Artificial intelligence tools are helping reduce factory planning time up to 80% and making robots 40% faster as described in the Automate 2025 keynote presentation, “Industrial autonomy in the era of physical AI.”

AI and industrial robot insights
- Artificial intelligence (AI) creates significant savings in factory planning and accelerated robot use.
- Labor shortages, reshoring efforts and robotic advantages make this a great time to accelerate those efforts with AI.
- AI helps with robot training and adds to savings said Deepu Talla, vice president of robotics and edge AI, Nvidia, in “Industrial autonomy in the era of physical AI,” a keynote presentation at Automate 2025.
Industrial software and artificial intelligence are helping robotic applications bring significant savings to industrial manufacturing design and operations, such as 80% reduction in factory planning time and 40% improvement in robot cycle times, according to Deepu Talla, vice president of robotics and edge AI, Nvidia.
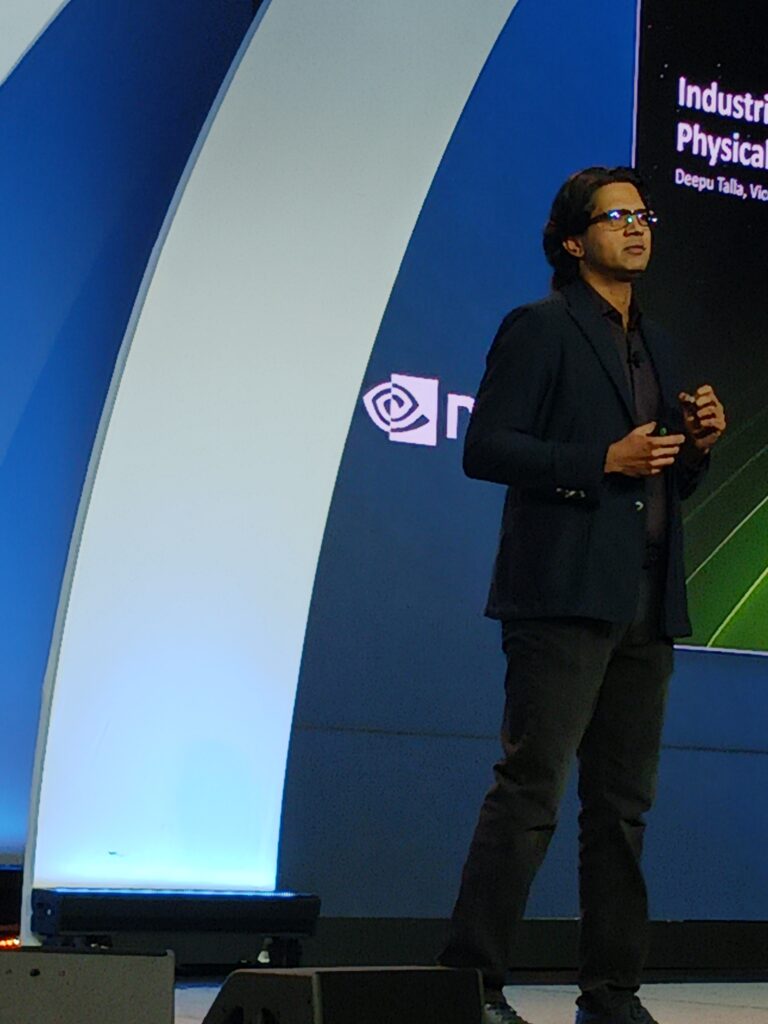
Talla discussed “Industrial autonomy in the era of physical AI” in a May 13 keynote presentation at Automate 2025, by the Association for Advancing Automation (A3). The show and conference are in Detroit, May 12-16, with more than 875 exhibitors, more than 40,000 registrants, and more than 140 conference sessions on robotics, machine vision, artificial intelligence and other industrial automation topics.
Physical artificial intelligence (AI) models that can understand and interact with the physical world will transform today’s rule-based automation, Talla suggested. Nvidia’s ecosystem of industrial software, hardware, AI and robotics partners are helping accelerate AI for industrial transformation. Talla, with a Ph.D. in computer engineering, spent a decade with Texas Instruments before Nvidia.
Robot use will accelerate; AI helps
“For first time I feel like future is coming to the present. Industry has implemented automation for last 30 years. For the last 10 years, deep learning has come about.” Now automation is integrating AI, he said, and bringing greater autonomy. However, Talla said, many traditional installations are brittle, creating tough challenges for AI, robots and humans.
“With AI and robots reaching a reasonable maturity, we’re looking at how ecosystem partners are taking advantage of these technologies.”
Talla said Nvidia’s partner list includes every major robotic company. Robotics is the next $10 trillion industry. Why? 2 billion cameras gather data for potential use in 10 million factories, 200,000 warehouses; 1.5 billion cars and trucks and a future billion humanoid robots. Some of these are now, some in the medium-term of 1 to 3 years and some longer. Sometimes technologies progress with an adoption curve; others, like ChatGPT, progress rapidly in steep steps, reaching 100 million monthly users within two months.
Labor shortages, reshoring and robotics
Everything we do can be automated. More than one humanoid robot per human isn’t inconceivable.
Labor shortages, reshoring manufacturing and changes in robot strategies are shifting industry.
Half a trillion manufacturing resources have been planned to move to the U.S., or nearby, recently, Talla said, creating opportunities for more autonomy and automation.
Why now? The ChatGPT moment for robotics is here as two technologies have reached the tipping point in last 12 months: Physical AI and simulation. Simulation is faster, easier and cheaper. Nvidia chips are tested in simulation first. Robotics, not as much. Over 15 years, our ecosystem of partners is creating a different trajectory.
Data challenge for training robots
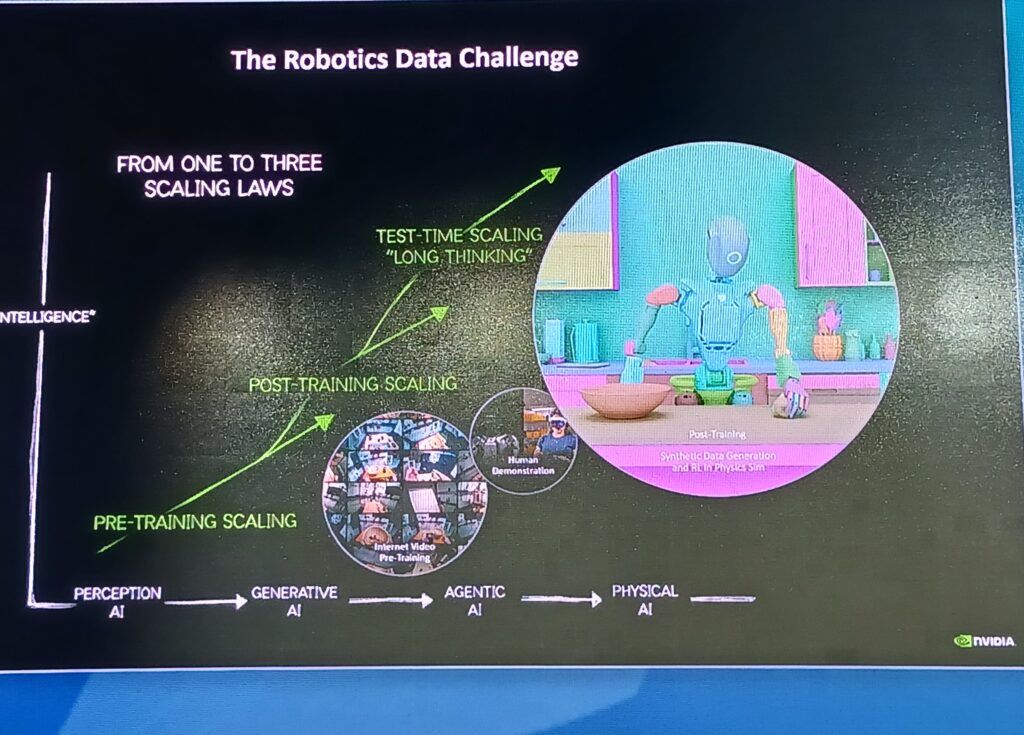
Robotics has a challenge using data for training; Talla described three scaling laws for training (Figure 2):
- Pre-training scaling.
- Post-training scaling.
- Test-time scaling.
It requires progressing in intelligence from perceptive, generative, agentic and physical AI.
Nvidia builds the underlying technology and works with an ecosystem to integrate our technology into robotic companies.
“We think it takes three computers for industrial AI.” Talla explained tools that help.
- Simulate Nvidia Omiverse with Cosmos.
- Train Nvidia DGX.
- Deploy Nvidia Jetson AGX.
Each of the three can provide feedback to others. Video can help provide the huge volumes of data required for robot training.
Practicing in labs differs from the real world.
Foxconn Omniverse is working on robot simulation.
Group N1 provides thinking for robots.
Robotics development platform
Nvidia Isaac is a robotics development platform to simulate, deploy and train robots. It provides robotic foundation models, simulation frameworks and synthetic data generation pipelines.
Robotics built on Nvidia include:
- The Universal Robotis UR15 Cobot AI Accelerator, more than 2 years to integrate
- Vention Machine Motion AI
- Kuka KR C5 Robot Controller, AI capable
- Standard Bots 30 kg Payload Robot.
AI can help robots, inside and out: Examples of savings
Industrial AI needs inside-out treatment (Nvidia Omniverse) and outside-in AI (video analytics AI agent).
Talla said Nvidia is developing for both, then provided examples for savings.
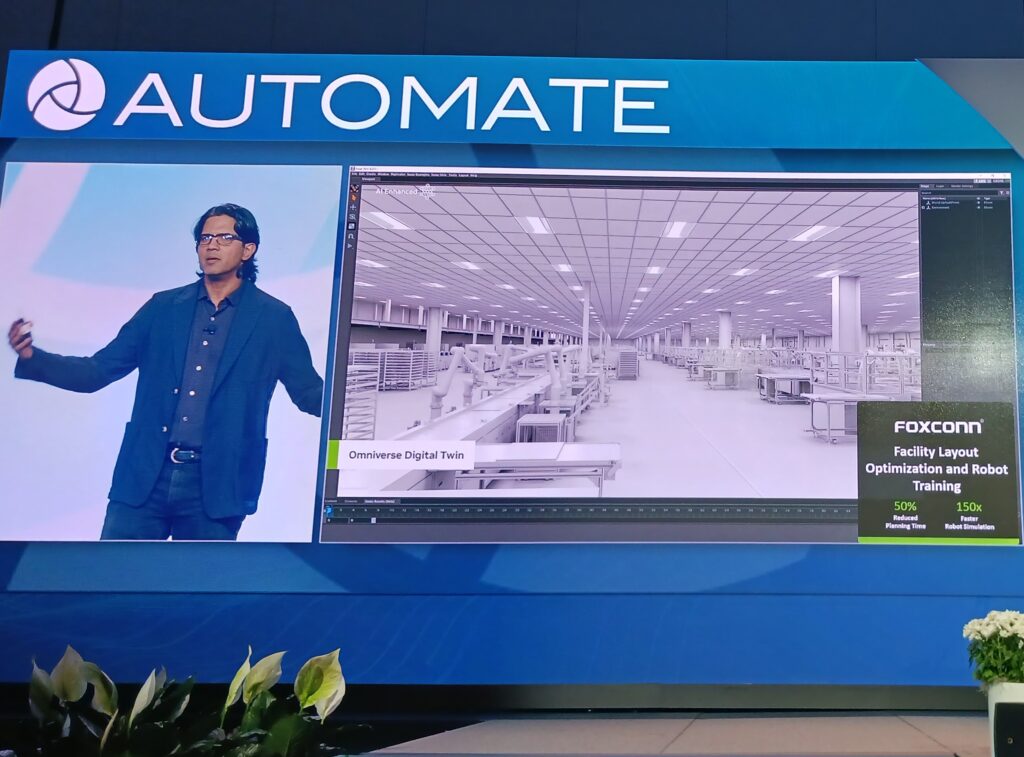
- Foxconn in developing a 450m long plant, optimized the facility layout and use of robots saving 50% in planning time and saw 150x faster robot simulation with the Nvidia Omniverse digital twin. (See Figure 3.)
- Mercedes-Benz reduced factory planning time by 80%
- Schaeffler improved robot cycle times 40% and decreased costs of digital facility planning about 65%.
- Pegatron optimized standard operating procedures on assembly lines to reduce defects 67% and decrease labor costs 7%.
Outside-in visual agents enable automated facilities, visual inspection, operator co-pilots, facility operations agents. Talla suggested using cameras to gather data. Ask your large language model (LLM) what you need to know. Apply video search and summarization (VSS).
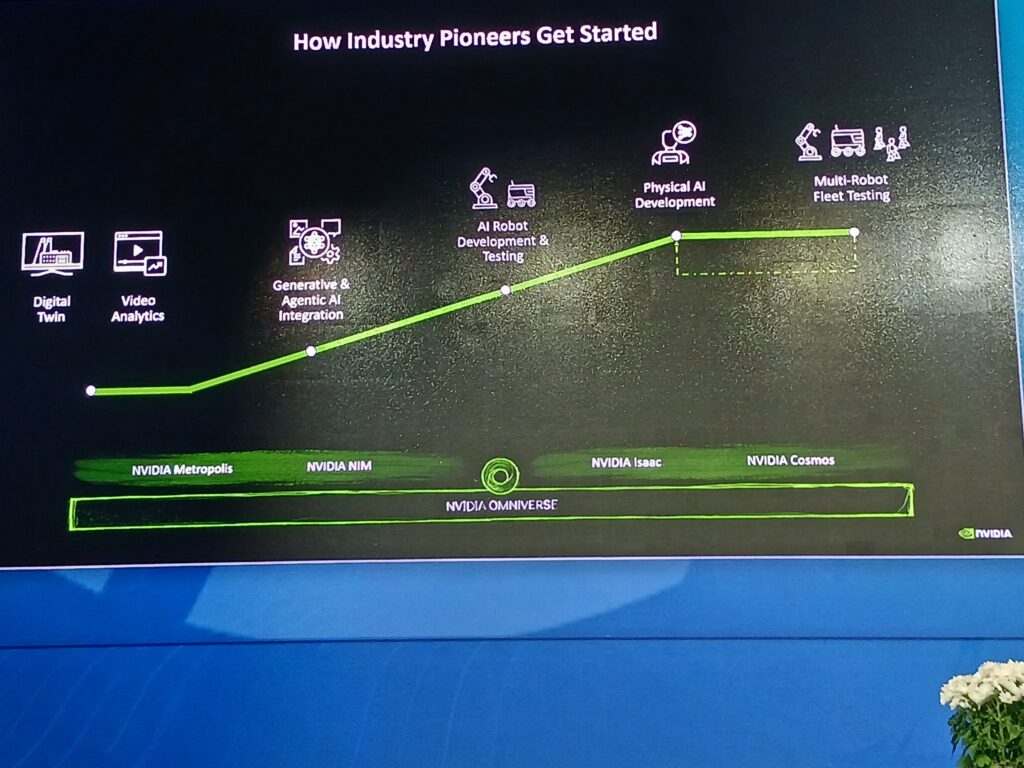
Combine real-time spatial AI, multi camera tracing and question-and-answer report generation, such as: “Show me throughput for the last hour” or “Where’s best place to place carton?”
Developing applications in a digital twin is faster, cheaper and safer (Figure 4). Do video analytics, generative and agentic AI integration, AI robot development and testing, physical AI development and multi-robot testing, Talla said.
Audience questions to Nvidia about AI and robotics
Audience questions to Talla included the following.
Did you mention cybersecurity?
Security and safety are nonnegotiable. Open data sets train a foundation model that becomes specialized. These are based on models trained on data accessible from everyone. Your own data will be added to that.
When will these technologies be integrated?
Some applications are happening now, in the last year or so. Simulating a robotic fleet, for instance, is in research and development, with the tipping point for implementation accelerating.
How can old-fashioned manufacturers evolve?
Technology needs to improve. That’s happening, and integration of new technologies has to be seamless. ChatGPT had record fast application to 100 million users because of ease of use. Increasingly people are using generative AI for programming.
Will humanoid or other robotics expand more quickly?
Humanoid robots are the largest opportunity for the future. Experiments to develop them are faster. The world is now designed around humans so data collection for developing humanoid robots is faster. Humanoid robot development will advance development of AI models. Parts of those models will be applied to other robots, such as paths for automated mobile robots (AMRs) and robot arm paths.
How will digital twins be used?
It’s easiest for brownfield applications to create digital twin because everything exists and can be captured with cameras. It’s easier to build and add new autonomous robots. Greenfield installations will develop a digital twin first.
Mark T. Hoske is editor-in-chief, Control Engineering, WTWH Media, [email protected].
KEYWORDS
Industrial AI, industrial robotics, humanoid robots
CONSIDER THIS
How can AI help your robotic application development and implementation?
ONLINE
Find more coverage by searching “Automate 2025” at www.controleng.com.
Also see: