Arizona State University researchers have found that alloys, while strong, can be broken down by stress and corrosion in harsh chemical environments.
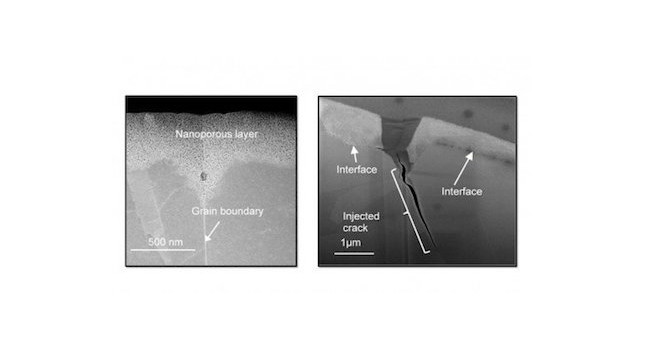
Alloys — metals combining two or more metallic elements — are typically stronger and less susceptible to cracking than pure metals. Yet when alloys are subjected to stress and a harsh chemical environment, the alloy can fail.
The reason? Cracks caused by corrosion. The cracks are generally thought to propagate slowly by the simultaneous, parallel actions of stress and corrosion where the tip of the crack never proceeds beyond the corroded area.
Researchers at Arizona State University (ASU) found cracking proceeds more quickly than they thought. That is, stress can inject a crack far into the un-corroded region. The team studied a form of corrosion called intergranular stress-corrosion cracking (IGSCC). Caused by environmental conditions, this type of corrosion causes cracks to propagate through alloys. It leads to the degradation of materials often used in bridges, airplanes, and power-generating stations. The research shows the structure that forms where tiny grains of two metals meet in an alloy can lead to cracks in an area previously unaffected by corrosion. This insight is critical to designing new alloys that deter stress corrosion-induced failures and to better assess the lifetime of existing alloys in service.
ASU scientists believed IGSCC requires the simultaneous presence of tensile stress and corrosion; however, the exact nature of this synergy has eluded experimental identification.
The team examined the behavior of a laboratory model silver-gold alloy. The alloy mimics the corrosion behavior of important engineering alloys, such as stainless steels and nickel-based alloys used in nuclear power plants.
Corrosion in these engineering alloys, as in the model silver-gold alloy, results in nanometer-sized holes within the corroded layer.
A key parameter determining the occurrence of rapid IGSCC is the adhesion between the corroded layer and the un-corroded alloy. To study the alloy, the team used atomic-scale techniques, together with statistical characterizations. They determined the apparent requirement for the simultaneous presence of stress and corrosion exists because of time-dependent morphology changes that affect adhesion.
As long as adequate adhesion between the layers is maintained, a crack that starts with the corroded layer may penetrate into the un-corroded alloy. If the nanoporous corroded layer breaks away from the un-corroded alloy, the local stress drops and the crack only grows slowly. This means there can be a significant mechanical component to stress-corrosion cracking that cannot be identified by any measurement of corrosion. It also means the crack can progress even if the stress is applied after the corrosion stops.
The result is a corrosion measurement can underestimate the rate of stress-corrosion cracking by multiplicative factors of 10 or more. The research clearly shows the roles of stress and corrosion can be decoupled, but there is synergy in these effects that leads to material failure.
The results provide a path forward for obtaining a more complete understanding of IGSCC of alloys that are currently used. The new understanding also provides a foundation for designing new materials with improved properties for harsh energy and industrial environments.
This content originally appeared on ISSSource.com. ISSSource is a CFE Media content partner. Edited by Chris Vavra, production editor, CFE Media, [email protected].