Automate 2024: Deciding where and when and how robotics first should be applied in manufacturing was the topic of a Mitsubishi Electric Automation presentation. Should you install a robot?
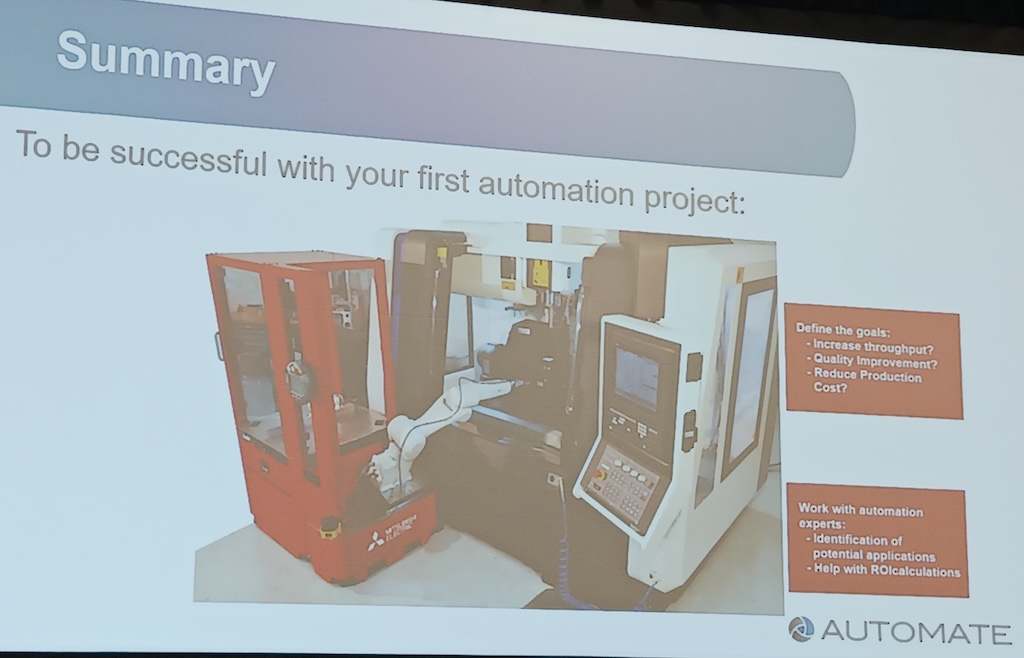
Learning Objectives
- Understand why and how a company’s first robotic automation project succeed.
- Explore how a system integrator helped with the first robotic application.
- Learn of added reasons and more help when considering a first robotic application.
Automate 2024: First robotic installation insights
- Mitsubishi Electric Automation explains why and how a company’s first robotic automation project succeeded.
- A system integrator, SCADAware, helped with Worldwide Fittings’ first robotic application, machine tending a CNC application.
- Additional reasons and more help is available when considering a first, or next, robotic application.
Why and when should the first industrial robot be installed? Too few qualified people are applying for available manufacturing jobs in the U.S., and robots can help in many areas to fill that skills and personnel gap, explained Patrick Varley, product marketing manager (mechatronics), Mitsubishi Electric Automation Inc. Varley spoke at Automate 2024 by A3, the Association for Advancing Automation, in Chicago, during the session, “How their first robot purchase enables a 70-year-old company with 11 facilities on 3 continents to profitably expand their domestic manufacturing.” Varley explained how Worldwide Fittings Inc. increased utilization rate from 70% to 90% or more with a machine tending robot, its first, with an expected return on investment of less than 24 months. In the short video, Varley explained what the robot does in the application.
Why did the company’s first robotic automation project succeed?
The project succeeded, Varley said, because of:
-
A clear need: Find a way to lessen impact of supply chain disruption
-
A defined goal: Identify a part/process that could be cost effectively re-shored to U.S. manufacturing site;
-
Identifying challenges: Similar processes were inefficient, 70% machine utilization rate was too low and labor cost and labor availability issues existed.
Varley, who programmed his first robot in 1987, cited statistics that Illinois has one to two job openings for each job seeker. Nine in 10 manufacturers struggle to close the labor gap, up 38% over the prior year; only 11 days per month are most facilities appropriately staffed. Quality of available labor pool is mostly fair to poor. Resource utilization is the lowest since 2021, just 78.5% in January 2024 Shipping from China averaged 40 days in 2019, and was 73 days in mid-2021. Shipping costs from China has increased 4.7 times compared to 2019.
Worldwide Fittings Inc., founded in 1950, with headquarters near Chicago, found some parts that used to take four or five weeks to receive were taking eight to 10 weeks now. A computer-numerical control (CNC) lathe had a 70% utilization rate, and the company found that retraining decreased productivity because when a machine operation is training, they’re not producing. They wanted a robot to help, but needed to find the right project in the 320,000 square-foot manufacturing and warehousing space.
System integrator helped with first robotic application
SCADAware, a system integrator based in Normal, Ill., helped find a profitable, high-volume part for reshoring in sufficient volume to keep a new automation system in use and integrated the robot to the work cell. A hydraulic fitting was chosen, but the existing work cell was very tight, without much room for automation. A simple robot system was designed using trays for the parts, a sensor system, including flexibility to move it out of the way or work around it if needed.
It’s very easy to overdo automation or make it too complex, Varley warned.
With the robot in place, production doesn’t have to stop; the 95% utilization rate is attributed to a higher pace without breaks. In addition, the robot enables a second shift with less-experience operators.
Making a case for additional robot use, Varley cited post-pandemic research saying:
-
49% won’t consider job that they cannot do remotely.
-
26% never returned to work.
-
66% who lost a pandemic job have been rapidly motivated to rejoin full time.
Added reasons, help for a first robotic application
In addition, supply chain disruptions can be caused by weather, conflicts and overcrowded port facilities. Fuel costs, insurance and higher load/unload rates add reasons for re-shoring.
If in doubt about how automation can help, A3 provides an “ROI Robot System Value Calculator, Varley said.
Mark T. Hoske, content manager, Control Engineering, WTWH Media, [email protected].
KEYWORDS: Automate 2024, industrial robotics, first robotic project
CONSIDER THIS
Have you found the best application to apply your first, or next, robot?