Overlooked areas when considering if goods should be manufactured in the U.S. or abroad are the total cost of ownership and how automation enhances productivity when applied to new or expanded, “reshored” U.S. manufacturing facilities. See the Reshoring Initiative “Total Cost of Ownership” tool.
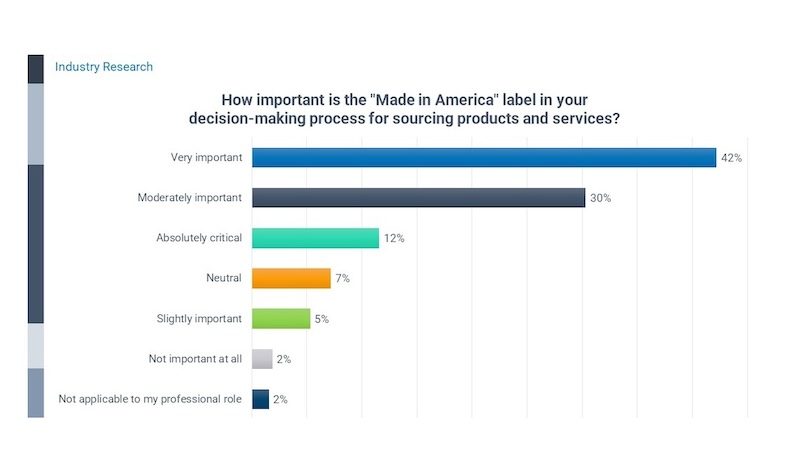
Learning Objectives
- Explore Reshoring Initiative’s Harry Moser updates about significant progress in reshoring and foreign direct investments to increase high-paying manufacturing jobs in the U.S.
- Understand Moser comments on Control Engineering and Plant Engineering research about Made in America and reshoring initiatives.
- Learn career advice related to automation, reshoring and manufacturing jobs, and that metrics need to consider total cost of ownership, not just price; automation can help.
Reshoring Initiative progress, video, insights
- Reshoring Initiative’s Harry Moser updates Control Engineering subscribers about significant progress in reshoring and foreign direct investments to increase high-paying manufacturing jobs in the U.S.
- Moser commented on Control Engineering and Plant Engineering research about Made in America and reshoring initiatives.
- Career advice related to automation, reshoring and manufacturing jobs show that metrics should include total cost of ownership, not just price; automation can help.
After supply chain issues during COVID-19, many manufacturers, beyond the semiconductor industry incentives, are reshoring manufacturing U.S. jobs that previously had been moved elsewhere for lower-priced labor. Control Engineering recently talked to Harry Moser, founder and president of the Reshoring Initiative and former president of machine tool maker GF Machining Solutions. Moser revisited and updated the reshoring topic with Control Engineering; see related video interview. Moser, with degrees from MIT and University of Chicago, has been applying a career full of manufacturing experience to helping others be more profitable in manufacturing.
Moser also discussed the Reshoring Initiative Total Cost of Ownership software, which he said helps correct the 20% to 30% miscalculation when manufacturer reshoring decisions are based only on price.
What’s the most important thing Control Engineering subscribers should know about reshoring?
Moser: About 20% or 30% of what they or their customers are offshoring or importing could be made here or sourced here with equal or greater profitability without having to raise the price to the customer. There’s a huge opportunity for hundreds of billions of dollars of work that could come back and millions of jobs to be created. Even greater percentages and opportunities are available with processes that can be automated.
Please tell us about you, the Reshoring Initiative and recent progress.
Moser: I was brought up in Elizabeth, NJ, right across the river from New York City. At that time the biggest thing in town was Singer Sewing Machine, with a 3 million square feet plant and 5,000 workers. Back in 1900, it was the biggest factory of any kind in the world. My dad ran a third of it, my grandpa was a foreman, and I worked there summers. I drove past 10 years ago, and Singer was gone. As far as I can tell, Singer doesn’t make anything in the U.S. anymore. It’s been replaced with imports from other countries.
During my career, I sold CNC machine tools and foundry equipment, and, industry after industry, company after company I was trying to sell to were wiped out by imports. I started to work in 1967 and felt the decline of U.S. manufacturing. There’s a need for more high-paying, fulfilling manufacturing jobs to enrich the U.S., giving people ways to make a good living, raise families and purchase homes and cars.
And that’s why I founded the Reshoring Initiative in 2010 to help turn that around. There’s been very great progress.
Surge cited in reshoring manufacturing jobs to the U.S.
Figure 1 shows reshoring brought back by U.S.-based companies, and the orange line shows jobs brought here by companies based outside the U.S. (foreign direct investment or FDI). It’s gone from about 11,000 a year in 2010 to about 287,000 last year between the two of them (Figure 2), the second highest year on record, according to a July Reshoring Initiative press release. The press release said: “Reshoring Initiative Annual Report details the remarkable surge in reshoring and foreign direct investment (FDI).” Growth trends continue “driven by increasing global risks. Supply chains today face numerous disruptions, from political tensions and regional conflicts to climate change and extreme weather events. These factors, combined with economic uncertainties, underscore the need for resilient and adaptable supply chain strategies to navigate an increasingly unpredictable global landscape. Reshoring is a major key to reducing these risks.”
Annual report highlights summarized by Reshoring Initiative are:
-
Significant growth has been noted in “essential” industries supported by the Inflation Reduction Act (IRA) and other government subsidies, particularly in EV batteries, semiconductor chips and solar energy (Figure 3). These products drove about 39% of the announced jobs in 2023.
-
Skilled workforce is a top factor. The success or failure of training millions of workers could skew the outcome of the current reindustrialization momentum, in either direction. Trends are moderately positive; for example, manufacturing apprenticeships up 83% in the last 10 years.
-
China remains a large threat, with the highest combination of huge trade dependency, single sourcing and geopolitical risk associated with tension over Taiwan and the possibility of decoupling. Reshoring and FDI from China are near historical highs, with reshoring at an all-time high of 87%.
Reshoring Initiative offers the full report with more analysis of trends, the underlying factors, and the projected impact on the U.S. manufacturing landscape.
Near-shoring, a related trend, also continues to expand. Related recent news reported by Reshoring Initiative is that for the first time in two decades, the U.S. purchased more from Mexico than from China.
We recently asked Control Engineering and Plant Engineering subscribers questions related to reshoring, covered in two survey articles: 30% said made in America it’s moderately important; 42% said it is very important and 12% said it was absolutely critical. Do you have anything about industrial automation and reshoring to add?
-
In that article, Figure 1 (Figure 4 here) noted that “More than 70% of respondents said the Made in America label is important in decision-making processes for sourcing products and services, in the spring 2024 ‘Made in America and Reshoring Report,’ from Control Engineering and Plant Engineering.” Moser said: Consumers say they prefer Made in USA, but do not often purchase that way. I think part of the reason is because U.S. products are hard to find. Import volume approximately equals U.S. production, so companies are not committed yet either. If products were easier to identify or find as made in the U.S., I think people would buy more, like these responses suggest, creating a virtuous spiral of increased spending for U.S-made products. Availability is key.
-
Figure 2 in that article said, “Some sectors are perceived as having greater growth opportunities from Made in America initiatives, including computer and communications, aerospace, machinery, electrical equipment and automotive.” Moser said: This matches very well with Reshoring Initiative data on the actual reshoring and FDI slide. The vast majority of government and military sectors were never offshored to start with, so there is not much to gain there.
-
Figure 5 in that article said, “More than half of respondents said Made in America enhanced production efficiency in their facilities.” Moser said: The biggest impacts should be on inventory levels and availability and communications of successes.
Regarding the second part of the “Made in America” research:
-
Figure 1, part 2 of the Control Engineering and Plant Engineering research said 72% of respondents say “Made in America” enhances facility supply-chain resilience. Moser said: All made in America products enhance supply-chain resilience, except in cases of supply chain gaps.
-
Figure 2, part 2, said, “A made in America strategy reduces lead times for production, according to 62% of respondents.” Moser said: For the 12% that said it results in longer lead times, they need more automation and workforce and quick response manufacturing (QRM).
-
Figure 4, part 2, asked, “What do you consider to be the primary strengths of U.S. manufacturing today?” Moser said: Avoiding geopolitical risk should have been among the choices respondents could select, along with proximity to market (see also, Figure 7, below).
-
Figure 5, part 2, said, “U.S. manufacturing weaknesses or areas for improvement are dependence on foreign raw materials and high labor costs, statistically tied at 68% and 66%, respectively. Lack of skilled labor was next at 45% followed by regulatory burdens at 39%.” Moser said: Dependence on foreign materials seems high but is fixable.
-
Figure 6, part 2, said, “Increased investments in technology and automation (26%), enhanced workforce training (22%) and reduction of regulatory barriers (19%) are the leading ways to enhance U.S. manufacturing globally, according to survey respondents.” Moser said: Automation helps but is not sufficient; currency value needs adjusting, too [though that was not among the choices].
-
Figure 7, part 2, said, “Sourcing American-made products greatly enhances quality for 31% of respondents and somewhat enhances quality for 48% of respondents.” Moser said: This is good news. I will quote it.
-
Figure 8, part 2, said, “Costs influence selection of American-made products. Perhaps not surprisingly, 93% of respondents said they definitely or probably would switch if products were less expensive; 61% said they definitely or probably would switch if American-made products were 10% more expensive; 31% said they definitely or probably would switch if American-made products were 20% more expensive.” Moser said: In future surveys, this question should be rephrased, speaking in terms of total cost of ownership, not only price. I like these answers and plan to quote them.
Do you have other metrics on manufacturing reshoring topics?
Yes, I want to show the percentage of companies actively reshoring (Figure 5), which has gone from 8% in 2012 to near 90% in 2022. This is a dramatic increase in companies that are or are planning to reshore what they make or source. Some of this represents OEMs choosing to switch components in machines from something like a pump made abroad to one that is made locally. We believe that for every job at an assembly plant, there are two or three jobs at supplier plants. That job multiplier effect is highest in manufacturing.
How can automation help reshoring initiatives to create desirable, high-paying U.S. jobs?
Use of advanced technologies in manufacturing attracts those with skills. Manufacturing today offers a much better factory environment than what our parents and grandparents experienced, both safer and more interesting. Figure 6 shows U.S. reshoring jobs by industry in 2023.
For those deciding between “wealth management” careers and engineering, wealth creation careers, what inspiration can you offer?
There’s a lot of satisfaction in making something tangible, like that car that’s behind me (note the Reshoring Initiative logo) or a pump or a casting or a machine part or something, whether you’re the president of the company or the CNC machine tool operator or the automated equipment operator, you get the feeling that you made a good part to satisfy your customer and keep good jobs here in the United States. I have a BS and MS from MIT and an MBA from University of Chicago, so I could have gone into finance, and maybe I’d be richer, if I had, but I did fine. I know people who started as an apprentice in the machine-tool industry and now have executive positions and have done just as well or better than people that got a bachelor’s degree or MBA because of practical knowledge of the process or product and of customers. It’s not a black-and-white decision of money, perhaps there’s a little less money on balance, but there’s a lot of career satisfaction. I spoke recently at a banking conference full of sharp 30-year-olds with finance degrees. Some said they cannot afford to buy an apartment in New York City. But if you’re highly skilled in manufacturing in Erie or Meadville, Pennsylvania, or in Toledo, Ohio, it’s different. You’re making $60,000, $80,000 and eventually $100,000 a year, and it’s easy to buy a pretty darn nice house and have a pretty good life. In finance, some may be working 80 or 100 hours a week for a few years to earn their spurs, and in manufacturing, maybe people are working 50 or 60 hours a week on the high end, but at least they’re getting paid overtime when they’re doing it.
COVID-19 challenged many supply chains. Are automation and reshoring helping?
At the Association for Manufacturing Excellence (AME) annual conference, just past the peak of COVID, I was on a panel that discussed if companies depended too much on just-in-time methodologies, asking if inventories got so low that companies got burned? Some on the panel admitted to being too lean and said they should have had more inventory to avoid the crisis. I said, no, many companies were not lean enough. If companies had more products sourced locally, for major plants, sometimes in the same neighborhood, then they’d have shorter delivery times of days rather than a month or more if sourced offshore, which creates much more supply chain risk. Sourcing locally helps companies be even more lean. The updated Reshoring Initiative Total Cost of Ownership Estimator considers the price of a product, along with duty, freight, inventory carrying costs and other factors, providing a much closer estimate of how much it costs to source products. There’s more value provided with two days delivery time compared to two months of delivery time. For those with data about what shorter delivery time is worth, I’d love to hear about it.
What else on automation and reshoring would you like to address with end users, OEMs and system integrators?
A recent Reshoring Initiative survey showed that the number-one driver for reshoring is geopolitical risk (Figure 7). Dependencies on products from parts of the world with wars or risks of conflicts can increase supply chain risks. If there’s a war between China and Taiwan, for instance, there wouldn’t be anything available from either of those countries for a long time, and supply chain delays could switch from months to years. The map shows the probability of a supply chain being cut off via geopolitical decoupling, think of six months or a year, if there’s conflict. During a conflict, it’s hard to find a new source because 30,000 other companies would also be trying to find new sources. If there were a conflict involving a source country, how much dollars in sales and margin would I lose, and how much more should I be willing to pay for components sourced domestically, to make my end products and keep my customers? Reshoring is a way to reduce that risk for some companies.
Compare the price of goods from China versus U.S. prices
The next graphic, “China FOB price % of U.S.” (Figure 8), shows 190 cases looking at the China free onboard (FOB with cost of goods, customs, packaging, loading, transportation, insurance, etc.) price percentage of U.S., which shows why U.S. companies import as much as they do. The bottom axis shows the Chinese price as a percentage of U.S. price and the vertical axis shows the percentage of cases among the 190. To the right of where the prices are equal on the horizontal axis, 100%, shows how few cases where products from China are cheaper than products from the U.S. The mode of the graphic, the center of instances on horizontal scale, is around 65%. The price for buying from China is about 35% less than U.S. price. Just looking at price, you can see why companies went heavy on imports.
Total cost of ownership for China-sourced products versus U.S.-sourced products
For a more accurate picture, companies need to look beyond price and consider total cost of ownership (Figure 9, Chinese price and TCO, % of U.S.), as mentioned before. In this graphic, the blue line is that same distribution of price, and the red line, total cost of ownership, is that price plus duty, freight, carrying costs, inventory and other relevant considerations that most people would consider to be real. Adding those factors shifts the curve 10 or 15 points to the right. Then if there’s a Section 301 tariff applied (when another country is found to have violated a U.S. trade agreement or engages in unjustifiable or unreasonable practices that burdens U.S. Commerce, part of Title III of the Trade Act of 1974, “Relief from Unfair Trade Practices”) of 15%, that’s the orange line. Among the 190 instances mentioned, based on price only, 8% of goods from China are more expensive than U.S. sourcing. With total cost of ownership considerations, the percentage goes up to 32%, and with a 15% tariff applied, it increases to 46%. By considering more than price on Figure 9, you go from seldom win (8%), to winning about half the time (46%). Doing that math correctly, even without tariffs, shows that 24% of what companies import now could be profitably sourced from the U.S. (32% minus 8%).
Why automation helps with reshoring
U.S. wages are two to five times as high as where we’re reshoring from, so it helps to update, modernize and automate as we’re bringing jobs back here to be competitive. Some might ask what is gained if we increase automation? We’re not on an island. We’re in a jungle, competing for work. We will lose more jobs to automated factories in China, India, Germany and other countries if we do not automate here, because we’ll lose competitiveness. If you want to compete, if you want to have high-paying jobs and a strong economy, to support the military with materials, to balance the budget, to improve ecological balance and reach other goals, then look at total cost of ownership with reshoring supported by automation.
A modern factory, with more robotics and other automation, is more able to attract talent, such as a young engineer or young toolmaker, and is better equipped to compete globally. A virtuous spiral upward helps attract people to U.S. factories and adds to U.S. competitiveness.
An example of how automation helps reshoring
Another interesting thing to think about is that suppose your manufacturing cost is $10 here and $7 there; that’s 30% lower there. If someone asks you to modernize and integrate automation to get our 10 down to 7, that is, take 30% out of manufacturing costs, not just labor, but also materials and other costs, the answer almost always would be no. But if it’s 9 and 8.5 based on total cost of ownership with a 5% difference instead of a 30% difference, now the feasibility of justifying that automation to make up the difference just went up substantially.
I would appeal to people to do their return on investment (ROI) calculations based on total cost of ownership, rather than price, to justify a lot more automation to attract more skilled workers and add competitiveness.
Anyone who wants help to reshore or to justify automation to help reshore, they can reach me at [email protected].
Mark T. Hoske is editor-in-chief, Control Engineering, WTWH Media, [email protected].
KEYWORDS
Reshoring U.S. manufacturing, made in America with automation
CONSIDER THIS
What metrics can you offer to justify reshoring manufacturing jobs?
ONLINE
Related reading: The 2024 annual Control Engineering salary survey showed the two highest perceived threats to manufacturing as the economy and lack of available skilled workers, two topics that directly feed a another concern on the list, offshoring.
https://www.reshorenow.org/tco-estimator/