Faster connectivity, data monitoring, and circuit protection are among advantages of device-level wiring solutions.
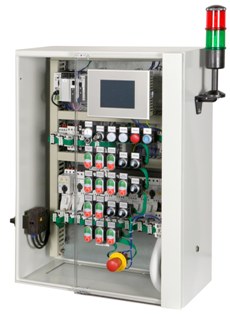
Innovative, user-friendly, device-level networks can provide original equipment manufacturers (OEMs) with an intelligent connecting solution that reduces commissioning time, improves wiring accuracy, and simplifies troubleshooting. Ultimately, they can help to drive increased profitability. That said, not all networking solutions are well suited for use within a control panel. Control panels perform a wide range of applications and have specific connectivity requirements that are not adequately handled by every network. Consider the following criteria:
- Simple connectivity. Is the cable media flexible enough to route to the devices in the panel? Ensure the connectors are easy to locate and connect to the cable. To minimize setup time, the connecting solution can have auto-addressing capabilities as well as accommodate both device control and power needs. Furnishing the panel building process with new solutions can improve throughput and profitability. Lastly, to ensure simple connectivity, the cable media should be able to extend both inside and outside of the control cabinet.
- Composition of I/O connections. The composition of the I/O connections will determine which type of device-level network is best suited for a control panel. Does the control panel I/O consist primarily of motor-control type connections (like motor starters, contactors, relays, and pilot devices)? Or, is more than a third of the I/O connected to position sensors? Networks that are primarily composed of motor starters and pilot devices can use connecting solutions that have a built-in communication system and integral diagnostics, allowing you to easily troubleshoot and improve wiring accuracy. On the other hand, control systems which require numerous sensor inputs may be better served with device-level networks that include quick-connect type cable connections and cord sets.
- Data monitoring. Increasingly, end users want data monitoring on some or all of their motor loads. In traditional PLC-control systems, this data is provided by current transformers (CTs), which are wired back to analog inputs on the PLC. Device-level networks can connect to electronic manual motor protectors (MMPs) or overload relays—the information can be monitored over the network, without using CTs or analog inputs to the PLC. Furthermore, the space requirements for electronic versus electromechanical MMPs or overload relays is about the same, so it is feasible to upgrade or retrofit control panels and/or to have this option on a larger number of motor loads.
- Design flexibility. Does the end user specify the preferred brand of programmable logic controller (PLC)? How does this impact engineering, documentation, and panel layout? Smart, device-level networks can help to standardize the control panel by eliminating the need for traditional PLC input/output (I/O) modules and use motor control components that can connect directly to the network. There’s no need to reconfigure the control panel layout and wiring for different PLCs.
- Control circuit protection. Is it difficult to troubleshoot after someone changes the panel wiring after installation? How do you prevent someone from bypassing or removing the safety interlocks that are part of the control design? Today’s device-level networks can deter unauthorized wiring changes and help prevent control wiring interlocking from being bypassed or jumpered. Additionally, device-level networks employed today can continuously monitor all devices on the network and detect changes in status or configuration.
- Standardization. Do you build multiple control panels that have the same or similar configurations? Do you offer optional devices for the control panels? Do you have to reengineer to change the panel wiring to accommodate these options? Intelligent, device-level networks speed design, assembly, test, and commissioning by eliminating or reducing point-to-point wiring and use quick connectors to connect control devices. They can significantly reduce the wiring effort required to build panels; some allow you to replicate the connection wiring harness—saving costs and time. They allow programming of the optional features in advance, automatically detecting when optional devices are present. This allows you to have one PLC control program, one wiring layout or connection harness, and control panels that can be easily be field upgraded.
– Richard Chung is product manager at Eaton.
DID YOU APPLY FOR, TURN IN A CONTROL PANEL DESIGN TUTORIAL VIDEO? www.controleng.com/controlpanelcontest