Testing drive-and-motor systems is a three-step process.
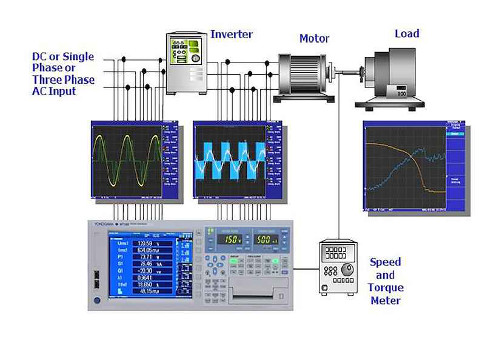
Complete testing of a pulse width modulation (PWM)-based drive and motor system is a three-step process. Step 1 is accurate measurement of PWM VFD input and output power to identify drive efficiency and power losses. Step 2 is accurate measurement of motor input power. Step 3 is accurate measurement of motor mechanical power. The optimum method is to integrate all three steps using a single power analyzer to eliminate time skew. This provides excellent efficiency calculations as well, in one software and hardware solution.
Some power analyzers have a motor option in which the speed and torque signals can be integrated in this manner. These power analyzers can measure electrical power and mechanical power, and send the data to a PC running software from the original analyzer manufacturer, or custom software from a system integrator (see Lead Photo).
PWM drive measurements for ac motors
When using a PWM VFD to operate a motor, it is often necessary to measure both the input and output of the VFD using a 6-phase power analyzer. Not only can this setup measure the 3-phase power, it can also measure dc or single-phase power (see Figure 1).
Depending on the analyzer, the setup mode will be performed in the normal or RMS mode. The wiring configuration should be set to match the application, such as 3-phase input and 3-phase output.
Any line filter or low-pass filter should be off because the filtering will obscure the measurements. However, the zero-cross filter or frequency filter should be on because it will filter the high-frequency noise so the fundamental frequency can be measured. This measurement is necessary when tracking the frequency of a drive.
Figure 2 shows a PWM output voltage waveform with a highly distorted voltage, chopped high frequencies, and a lot of noise on the current side, making for a difficult measurement. High-frequency switching on the voltage signal creates a much distorted waveform and with high harmonic content. The frequency varies from 0 Hz up to the operating speed.
For such a noisy signal, special current sensors are needed for measurement. Accurate PWM power measurements also require wide bandwidth power analyzers capable of measuring these complex signals.
Figure 3 is an example of the voltage harmonic content from a PWM output. Beat frequencies are present, and voltage harmonic content exceeds 500 orders (approximately 30 kHz). Most of the harmonic content is in the lower frequencies on the current side.
PWM motor, drive measurement issues
Inverter voltage is typically measured in one of two ways. A true RMS measurement that includes total harmonic content can be used. However, because the fundamental waveform is primarily what contributes to the torque of the motor, a simpler measurement can be made and used. Most applications only require measurement of the fundamental waveform.
There are two main methods for measuring the fundamental amplitude of the voltage wave. The first and simplest is to use a low-pass filter to remove high frequencies. If the power analyzer has this filter, simply turn it on. Proper filtering will give an RMS voltage of the inverter fundamental frequency. However, this type of filtering does not offer a true total power measurement, so filtering isn’t the most exacting method.
The second method is the rectified mean measurement method, which delivers an RMS voltage of the fundamental wave without filtering by using mean-value voltage detection scaled to the RMS voltage. The algorithm of the rectified mean of a cycle average will provide the equivalent of the fundamental voltage that will be very close to the RMS value of the fundamental wave.
Using this method, the total power, total current, and fundamental voltage can be measured.
Measuring fundamental wave amplitude using harmonic analysis
The harmonic analysis function can be used to find the true fundamental voltage by using a Fast Fourier Transform (FFT) to determine the amplitude of each harmonic component including the fundamental wave. This gives an accurate RMS voltage measurement of the fundamental wave. The latest power analyzers can make simultaneous true RMS measurements along with harmonic measurements.
In Figure 4, the "Urms2" (the RMS value on the PWM output) is a very high number, and F2 (the mean value of the fundamental) is somewhat lower. The value "Urms3" (filtering the fundamental) provides a similar result. Finally, U2 (1) is obtained from harmonics analysis or FFT calculations of the fundamental. F2, Urms3, and U2 (1) provide results that are very close, but the U2 (1) FFT calculation is considered the most accurate.
Inverter current is usually measured only one way, and that is as a true RMS signal, because all harmonic currents contribute to and are responsible for temperature rise in the motor, so all must be measured.
Another important measurement involves drive Volts-per-Hertz (V/Hz). A PWM drive should maintain a constant V/Hz ratio over the operating speed of the motor. The power analyzer can calculate V/Hz using the RMS or the fundamental voltage value. The analyzer’s user-defined math function is used to develop an equation for this measurement.
Measuring dc bus voltage
The dc bus voltage in the PWM can be measured to check for over- and under-voltage conditions. This measurement can be performed inside the drive on the terminals of the capacitor bank. However, an easier method is to use a power analyzer waveform display with the cursor measurement.
When performing the waveform display with the cursor measurement, one must make sure the cursor isn’t directly on top of the small spikes in the display. Instead, the cursor must lie across the waveform to make an accurate measurement. Figure 5 shows a PWM voltage measurement with high-speed switching. The cursor is placed to read a value, such as 302.81 V in this measurement.
Mechanical power measurements
Mechanical power is measured as the motor speed times the motor torque. There are many different types of speed and torque sensors on the market that work with a variety of motors. It is wise to confirm compatibility in each case. These sensors can be used to provide the mechanical measurement information to calculate the mechanical power measurements in the power analyzer.
Many sensors come with interface electronics to condition the signal properly to work with power analyzers or other equipment. The conditioned signal can be an analog output, or a serial communication output that goes to a PC and its application system software.
One option to implement mechanical power measurements is to use both a sensor and a corresponding measurement instrument from a given manufacturer. This approach has advantages because the sensors will be exactly matched to the instrument. Readouts for torque, speed, and power will be available, and there will likely be options for PC connectivity along with associated application software.
A more integrated approach is shown in Figure 6. With this configuration, the speed and torque signal outputs from the sensor instrumentation are connected directly to power analyzer speed and torque inputs. This offers the big advantage of enabling electrical and mechanical power measurements to be evaluated simultaneously, and efficiency calculations to be performed continuously.
Motor, drive, and system efficiency
Inverter efficiency in its simplest form is calculated as output power divided by input power, and represented as a percentage. One method used to measure input and output power is simply to connect power meters on the input and output, with the readings of the two meters used to calculate efficiency.
A more comprehensive method is to use a multiple input power analyzer to measure input and output simultaneously as shown in Figure 1. This results in a more accurate efficiency calculation as it uses a single power analyzer to eliminate potential errors caused by time skew measurements.
With the internal math calculations provided by the analyzer, a very simple, menu-driven computation can be set up to calculate the drive loss and drive efficiency.
Which method should I use?
IEEE 112: Standard Test Procedure for Polyphase Induction Motors and Generators is the U.S. industry standard for motor testing, and it outlines several methods. Figure 7 shows a power analyzer display supporting "Method A" from the IEEE 112 standard in which all mechanical power is divided by the total input to the motor. The standard defines many parameters beyond the current and motor voltage measurements, and it provides instructions for conducting and reporting generally accepted tests for polyphase and induction motors and generators. Additionally, the standard contains 11 test methods to define how to make efficiency measurements in motors.
Test Method A-input-output defined by IEEE 112: The efficiency is calculated as the ratio of the measurement output power to the measured input power after temperature and dynamometer corrections, if applicable. Tests are done at the rated load by the means of a mechanical brake or dynamometer. This rating should be limited to motors with full load ratings of 1 kW or less.
Test Method B-input-output with loss segregation: In Method B, both input and output power measurements are made, but various losses are separated out. Most of these losses merely produce heat that must be dissipated by the motor assembly and represent energy that’s not available to perform work. This method is the recognized testing standard for the U.S. motor industry for motors with full load ratings of 1 to 300 kW.
While both Methods A and B work, Method B requires a lot of instrumentation and is usually only performed by motor manufacturers. Because most manufacturers use Method B and most users prefer Method A, the efficiency calculations between the two may differ. The motor and drive manufacturers’ performance data may use different motor speeds, test loads, or other test conditions.
Conclusion
Many items need to be considered when measuring power in an electric motor, such as total and true power factor. These measurements involve complicated equations, which is why most companies use a power analyzer to generate these results automatically.
After the decision is made to use a power analyzer, decisions on the frequency range and accuracy level must be made. Instrument compatibility is another important aspect in obtaining accurate readings safely, particularly with current transformers. And this is an area where the input/options on the analyzer must be considered. Given correct sensor inputs, mechanical power measurements can also be made using a power analyzer. Selecting the right speed and torque sensors is the first step in determining mechanical power.
Certain power analyzers also enable PWM measurements to be made. However, setting up the analyzer for PWM measurements also requires knowledge about how currents and voltages will affect the power measurements.
A precision high-frequency power analyzer is an important tool for measuring both mechanical and electrical power. Its analysis features and readings can help improve operations and even extend the life of a motor. Selecting the right analyzer and implementing it correctly does require knowledge; however, if employed correctly, the power analyzer data will provide accurate and highly valuable results.
Bill Gatheridge is the product manager for power measuring instruments at Yokogawa Corp. of America, and has more than 25 years of experience with the company in the area of precision electrical power measurements. He is a member and vice chairman of the ASME PTC19.6 committee on electrical power measurements for utility power plant performance testing, a member of the RTCA/DO-160 committee for aircraft power testing, and has worked with an ASHRAE committee on VFD testing.
This article appears in the Applied Automation supplement for Control Engineering and Plant Engineering.