A system integrator leveraged enterprise resource planning (ERP) products to help a packaging client realize major gains and meet growing demand by giving them access to real-time data.
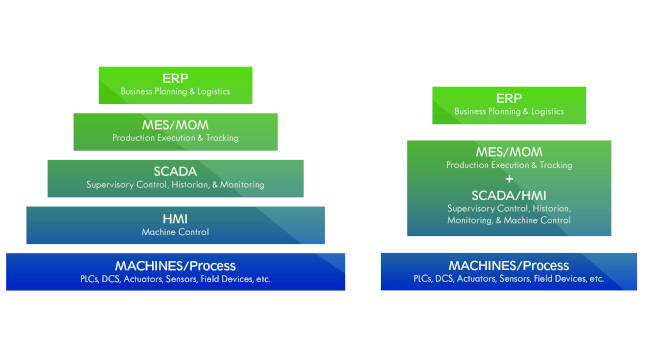
Learning Objectives
- A system integrator performed helped a packaging company develop a plan to improve their operations after getting increased demand due to the COVID-19 pandemic.
- The integrator used a connectivity module to improve their enterprise resource planning (ERP) and other systems to provide better data and information flow throughout the company.
- The project gave senior management better insights for their operations as well as the ability to use the data to improve other aspects of their business.
Asset management insights
- Getting enterprise resource planning (ERP) systems to communicate with other systems prevents data silos, which can prevent companies from seeing a much larger picture about their operations.
- Companies looking to improve asset management should develop a plan that considers all aspects of the operation, which can help improve scalability as well as lessening the burden on the operators by making it a more automated process.
Companies today are looking to bring their systems into the modern age and be able to obtain real-time manufacturing data at the machine level without manual intervention. They also want to bring everyone onto the same system while reducing training and licensing costs. Companies also are looking to achieve better control and efficiency in their day-to-day operations. All the while, they’re looking to accomplish these tasks while scaling the business to meet aggressive expansion goals. Â
It may seem like a tall order, but a system integrator accomplished this by conducting a needs analysis and executing a plan for a packaging company that serves end users in the pharmaceutical industry. The company provides solutions designed to reduce product damage risk, improve dimensional control during shipping and storage and allow for broader temperature stability. Â
When COVID-19 hit, demand for the company’s injection-molded plastic packaging skyrocketed. This proprietary product shares characteristics with glass, but is faster and easier to manufacture, while also enabling downstream manufacturers to package vaccines and pharmaceuticals safely.Â
Introducing ERP connectivity in manufacturing operationsÂ
It helps to look at the role of enterprise resource planning (ERP) connectivity in manufacturing operations to understand what comes next.Â
Manufacturers have many crucial systems that need to talk with one another. The traditional manufacturing stack includes human-machine interfaces (HMIs), supervisory controls and data acquisition (SCADA) systems, manufacturing execution systems (MES) and ERP layers. These systems are most effective when they work together. Â
For example, in an integrated manufacturing stack, an ERP system may confirm inventory exists and release a production order to manufacturing. From there, MES makes it possible to present detailed work instructions to the plant floor operator, schedule production, track real-time work in progress (WIP) inventory, and more. Once the production order is fulfilled, the actual material produced and consumed is reported back to the ERP system. SCADA/HMI provides machine control, communicating with machine controllers, collecting and storing data and monitoring for alarms. This fully integrated process simplifies the operator interface and reduces the complexity of operator tasks by presenting everything in one place. Â
On the other hand, when ERP and other manufacturing systems do not communicate, data silos often arise. As a result, collections of data controlled by one department or business unit remain isolated from the rest of the organizations. When data is siloed, or inaccessible to part of the organization, information may be incomplete or inconsistent between business units, leading to increased risk of redundancy, inefficiency and inaccuracy. If the production staff also use multiple systems with different custom user interfaces, they inevitably require more training while the increased risk of errors, duplication of data, and process management challenges persists. Â
The simplest solution to avoid data silos is implementing manufacturing systems that talk to one another. However, this is easier said than done. Common but less-than-ideal approaches to integrate manufacturing systems include expensive middleware and custom integration. Custom development may seem like a cost-effective solution, but there are significant short and long-term drawbacks.Â
As a rule of thumb, more customization comes with increased risk and complexity. Custom integration of MES and ERP systems often requires the mapping and conversion of data, which means the organization must take on the added burden of maintaining high volumes of script over time. Further, considerable time and resources are needed to manage future modifications and debugging.Â
So what is the ideal solution? The right connectivity solution will:Â Â
- Minimize the number of systems in the manufacturing stack.
- Provide a low-code alternative to custom integration.
- Decrease the chaos with unified interfaces.Â
- Decrease the cost by reducing costly programming maintenance hours.
- Coordinate data more easily for use by multiple systems.
Developing an initial needs analysisÂ
The project started with an initial needs analysis. By leveraging the business connector flowchart, scripting and mapping capabilities, a design and project roadmap was created as well as a process mapping analysis to visually map out workflows and processes.Â
After obtaining customer approval, the project was built in a SCADA software. The templates and allowed for simplified ongoing maintenance by reducing the need for proprietary systems. By planning ahead and utilizing templates early in the project, the integrator would not have to build each component from scratch and would save a significant amount of time on the project.Â
Aligning the project with the strict requirements for highly regulated industries like pharmaceutical manufacturing and food and beverage processing required deep experience and knowledge in this area. The data collection and templating capabilities consider regulatory requirements such as audit trail and data integrity.Â
The solution featured two central steps:Â
- Configure the platform with the MES module for all machines on the client’s lines.
- Design an information template capable of obtaining all data the ERP system needs in addition to the data needed at each machine.Â
Setting up a web services integrationÂ
The integrator worked with machine vendors to ensure the PLCs mapped to the Ignition template as well as the ERP vendor on web services integration. The web services module supported SOAP and RESTful protocols, configures quickly for custom integrations with any ERP API, and can be called from anywhere. It also supports data translation and mapping to ensure any data source and destination receive the right data in the right form.Â
The integrator configured the system to collect information from the machines, add the information to a template, and then present the collected information to various places where it is useful. Â
Leveraging a business connector moduleÂ
An ERP system was set up, which was integrated with a business connector module, allowing the client to manage and gain insights into its manufacturing, reporting, financials, supply chain, and operations.Â
The business connector module is a connectivity tool that gives an intuitive low-code way to enable gateways to retrieve and send data in real time to ERPs and other higher-level business systems. Featuring a highly visual, drag-and-drop user interface (UI) and mapping toolset, it lets you sequence communication, create charts (or use pre-built), and map data between systems without reams of scripting — and coding expertise. The total cost of ownership (TCO) decreases as it requires neither expensive middleware nor extensive integration labor. This application helped the integrator save needed time when delivering this solution.Â
The business connector module pairs well with the ERP module and enables a native connection to on-premise servers, dynamically pulling in objects from the ERP system. The module accurately communicates all essential enterprise data and the module interface also leverages the ERP’s remote function call protocol to provide high-performance connectivity without additional middleware. This gives manufacturers control over synchronous or asynchronous processing, avoids duplicate messages, and ensures messages are processed in the correct order.Â
Combined with web services, the business connector opens not only ERP, but a wide range of systems including advanced planning systems (APS), warehouse management systems (WMS), product lifecycle management (PLM) systems, computerized maintenance management systems (CMMS) and cloud-based analytics and reporting systems (AI/ML/etc.).Â
Five improvements from the project Â
The project brought several benefits to the packaging company including:Â
1. Reduced operator training:
By flattening the integration stack, machine operators need to complete only one workflow instead of two, resulting in less work and lower risk of forgotten data entry. Everything the operator must do is now presented on a unified human-machine interface (HMI), which eliminated the need for a second interface for inventory information entry.
2. Low-code ERP connectivity:
Using the business connector to connect to the ERP software allowed the integrator to utilize the user-friendly visual interface to sequence communication and map data between the two systems. This was a simpler and less time-consuming process than custom developing the ERP integration.  Â
3. Enhanced scalability at a reduced cost:
The number of computers on the plant floor grew to over 100 with no additional licensing costs, allowing the packaging company to grow without being hindered by unexpected hidden fees. Within an site license for the SCADA or MES used, unlimited lines, machines, users, screens, reports, and field device connections are supported at no extra charge.Â
4. Easy-to-use infrastructure:
The packaging company incorporated this SCADA software template into the standards it shares with machine vendors who may be working on the project. As a result, all machines provide the right information to the management systems with minimal effort. Using a template to ensure uniform design patterns across multiple machines allowed the integrator to meet client demand — even as the request for integration rose from the initial 41 machines to at least 100 machines. This also enabled the quick implementation of a statistical process control (SPC) system. Â
5. Real-time automatic data collection:
The connection of the business connector to other MES modules enables consumables to be tracked automatically from inventory to production. Once ERP is connected to MES and SCADA/HMI, the possibilities expand. Real-time automatic data collection with context helps the client in three ways:Â
Prioritize plant floor time and effort: Busy engineering and production staff can access objective data to point them in the right direction when they encounter a problem. This means less guesswork and allows them to better prioritize their time. Â
Continuously improve: With access to real-time data for analysis and reporting, the root cause of downtime, waste, and other production issues becomes more visible, unlocking opportunities for improvement.Â
Comply with legal regulations: In highly regulated industries, meeting compliance challenges are of utmost importance. With complete traceability comes increased accuracy of parts produced and raw materials inventory, as well as the ability to document proof that products were made properly with the correct raw materials and the correct settings. Â
Fulfilling the promise of Industry 4.0Â
The value of real-time manufacturing data goes well beyond the production floor. The worth of this data, and the insight it can provide, became abundantly clear during the execution of this project. Not only did the data help senior management at the packaging company gain better awareness of their operations, but it also presented a future opportunity to use this data in other aspects of the business that went beyond the scope of the project. Â
The potential to use this real-time data for business-wide decisions is now realistic. The promise of Industry 4.0 is often discussed in the manufacturing industry, and this project delivered available data that could help realize that promise. Regulatory compliance and continuous improvement are supported through the move from traditional processes to the world of digital. Real-time data makes future projects focused on vertical integration, horizontal integration, automation, and optimization targets for the next round of possible operational improvement. Â
Â
Rajah James is manager of products at Grantek. Edited by CFE Media and Technology.
Â
Keywords: enterprise resource planning, asset management Â
A system integrator performed helped a packaging company develop a plan to improve their operations after getting increased demand due to the COVID-19 pandemic.Â
The integrator used a connectivity module to improve their enterprise resource planning (ERP) and other systems to provide better data and information flow throughout the company. Â
The project gave senior management better insights for their operations as well as the ability to use the data to improve other aspects of their business.Â
Â
CONSIDER THISÂ
How are you improving information and data flow in your facility?Â