Manufacturing execution systems (MES) can help companies measure performance, improve processes, attain productivity improvements, and acquire a general competitive advantage by being faster and leaner.
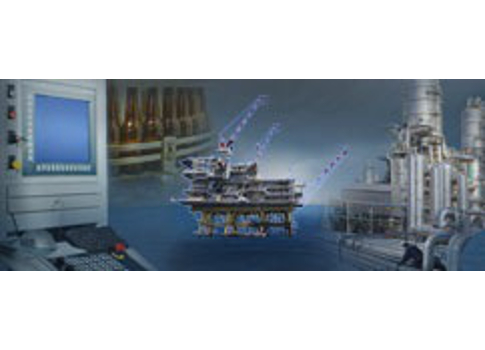
In the current economy, manufacturing industry leaders are often determined by their ability to operate more efficiently, with higher quality, and at a lower cost than their competitors.
One of the methods they achieve those things with is a manufacturing execution system (MES). The MES allows them to measure performance, improve processes, attain productivity improvements, and acquire a general competitive advantage.
The expense of raw materials, employing a workforce, and maintaining facilities are growing, and more companies are starting to understand the benefits of lean manufacturing, improved visibility of everyday operations, and more efficient workflows that result in a better product with a shorter time to market.
MES can help manufacturers realize these benefits by providing detailed, real-time data from the shop floor that can be applied in a continuous improvement program while providing consistent documentation and simple root cause analysis in the process.
With the increased risk that comes with frequent changeovers that are a result of having to offer a large variety of products, having visibility of the immediate production data will provide the necessary time and information to mitigate any factors that may adversely impact a production order.
By delivering constant real-time data of the shop floor processes, MES can enable a manufacturer to better understand where problems exist or improvements may be made.
The detailed information that MES is able to present allows manufacturers to operate in a high speed environment, making crucial decisions on the fly, and provide insight into operations at several business levels.
Here are five reasons why manufacturing companies should invest in MES:
1. Visibility
- Supervisors are provided data in ways that give them awareness of how exactly the production process is behaving.
- The same information, which may include availability, product trails, and current equipment state, among other information, is available to operators on the floor at the same time.
- Real-time statistics are provided regarding the direction of people, equipment, raw materials, and procedures, just to name a few.
- Alarms and other measurements that are out of the ordinary can be noted in frequent status updates, or provided to employees via text or email.
2. Consistency
- MES improves security and consistency by replacing paper document procedures that rely on physical copies that can be lost or damaged.
- The system provides access to documents such as recipes, SOPs, BOMs, genealogy, and other crucial data that the supervisor or operator would otherwise have to search for manually.
- Signatures for completed actions by personnel can be recorded electronically for improved security as well.
3. Productivity
- MES offers the ability to balance personnel, material, and equipment among available resources and is able to schedule these according to constraints such as urgency or resource requirements.
- Because of the precise scheduling of personnel, material, and equipment, orders can be optimized to achieve faster product flow.
- Even with a complex timetable, the system can evaluate and display how long each operation has run, and for periods that take longer than usual, this information can be flagged in reports or sent directly to staff to determine the root cause.
4. Quality
- MES has the capability to compare current production metrics against previous ones, and the older data can be used to determine what might have caused an undesirable result.
- Production data can be put into a format that makes it simple to determine what orders require more research.
- Since the production process is being monitored every second, it’s possible to warn operators of issues when they happen, which reduces the amount of material that needs to be scrapped or repaired.
5. Traceability
- The increasing amount of regulations that manufacturers are experiencing require a stronger focus on genealogy.
- MES is able to link lot numbers from raw materials to WIP materials to finished goods.
- Because of the ability of the system to locate parent components of a product, the risk of a potential recall is decreased with the use of MES lot tracking.
After outlining the gains that follow a successful MES implementation, it’s easy to see that the advantages for a business are immense. It’s not hard to calculate how many hours of labor can be saved or how much money is saved on product, but it’s also important to consider that most of the actual value comes from benefits that are not so easily measured.
This post was written by Russ Durham. Russ is a developer at Maverick Technologies, a leading automation solutions provider offering industrial automation, strategic manufacturing, and enterprise integration services for the process industries. Maverick delivers expertise and consulting in a wide variety of areas including industrial automation controls, distributed control systems, manufacturing execution systems, operational strategy, business process optimization, and more.
Maverick Technologies is a CSIA member as of 9/20/2016