Motor drives, power-switching transistors and microprocessors, sophisticated control algorithms, software influences, and mechatronic integration are among the standout electronic motion control developments.
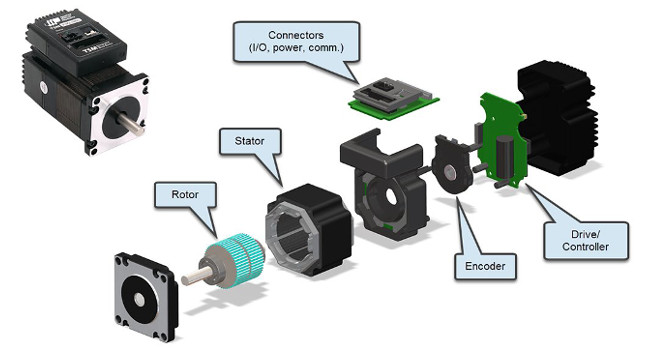
Perhaps the pace of developments has slowed over the past six-plus decades, yet innovations continue in the maturing technologies of electronic motion control. Five developments in electronic motion control are anticipated to continue to drive advancements.
1. Electric motor drives
Electric drives power myriad manufacturing and process lines worldwide. Variable frequency drives (VFDs), delivering reliable speed and torque control of the industrial workhorse ac induction motor, represent one of the biggest developments over time. The ability of newer-model VFDs to also control permanent-magnet ac synchronous motors adds to their versatility. Servo and stepper drives have also made remarkable performance advances in torque and position control of various types of servo and stepper motors. They complement the scene at their respective lower power ranges (Refs 1, 2).
Hardware and software innovations were the enablers for these electric drives. Prime hardware developments include power-switching transistors and microprocessors. The second category comprises new software tools that allowed execution of sophisticated control algorithms not possible in the past. With wider availability, software also made electric motor drives more user friendly.
Dramatic size and weight reductions have especially been realized in VFDs. Bulky cabinets gave way to compact electronic housings that could be located near motors to suit specific manufacturing plant layouts — even mounted on the motor, depending on power needs of the application. In the 1990s, a class of so-called “microdrives” sprang up, which included a 0.19 kW model able to fit into a technician’s shirt pocket. This is an impractical application, yes, but a vivid illustration of possibilities.
Although smaller than VFDs, servo and stepper drives also have benefitted from ongoing electronic controls miniaturization. Newer features include growing intelligence built into all types of drives, such as diagnostics and motor/drive tuning — and connectivity to various bus networks for communicating with higher-level control systems or multiple motion axes.
2. Power-switching devices, microprocessors
Power-switching transistors that shape input current/voltage waveforms for motor control are at the heart of electric drives. The silicon-controlled rectifier (a type of solid-state switch) and the gate turn-off thyristor (a power semiconductor) served the power-switching role in the early drives. They represent matured technology and see limited application, mainly in some large-power drive applications.
With the proliferation of computers and digital technology, motor drives moved to digital microprocessor (MPU)-based designs that continue to dominate the scene. A newer class of semiconductor, the insulated-gate bipolar transistor (IGBT) came along, which has become the prime power-switching device for present-day electric motor drives. IGBTs combine best features of a metal-oxide semiconductor field-effect transistor (MOSFET) input and a bipolar transistor output. They provide fast switching and lower losses due to the insulated gate, among other features (Ref 3). IGBT advances, for example, include faster switching speeds and the ability to operate at higher voltages.
Microprocessors and digital signal processors (DSPs) also are continually increasing their capabilities. Higher computation speeds allow faster response to load dynamics and near real-time communication with other parts of the motion system (Ref 4). Memory is becoming virtually unlimited as developers can squeeze more capacity into microchips. All this permits more sophisticated motion control algorithms to be implemented in software and hardware.
3. Control sophistication
Versatile ac variable-frequency drives offer three principal motor control methods (Ref 5). Open-loop control (also called Volts per Hertz (V/hZ) or scalar) was the first and simplest method to come along. It provides reasonable speed regulation and runs without a feedback device.
Flux-vector control (FVC) is at the highest level of VFD performance and has several variations. Its most capable version is field-oriented FVC, which models characteristics of the dc motor to ac motors, via independent control of flux-producing (magnetizing) and torque-producing current components to derive optimal control of motor torque and power.
FVC uses a feedback device (usually an encoder) to obtain motor shaft position and speed information. Control algorithms rely on sophisticated motor models and implement separate speed and torque loops. Full vector control can deliver high torque at low speeds — even near zero rpm.
Between the above extremes lies sensorless vector control (SVC) — also called open-loop vector control — still another alternative to improve low-speed torque, speed regulation, and starting torque capability over V/Hz drives.
While SVC drives work without a feedback device, they can estimate — using motor current and voltage signals — torque current, magnetizing current, and the vector relationship between them necessary for precise motor control. Hence, they also rely on an accurate motor model. A limitation here is loss of good motor parameter estimation below, say, 90 rpm (for 1,800-rpm base-speed motors). Newer VFDs offer all control types noted above, even V/Hz, because of its usefulness in certain applications.
Direct torque control (DTC), another advanced electric drive technology, controls motor torque and speed directly without the need for separate voltage and frequency control (Ref 6). DTC provides independent control of an induction motor’s magnetic field (flux) and torque using motor current and voltage information — without motor shaft position or speed feedback. In addition, DTC works with permanent magnet synchronous and synchronous reluctance type ac motors.
DTC eliminates the need for a modulator stage found in pulse-width modulated (PWM) drives described above. This can reduce an inherent delay between processing motor parameter measurements and executing control commands. It requires a very accurate motor model and a DSP able to compare instantaneous torque and flux with reference values, at intervals of 12.5 microseconds.
For their part, electric servo systems offer the most accurate motion control method available today, delivering extremely fast loop closure for dynamic positioning response. Field-oriented control is extensively used in servo drives (Ref 7). Servo motion uses encoders, resolvers, and other feedback types for motor status information. However, extremely high-resolution feedback is required to obtain the ultimate point-to-point load positioning and smooth, accurate trajectory control between movement points.
4. Software influences
The equations and motor models were available early on, but their implementation into software for dynamic motion control programs and algorithms had to wait until computers became commonplace. In parallel, continual performance improvement occurred in MPUs, digital signal processors, and microchips for executing programs in motion controllers and motor drives. Higher execution speeds and huge memory growth were made possible.
One result was the ability and the economic rationale to incorporate multiple motor-control topologies noted above in the same electronic drive. A simple software parameter change could thereby change control modes.
Another aspect of motion control software is assistance in the set-up of an electronic drive/motor combination — especially for servo drives (Ref 8). Tuning algorithms in adaptive controllers can continually adjust servo tuning gains. This kind of intelligence built into a drive also can sense other parameters, such as motor temperature changes and control disturbances to enhance motion system performance.
At the user level, PC-based motion control software packages are available on the market. Features of these software tools include set-up and configuration of motion system elements, preprogrammed motion functions, software wizards, dashboards and more. Interactive point-and-click and graphical programming interfaces are provided. Common programming languages and development environments are available.
Simulation is a further area of software innovation. It allows “virtual prototyping” of motion control systems in software before building hardware. This can show how well the design might work, check out complex motion system details, and explore potential design trade-offs and alternatives. Simulation software can reduce cost and time needed to develop the motion control system. For example, it can cut physical testing, but not eliminate it. Still, simulation is not a panacea; it has to be applied with care and practical engineering sense (Ref 9).
5. Mechatronic integration
Mechanical and electronic systems traditionally worked as physically separated units. The motion control arena experienced a huge change in this regard in the mid-1990s when electric motor and control integration came on the scene in a big way (Ref 10). A flurry of products was introduced by many manufacturers — first as combinations of ac induction motors with VFDs in one package, so-called integrated motors. Then similar combined units became available for servo and stepper motors and their respective controllers (Ref 11).
Various benefits can be attributed to having control electronics onboard motors — for example, lower installation costs without long cabling between motors and drives and associated conduit trays, fewer system components, easier diagnostics and maintenance, and simpler control architecture (Ref 12). However, integrated motors have experienced less success than expected, mainly in the induction motor and drive sector. Perhaps this is due to fewer favorable applications or user ambivalence. Still, these induction motor/drive combinations remain in the market for sizes up to 22 kW, serving appropriate applications and in hybrid control architectures.
On the other hand, integrated servo and stepper motors have done better. More suppliers are providing these units with more product sizes being introduced. A case in point is a very recent example of integrated motors development (Ref 13). Smaller physical size and power of these integrated motors also favors more applications.
As electronic motion control matured, its application in manufacturing plants expanded to serve multiple motion axes. This has promoted decentralized or distributed control architectures, which connect to the overall plant control system via fast communication networks. Such hybrid architectures favor integrated motors of all types. The extent of electronic integration can be tailored to the specific production line. All control electronics need not be inside a servomotor or atop an induction motor, just nearby, to derive some of the benefits.
In the larger view, mechatronic integration goes beyond combining best practices of mechanical and electronic design to include control system and software developments. In fact, software has added to the success of mechatronics (Refs 14, 15). The ability to simulate motion control systems without the need to build multiple hardware prototypes has been a key advance, as noted earlier. The software element of mechatronic design — once limited to only large engineering departments — has been able to filter down to wider applications and more users as software tools became easier to use, more affordable, and deployable on industrial PCs.
Today, the road ahead remains open to continued developments in these five areas of electronic motion control.
Frank J Bartos, P.E, retired, is a former Control Engineering executive editor and consulting editor. [email protected]. Edited by Mark T. Hoske, content manager, Control Engineering, CFE Media, [email protected].
KEYWORDS: Motion control, motor control, VFDs
Five trends in motion control shaped the past and guide the future.
Motor drives and power-switching transistors and microprocessors
Motion control algorithms, software influences, and mechatronic integration.
CONSIDER THIS
Which key motion developments do you need to advance motion control optimization?
References
1. Electronic motion control, then and now (2014)
2. Step-motor-based systems stay competitive (2013)
3. AC Drives stay vital for the 21st century (2004)
4. Microchips doing more for motion control (2010)
5. The 3 (or more faces) of ac variable-speed drives (2001)
6. DTC: A motor control for all seasons (2013), an ABB white paper Adobe PDF file
7. Got Field-Oriented Control in Your Servos? (2004)
8. Servo System Application Tips (2006)
9. Simulation software in motion control (2010)
10. Integrated Motor-Drives Seek Wider Market, User Acceptance (2000)
11. Integrated, Intelligent Motors & Controls Will Be in Your Future (2001)
12. Integrated motors and drives: Benefits and solutions (2016)
13. Integrated motors offer flexibility (August 2019)
14. Simulation widens mechatronics (2007)
15. Mechatronic integration facilitates control system design (2013)