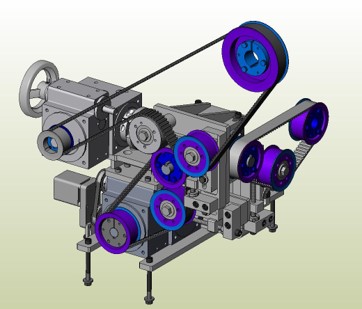
Motors and drives insights
- Motor drives perform a wide range of functions, which means it’s critical to choose the proper one for each individual application.
- It’s critical to size a motor drive to match the motor’s nameplate data.
- Safety is paramount when it comes to motor drives.
Motor drives have become ubiquitous within industrial manufacturing. By regulating motor speed and torque, they increase energy efficiency, reduce equipment mechanical wear and improve process consistency. They integrate better with modern automation systems and enable advanced safety functionality.
However, because motor drives serve a wide range of applications that extend from simple fans or pumps to complex servo systems, it is essential to select, configure and tune them where applicable to ensure the system’s overall safety and performance. It’s critical to know how to correctly size a drive, account for load dynamics, consider the system’s safety requirements, choose an appropriate control mode and tune advanced closed-loop control systems for optimal performance.
Selecting and configuring a drive
Drives are selected and configured to match the electrical and mechanical characteristics of the motor they control, the dynamics of the connected load and the functional and safety requirements of the application. While variable frequency drives (VFDs) are used most of the time to control ac induction motors, servo systems require more specialized motors and advanced servo drives for control. Configuring a drive involves setting up its internal parameters to ensure safe and accurate operation with the connected motor and application.
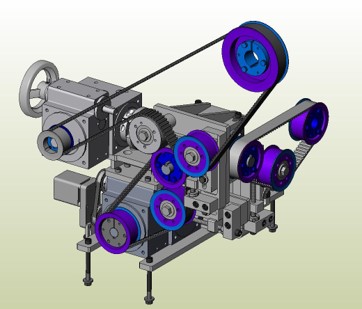
How to properly size a drive
Drives must be sized to at least match the motor’s nameplate data, including voltage, full load current, speed, horsepower and application-specific requirements. These values are entered during configuration so that the drive regulates power correctly to the motor. In some cases, a drive may be selected with a higher power or current rating than the motor requires, either to accommodate intermittent high-demand conditions or in anticipation of future system upgrades. Application-specific requirements will often affect the options such as whether to use encoder, different safety functions, control system communications or drive input/output (I/O) options.
The importance of load dynamics
The physical behavior of the connected load significantly influences drive selection and configuration. Understanding of the system’s load inertia, torque variability, and feedback requirements is critical for choosing the correct drive and configuration to perform safely and reliably. The load inertia is a function of how much mass the motor must turn to get the connected load to the correct speed. A load with a large mass will require significant effort on the drive, whereas a small mass not as much. Another load influence for drive selection is the interaction of the load with other parts of the machine or a drastic change in load. This torque variability could lead to more mechanical stress and higher maintenance requirements.
Acceleration and Deceleration Ramps
These ramps are used for smooth motion control to minimize equipment mechanical stress and sudden motion of the process. Ramp times are selected based on the inertia of the load and the process requirements, including coordination with other equipment in the system and material sensitivity to avoid breakage, wrinkling, or spillage.
Acceleration Ramps: Acceleration ramp times must be set to keep motor current within proper limits. During startup, a motor draws significantly more current than when it’s at regular operating speed. Additionally, the higher the inertia of the load, the more current is drawn to generate the torque required for acceleration. A longer ramp allows the drive to bring the motor and associated load up to speed more gradually, reducing mechanical stress and preventing overcurrent trips.
Deceleration Ramps: During deceleration, a motor acts like a generator, converting the kinetic energy of the rotating load into electrical energy, which flows back into the drive’s dc bus. Higher inertia loads will generate proportionally higher amounts of electrical energy. Deceleration ramps must be tuned to ensure this energy does not raise the dc bus voltage above the drive’s operating limits. In some cases, including high inertia loads or where aggressive stop times must be met, a braking resistor may be added to the drive to dissipate regenerated energy and prevent drive overvoltage faults.
Motor drive safety requirements
The functional safety requirements of the application must be considered when selecting a drive to ensure it supports the required safety features. The safety requirements are typically based on the potential hazards associated with the application. Most modern drives come equipped with safe torque off (STO), which ensures that no torque is delivered to the motor when an emergency stop is triggered without fully cutting power to the drive. Some applications may require additional safety features, including safe speed monitoring (SSM) or safe limited speed (SLS) to ensure the motor remains below defined thresholds during certain operating modes including those where personnel are nearby.
Applications for mechanical and dynamic braking
In some applications, a mechanical brake is required to hold the load stationary when the motor is turned off. This type of brake is used for hoists or other applications to prevent unintended motion due to gravity. The mechanical brake is mounted on the motor and is separate from braking resistors which are connected to the drive. The drive must be configured to correctly control the mechanical brake’s timing. Typically, the brake should be released just after the motor begins being energized and engaged after it stops.
Exploring control mode
The control mode refers to the method a drive uses to regulate the motor’s speed, torque and position. The selected control mode influences drive performance and must be matched to the demands of the application. The primary ac control modes include V/Hz, vector and servo control.
- V/Hz control: V/Hz control is the simplest control method for ac induction motors. It is generally provided by a standard VFD which adjusts motor speed by maintaining a fixed voltage to frequency ratio. The drive regulates motor speed by maintaining a fixed ratio between voltage and frequency. For example, if the motor is rated for 60Hz and 480V at full speed, then to operate at half speed, the drive applies 30Hz and 240V to the motor. This control method is commonly used for variable torque applications such as pumps and fans, as well as some constant torque systems where precise speed regulation is not critical. It does not perform well in applications requiring fast response, precise speed control, or stable low-speed operation.
- Vector control: This type of control is available on higher level VFDs for controlling ac induction motors in applications where torque must change dynamically or precise speed control is required. Vector control works by mathematically breaking the motor’s current into its two orthogonal (vector) components: the one that creates the stator’s magnetic field, and the other that produces the torque in the rotor. By independently controlling each current vector, the drive can be more responsive to variations in load or speed and performs better at low operating speeds.
- Sensorless vector control: Open-loop control relies entirely on the calculated estimates of rotor position, speed, and torque. This method has better dynamic performance than V/Hz control, however its accuracy may degrade at low operating speeds or those involving very dynamic load changes. An example of an application that may be suitable for this type of control is a conveyor system requiring moderate speed changes.
- Closed-loop vector control: Closed-loop control uses an encoder to directly measure the rotor’s position, significantly improving the precision of the model’s calculations of speed and torque. Closed-loop vector control is excellent for applications requiring high inertia handling, precise start and stop, direction reversal or stable low-speed operation. A suitable application may be precision rollers with reverse motion and positioning requirements for material handling.
Additionally, this type of control is well suited for applications that involve a mechanical clutch. Because the drive receives real-time feedback on the motor’s position and speed, it can maintain accurate low speed steady torque during clutch engagement or disengagement. This allows the control system to more precisely coordinate the timing of clutch operation, reducing mechanical shock and wear.
Servo control: Closed-loop control. Used with motors most suited to high performance including dc brushless motors and ac permanent magnet motors. Servo control uses feedback from high-resolution encoders with far more pulses per revolution than their regular counterparts. This high-resolution position allows feedback control loops to operate at much higher frequencies and therefore provide very responsive speed and torque corrections compared to closed-loop vector control. Servo systems are costlier and the most complex of all solutions; however, they provide the accuracy and responsiveness needed for high-demand applications such as robotics, computer numerical control (CNC) machinery and high-speed packaging.
Taking environmental considerations into drive selection
Because drives generate heat during operation, the environment that they’re placed in must be considered. Drives installed in motor control centers (MCCs) typically do not require additional thermal mitigation strategies since these spaces are climate controlled. However, when a drive is operating within a panel enclosure or other warmer environment, additional cooling may be required to keep the drive within its rated operating temperature to prevent thermal faults.
Exploring modular drives and dc bus sharing
In some applications, multiple drives are installed to share a common rectifier stage and direct current (dc) bus. Known as a modular drive system, this setup uses a single power feed to supply the group of drives, reducing wiring complexity and simplifying power distribution and isolation when needed. While the drives share the rectifier stage and dc bus, each one includes its own inverter stage to independently control its respective motor. Drives used in these systems must support dc bus sharing and be configured to meet the shared power and any coordinated braking requirements of the system.
How to tune a closed-loop drive system
When the control mode utilizes real-time encoder feedback (closed-loop vector control and servo control), a drive’s internal control parameters must be tuned to optimize its response time with the mechanical system. Tuning is performed during system commissioning and startup and involves the following steps:
- Motor Characterization: the drive runs the motor while it is disconnected (uncoupled) from the load to measure its internal electrical characteristics. These baseline values are used by the drive to create an internal model of the specific motor it is controlling.
- Load Integration: the motor is reconnected to the mechanical load so the drive’s response times can be tested and tuned for the system’s real operating conditions.
- Gain Settings Optimization: A drive’s gain settings are the control parameters that determine how aggressively the drive responds to differences between the commanded and actual motor behavior based on encoder feedback. Gain settings are adjusted, refining the drive’s response time to ensure the motor changes speed and torque smoothly without instability or oscillation during these dynamic states of operation.
When the gain is set too high, the drive overcorrects for small differences with too frequent motor current adjustments. This results in motor oscillation which vibrates it in the audible range producing a high-pitched hum during corrections. Alternately, like other feedback systems, when the gain is set too low, the drive responds too slowly to changes, leading to sluggish motor performance and noticeable system lag.
How to program drives
Drives are integrated into the controlling programmable logic controller’s (PLC) I/O configuration tree, allowing for direct control and real-time monitoring. Most modern drives also allow the PLC to read and write parameter data, monitor drive faults, connection status and verify firmware versions.
Vendor tools simplify the selection process and debug
Most vendors offer software tools to assist with selecting the appropriate drive model based on motor specifications and application needs. Modern drives connect easily to PC-based vendor configuration software, allowing all parameters to be viewed in a single drive profile interface. These software tools often include built-in diagnostic features and visual logic diagrams that simplify troubleshooting.
While motor drives have become indispensable within modern industrial applications, they are only fully utilized when they are selected to correctly address the demands of the application, configured to meet performance and safety requirements and tuned as appropriate for robust and accurate motor control. Whether the drive is controlling a basic fan or managing motion in a complex production line, its proper setup supports more stable performance, greater energy efficiency and longer-lasting equipment.
Rich Houtz, PE is a controls and automation engineer with Hargrove Controls & Automation.