Robotics technology eliminates repetition, lifts all productivity boats by helping workers on value-added tasks and enhancing productivity.
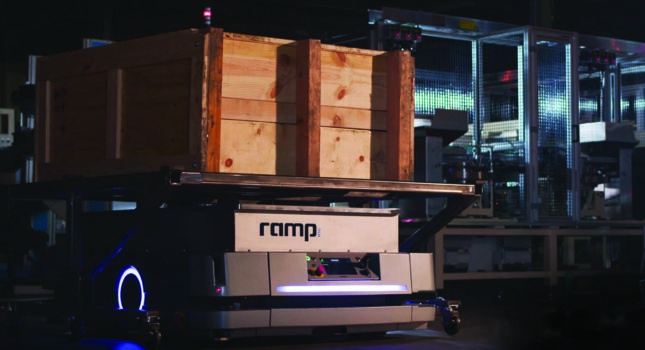
As labor shortages persist and supply chain complexities increase, system integrators can play a crucial role in the industrial value chain, addressing challenges that would otherwise negatively impact manufacturing productivity and growth.
Waterloo, Ontario-based RAMP, bills itself as a “technology development” company that designs and builds custom automation systems. It is part of the Samuel Automations Solution Group. The company provides autonomous handling solutions to its customers, including use of Omron’s autonomous mobile robot (AMR) technology.
RAMP has seen autonomous mobile robot technology alleviate labor and material handling challenges. Automation solutions often focus on non-value-added operations; repetitive and non-value-added tasks diminish productivity. Automating these tasks eliminates the need for manual material handling, sequencing or other mundane processes. RAMP develops automation solutions that enable skilled workers to focus on value-added tasks, thereby enhancing productivity. Successful integration of a robotic solution involves a design process that addresses a range of impacting factors.
In one recent example, RAMP compared its client’s current state of operations — before automation — to its desired state. Regardless of whether the goal is to boost production or to identify new business, factors like layout challenges, interfacing, payload, and cycle times must be carefully examined.
Specifics such as travel distances and demand for specific appliances — such as a robotic arm or control system — were addressed, along with the need for a robust communication infrastructure. Addressing these crucial steps in the initial stages ensured a solid foundation before proceeding to implementation.
Robotics partner
Partnering with automation solution provider, Omron Automation Americas, RAMP successfully integrated Omron’s range of mobile robots across multiple customers and industries including, at the smaller end of the spectrum, Omron LD-90 based autonomous mobile robot (AMR) solutions for use in injection molding applications. Here robots can play a vital role in feeding material from an injection molding operator into a stalker system.
The process begins with the operator unloading a plastic injection molded part, conducting a visual inspection, and then delegating the task to the mobile robot. The mobile robot beside the workstation loads the parts into a fixture upon a conveyance system equipped with multiple lanes.
The small form factor of the LD-90 based mobile solution allows access to tight areas not normally accessible with larger AMRs. Control of robot motions and goals allowed RAMP engineers to fine-tune operations in challenging areas to maximize efficiency.
For larger applications, RAMP leverages the increased payload and larger form factor of Omron’s LD-250, especially in applications where a system is tasked with moving carts around a facility.
For example, RAMP designed and built a cart-top unit that can dock to carts around a facility and move them to other locations as needed. Once delivered, the robot disengages from the cart and is ready to find another cart to move.
The cart-top module enables engaging and disengaging from carts quickly and reliably, but also increases the LD-250’s maximum payload from 250 to 500kg, providing users with the versatility needed to address heavier loads.
RAMP also implements flow racks as an autonomous solution, delivering plastic totes to the line side using conveyor top modules to move totes from one conveyor system to another or to fixed locations for consumption. This automated process ensures a seamless operation where empty totes are picked up and replaced with full ones in a single delivery.
Mobile robots with flow racks also perform tasks such as picking up, delivery or relocating of stationary stands. Robots lift pallets or heavy loads, accommodating a wide range of products for transport. Whether it’s moving a rack or something else, AMRs pick-up and deliver with ease.
Recently, RAMP undertook several very large projects involving robot fleets including Omron’s largest AMR for applications moving large and heavy racks of parts throughout a facility.
Deploying a fleet of robots in a at the same time in a given facility can be challenging. The trick is to set up the application to function efficiently while also being flexible enough to adapt to process changes. RAMP understands how modern manufacturing facilities function and identified user needs and pain points to deliver the best possible robotic solution.
Simulate to analyze
Using mobile planner software and simulation capabilities, RAMP customizes robotics solutions to best fit requirements, including for information and materials management systems. The integrator has the ability to simulate proposed process changes and adjust without negatively impacting real-world work. Multiple simulations of varying conditions and configurations result in efficient AMR solution deployments and can accelerate return on investment in automation.
The solution included structured query language (SQL) database capability that allows operators optimize the system and make it more efficient by analyze the collected data.
Safety is always a consideration when deploying equipment in a manufacturing environment and AMR solutions are no different. They assess loads being moved and ensure robots safely operate at the highest speed, given the payload size and mass. RAMP can address issues related to robot pick-up and drop-off stands. It also can install additional facility side safety hardware in areas needing such.
The RAMP team gained invaluable knowledge and expertise through former training and technical sites. Omron’s proof of concept centers, training facilities, and online training tools are instrumental in keeping RAMP team members up to date. Omron also provides on-site support for customers.
Final words
RAMP implemented the autonomous handing solution in question at a customer site more than three years ago. RAMP and its client continue to evaluate prospects for further investment on a regular basis.
This allows for advances, changes and expansions to be considered, resulting in a safer, quieter and efficient process by reducing fork-truck travel. Besides labor reduction benefits, implementation enhanced safety.
The client achieved its labor-saving targets. By eliminating manual delivery methods, the implementation opened up floor space. Past delivery methods were often inefficient, leading operators to anticipate delays in deliveries and to drop off extra material to prevent production line shutdowns. This causes housekeeping and space crowding problems. However, with the autonomous handling system, these challenges are overcome and provides a streamlined and clutter-free production floor.