Open robotic control: As robotic controls advance in capabilities, other options have been emerging for control, including open control software that can be used with multiple vendors’ robots, programmable logic controllers (PLCs), and other non-robotic controllers.
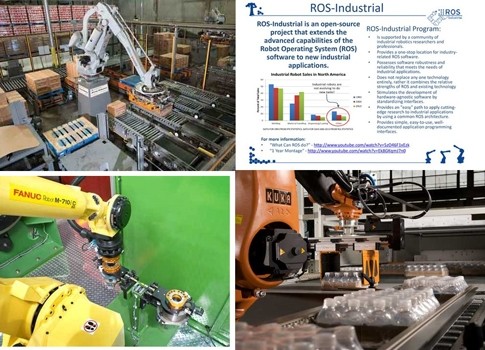
Robotic controls are advancing in capabilities even as other options have been emerging for control. These include open control software that can be used with multiple vendors’ robots, programmable logic controllers (PLCs), and other non-robotic controllers. Link to each of the three articles at the bottom for more information, additional links and images.
Robots should be doing more than 2 or 3 tasks
If tools aren’t enabling more flexibility in use and expansion of robotics, then we need better tools. That’s what’s behind the ROS-Industrial effort from Southwest Research Institute (SwRI). How does setting up a factory in a day sound?
Robots should be easier to use for more applications, and SwRI established ROS-Industrial, an open source industrial robotic software and working group, to broaden the application of robotics and increase robotic interoperability. ROS stands for robotic operating system. A Dec. 5 quarterly community meeting discussed the general direction of the ROS-Industrial program, reviewed new robotic technologies, and publicized the work and the needs of the community.
PLC-based vs. proprietary robotic controls
For facilities that already use programmable logic controllers (PLCs) for other machine control functions, integrating robotic control into a PLC may be a wiser choice than relying on the controller provided by the robot manufacturer.
As more manufacturing facilities and distribution centers discover the benefits of robotic material handling solutions, they must decide how best to control the robot. While robot original equipment manufacturers (OEMs) offer their own tightly integrated controller, recent developments have enabled control by a programmable logic controller, or PLC.
For facilities that already use PLC-based controls for other machine control functions, integrating robotic control into a PLC may be a wiser choice than relying on an OEM proprietary controller. Speaking robot just got easier.
Industrial PCs ease robotics integration
Hardware and software advancements, such as multi-core processors and industrial Ethernet fieldbus technology, are enabling engineers to integrate cost-effective robotic solutions with motion control, communications, and human-machine interfaces.
Adding open-control hardware and software to the convergence of well-known controls principles makes it possible to create machine designs that feature seamlessly integrated robots. This results in game-changing advantages for machine builders and manufacturers and the ability to integrate robot technology into more applications, including those that are traditionally among the most cost-sensitive.
The cost-saving benefits that make this possible include: reduced wiring, network and software platforms that are shared with the overall machine automation system, and a significantly reduced machine footprint. This has led to higher performance mechatronic and robotic solutions, including product packaging with variable product flow and complex material handling lines.
– Control Engineering, January 2014 North American print and digital edition