Smaller, more compact energy-efficient servos have faster response time speeds, higher accuracy and dynamic intelligence, along with advanced capabilities. Four enabling technologies are at work.
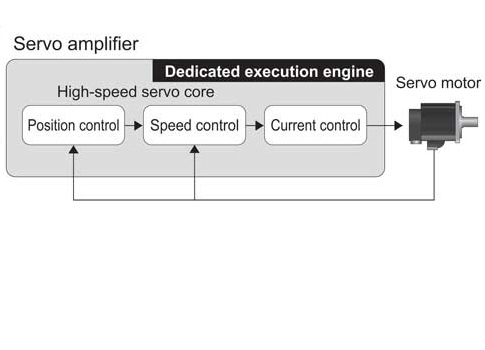
Like many types of electronics and electrical equipment, the trend for ac servo manufacturing technologies has always been toward “smaller, faster, better” and will continue for the foreseeable future. From the advent of ac servos, manufacturers have historically focused on developing high-speed, high-precision amplifiers packaged in the most compact footprint possible. In recent years, features and capabilities relating to energy management, networking, preventive and predictive maintenance, and operator safety are steadily gaining in importance for original equipment manufacturers (OEMs) and end users as they continue to leverage ac servo technology to boost productivity while reducing waste and inefficiency in their operations.
Today, new applications and opportunities in mega-market-growth areas, like smartphone and medical devices manufacturing, are pushing ac servo manufacturers to their limits. Servo manufacturers must continue to find new ways to innovate and deliver even greater productivity and performance with new product development while using available technologies. Four key trends in ac servo design and manufacturing—improvements in semiconductor design, algorithms, monitoring and estimating of machine characteristics, and silicon-carbide power modules—are advancing performance levels and productivity in manufacturing and plant operations.
Semiconductor manufacturing
Internal central processing units (CPUs) and application-specific integrated circuits (ASICs) are the engines driving ac servo technology and performance. Speed, processing power, and response times of ac servo systems are the key factors in realizing superior performance, productivity gains, and throughput in manufacturing operations. Quantum leaps in speed, accuracy, and precision are thanks in part to, or made possible by advancements in, new semiconductor manufacturing technologies.
Among advancements is system on a chip (SoC), where the CPU and ASIC are combined into one integrated chip, offering two main benefits to ac servo designers. CPU and ASIC integration halves the number of components used and contributes a smaller overall amplifier package. For this reason, some ac servo manufacturers are moving away from system in a package (SiP) configuration, where the CPU and ASIC reside on one printed circuit board, and toward SoC configuration.
Servo manufacturers that employ an SoC configuration will significantly increase processing speeds and accuracy, and reduce the footprint of ac servo packages. Saving space saves money.
Control theory
Modern control algorithms are based on a classical PID theory and have been at the core of servo control algorithms since their inception. Newer control techniques are continually incorporated to increase the intelligence of the control algorithm, delivering advanced features and operation. In recent times, ac servo manufacturers began using new techniques like feed-forward control to run their servo control algorithms. Servo manufacturers also are incorporating vibration suppression controls and disturbance control functions to measure friction due to the response of the machine and for other advanced capabilities. Using these new calculations and techniques inside the servo control algorithm dramatically shortens cycle times. While the discussion of control theory may be technically more complex than most OEM designers desire to know or can appreciate, the “real-world” benefits result in faster system tuning and setup, which reduces labor costs.
Machine characteristics: monitoring, estimating
A few years ago most ac servo manufacturers were primarily concerned with machine motor performance, but thanks to faster and more intelligent CPUs, today’s advanced ac servo systems can now monitor and estimate machine characteristics as the machine ages over time. An example would be the estimation of load inertia from the relation between the input and output. This can be easily adjusted and corrected with a couple of gain parameters. This information is valuable in establishing predictive and preventive maintenance schedules to help a machine stay in production at peak performance levels.
With the latest development of next-generation CPUs, servo manufacturers can accurately control inertia mismatches and vibration frequencies of a machine compared to previous generation amplifiers. Over time, every machine’s performance will begin to suffer from normal operation, wear and tear, and vibration. By adjusting a few gain parameters and applying a machine resonance filter and/or vibration suppression filter, end users can dial back the machine to levels at which it was originally installed on day one of operation.
Essentially, this improved estimating of machine characteristics helps users maintain day-to-day peak performance levels for equipment, and lower total cost of operations (TCO) and maximize overall equipment effectiveness (OEE), since the life of the machine will be extended due to more effective maintenance, service, and production planning.
Silicon carbide power module
Power devices are used in motor control and power conversion devices in wide-ranging sectors, such as electric home appliances, railcars, industrial equipment, and automobiles. While silicon (Si) has historically been the primary material used, silicon carbide (SiC) has attracted considerable interest as a next-generation material in recent years for improved energy savings and lower temperature operations. This interest is based on the outstanding low loss properties exhibited by SiC, which enhance power conversion efficiency and help reduce CO2 emissions, with potential to help reduce the size and weight of a variety of devices.
All ac servo manufacturers have faced similar challenges of dealing with energy loss and high heat generated from using isolated gate bipolar transistor (IGBT) intelligent power modules. Now with the advent of new SiC materials, servo systems can become even more compact and energy efficient in the near future.
These four identified trends are critical today, but tomorrow ac servo manufacturers will continue to search for new ways to innovate and improve their servo product designs to serve market demands of “smaller, faster, and better.” Smaller, more compact energy-efficient servos with faster response times, speeds, higher accuracy, dynamic intelligence, and advanced capabilities will continue to result.
– Sunny Ainapure is senior product manager ac servos, Mitsubishi Electric Automation Inc. Edited by Mark T. Hoske, content manager, CFE Media, Control Engineering, [email protected].
ONLINE
www.meau.com
At www.controleng.com, search servo motors for more on this topic.