Case Studies
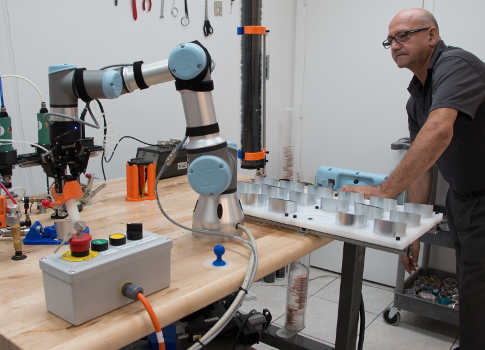
Robots solve assembly line production challenges
Inside Machines: An electronics manufacturer with double-digit product rejection rates used a collaborative robot that was controlled and monitored in a cloud-connected system to handle soldering, drilling, silicone dispensing,… » more
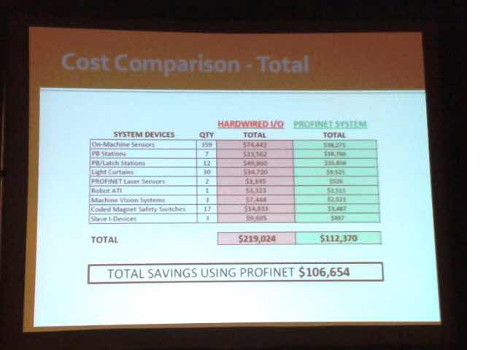
Ethernet cuts automation hardware, labor costs, errors
Think Again about digital networks: A redesigned automated industrial process with the goal of improving safety and efficiency saved $106,654 in hardware, design, and installation costs by using an industrial Ethernet protocol… » more

Robots used in greenhouses to improve productivity
Metrolina Greenhouses used robots from Harvest Automation to help space plants and help improve worker safety and overall efficiency for the company. » more
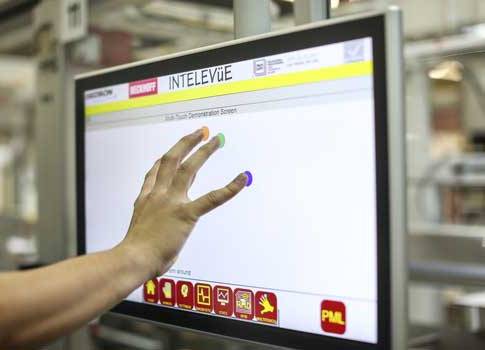
Packaging OEM offers multi-touch enabled machines
Inside Machines: Edson Packaging, a manufacturer of case packing machinery, turns the page to a new era of multi-touch enabled machinery, putting an industrial spin on one of the most popular consumer electronics technologies. » more
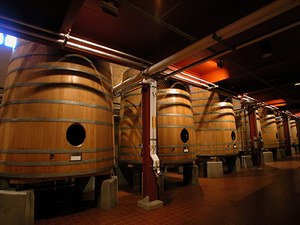
Case study: Pumps provide effective wastewater handling at California winery
Ecolabs designed and now manages the wastewater treatment process for a Northern Californian vineyard producing premium varietal wines for global markets. Learn about the challenges and solutions in developing the system. » more

Automation system retrofit transforms 175-ton hydraulic forming press
Application Update: In less than one month, a rebuild automates press operations to increase production rates and improve quality. » more
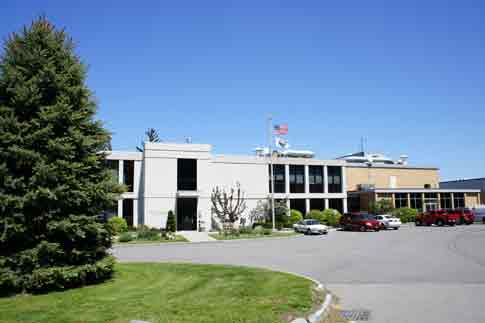
Case study: Evolving SCADA toward energy management
Monroe County Pure Waters, the association responsible for protecting water resources in Monroe County, N.Y., implemented a new SCADA system to protect itself from Y2K threats and continues to reap benefits even 14 years later. » more
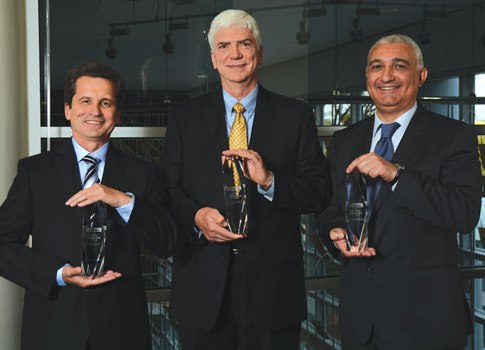
Top Control Engineering articles, January 2014
The most-visited articles at www.controleng.com during January 2013 included: understanding pressure instrumentation, Schneider Electric’s acquisition of Invensys, Control Engineering predictions for 2014, using PID tuning to… » more