easy collaboration
Safety laser scanners are permanently mounted on the mobile robot cell to detect people near the station, regardless of where it’s moved in the facility. If a person approaches the robot, the safety laser scanner sends a signal to the safety controller and the robot reduces its speed.
The robot only stops operating completely if the person enters the safety zone and will resume moving once the person leaves the zone. This increases productivity as the robot does not always have to be stopped completely for safety alerts. The safety controller also monitors the robot gripper and stops it as soon as a situation occurs in which the robot could lose parts and endanger the surroundings.
If the robot is moved to another location, the safety implementation also checks whether the mobile robot cell is anchored in the docking station. Careful system integration and attention to safety regulations were used to lower risk, despite the robot’s large size compared to many robots that work in collaborative industrial applications..
Solving the challenge of high mix and low volume
The growing trend of flexible robots helps to support SMEs, Tier 1 companies, and original equipment manufacturers (OEMs) with increased flexibility and productivity for both small-series manufacturing and high-volume production. These flexible robot cells were initially created for SMEs with small series and low-machine utilization. Now, a high number of large corporations, OEMs, and Tier 1 companies have expressed an increased need for flexibility as they go toward higher mix and lower volumes.
Some of these companies also want to use this option for high-volume manufacturing because it is much faster to integrate and set up at a new machine, and it provides added flexibility for robot cells. Flexibility is key: One application may require five robots and another two.
Furthermore, the robots can be programmed without prior robot knowledge in about 10 minutes. Instead of programming the robot for several hours, the operator only has to answer a few questions and teach the robot a few simple movements, then it will automatically program itself.
When juggling as many as five work shifts, it can be a challenge to plan production stops for equipment adjustments or implementing new automation options. Traditional robot cell implementations often stop the manufacturing process for more than 10 days, which means losing up to 30 to 50 shifts.
With a flexible robot cell, the installation and commissioning time is reduced by up to 90%, taking only about two to three shifts. When working within tight production schedules, it is advantageous to make automated implementation easier to a minimize loss of production.
Cooperation may be the buzzword in the field of robotics, but in the smart factory of tomorrow, genuine collaboration between humans and machines really is what counts. Humans and machines that work hand-in-hand as equals is the future, which many manufacturers are trying to make a reality.
Bryan Sellars, segment marketing manager, Sick Inc. Edited by Chris Vavra, production editor, Control Engineering, CFE Media, [email protected].
MORE ANSWERS
Keywords: collaborative robots, machine safety
A kit can help industrial robots work collaboratively.
Flexible robot cells cut installation and commissioning time.
Consider this
What is the biggest obstacle your company faces in implementing collaborative robots on the plant floor?