Integrating Ethernet into automation can start at the lowest levels, continue through process control level for controller-to-controller networking, on to the enterprise network level for SCADA and reporting. Ethernet can be the only network used to conduct the business of manufacturing.
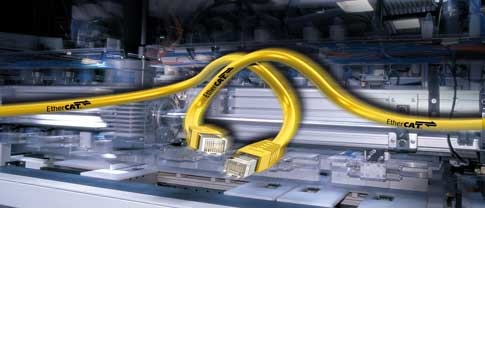
The integration of Ethernet with automation can start at the lowest levels and continue up to the process control level for controller-to-controller networking, and then up to the enterprise network level for SCADA and reporting. When properly selected, industrial Ethernet today can be the only bus needed to conduct the business of manufacturing.
An inexpensive yet high-performance Ethernet-based fieldbus technology will enable the process or machine to perform at the highest levels of efficiency. Through increased performance, higher precision, and better diagnostic capabilities, industrial Ethernet will also lower equipment costs, help manufacturers produce better products, and help eliminate waste and power consumption.
1,000 EtherCAT I/Os in 30 µs
Due to hardware integration in the slave and direct memory access to the network controller in the master, the complete EtherCAT protocol processing takes place within hardware and is fully independent of the run time of protocol stacks, CPU performance, or software implementation. The update time for 1,000 EtherCAT I/Os is only 30 µs, including I/O cycle time. Up to 1,486 bytes of process data can be exchanged in one Ethernet frame, equivalent to almost 12,000 digital inputs and outputs. The transfer of this data quantity takes only 300 µs. One EtherCAT master can communicate with 65,535 slaves in one network.
The EtherCAT fieldbus doesn’t require active infrastructure components (such as switches, hubs, and routers), which lowers the cost of EtherCAT compared to traditional fieldbuses.
Gigabit Ethernet, wireless
At the process control level (controller-to-controller or master-to-master communication), EtherCAT Automation Protocol (EAP) is an EtherCAT-based communication protocol using IP, independent of the physical layer. As a result, communication via gigabit Ethernet or even wireless is possible. EAP enables communication between controllers to exchange process parameters, distribute non-real-time parameters and data, and configure lower level devices from upper level systems. With EAP, the exchange of high-performance data can be managed in a millisecond cycle. If data routing between distributed machines is required, process data can also be transmitted via UPD/IP or TCP/IP.
While the EAP protocol is not real-time, it does streamline process control data exchange.
Upper level enterprise networks traditionally have been rooted in Ethernet communications, so application in this area is natural. Most good controllers and software masters now support OPC UA, for secure exchange of data and settings. Also, these upper level systems may use standard supervisory control and data acquisition (SCADA) and Internet connections for Web-based connectivity for data storage and remote access.
Ethernet can be implemented at all levels of factory automation. EtherCAT can improve fieldbus communications at the device level, as well as at the controller-to-controller, or "process control," level via the EtherCAT Automation Protocol.
– Joey Stubbs, PE, is North American Representative, EtherCAT Technology Group. Edited by Mark T. Hoske, content manager, CFE Media, Control Engineering, [email protected].
ONLINE
www.controleng.com/archives for July has more information with the online posting of this article.
Key concepts
- Ethernet can be used as the only network for manufacturing business.
- Ethernet can reach from the lowest levels of the plant floor through supervisory enterprise networks.
- EtherCAT protocols can provide Gigabit Ethernet and can be used wirelessly.
Consider this
How many networks do you use? Could consolidation help?
ONLINE extra
Also see related Control Engineering articles about EtherCAT linked below.