Like most vision-enabled systems, 3D bin picking relies on compatible peripherals and sophisticated software.
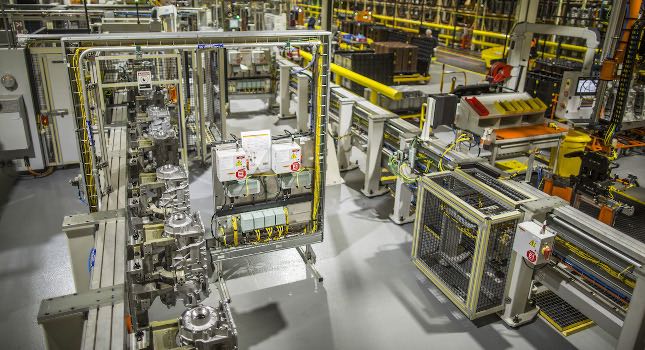
3D bin picking insights
- There has been a shift towards automated 3D bin picking in various industries, focusing on the use of advanced technologies like 3D vision and artificial intelligence to streamline operations and reduce expenses.
- There are complexities involved in implementing these systems, including the need for suitable hardware and sophisticated software and suggests considering the broader operational context for successful adoption.
The use of manual labor for picking and assembling components has long been central to manufacturing. Although it has proven effective over the years, manual bin picking is a slow, detail-oriented and repetitive task that inflates manufacturing costs. For many manufacturers today, increasing productivity while at the same time lowering manufacturing costs and improving product quality is high on the priority list. Selecting parts from a bin isn’t a difficult task for human operators but is it the best use of those resources?
In many high-volume manufacturing environments, the shift to automated bin picking has been taking place for several years, but what is trivial for a human isn’t always as trivial for automation. Conventional bin picking relies on 2D images to identify which objects to pick and where to place them. It requires that objects be properly placed or kitted in the bin so the imaging system can analyze them. These systems have been used successfully in sectors where the part quantities are known and limited, such as in automotive assembly, for years.
The advent of 3D bin picking has significantly expanded the field of potential applications and industry segments by incorporating a third dimension to the analysis process. This enables the bin picking system to work with higher volumes and variations of parts, which may be randomly arranged in a bin. Using 3D vision, robots can identify the correct part for each step of the workflow and select it accordingly.
Robotics, vision and software
Like most vision-enabled systems, 3D bin picking relies on compatible peripherals and sophisticated software. Along with a 3D vision system, builders and integrators must select a robot with adequate range of motion and an appropriate gripper for the application. Aaron Donlon, product manager at Epson Robots, said, “6-axis robots are ideal for bin picking since the parts tend to be lying on top of one another in random formation.”
Software and communication protocols must also be carefully integrated to ensure smooth operation and robustness of the system. At 3D camera manufacturer Zivid, product marketing manager John Leonard noted 3D machine vision has converged with other emerging technologies, “Particularly AI and deep learning to make the detection and picking of parts adaptive and intelligent.”
At Photoneo Inc., senior product manager Dušan Petráš believes that while AI will continue to have major impacts, it is the development in handling, gripping and manipulation technologies that will be the prominent driver in 3D bin picking capabilities.
Petráš said, “Any 3D picking solution relies on technologies that can handle objects with proper care, and we are seeing major advancements in materials and technology unlocking new applications that cannot be addressed by traditional suction or magnetic grippers.”
Traditionally, bin picking has been prevalent in manufacturing — automotive, aerospace, white goods and general assembly and continues to thrive in these environments. Optimal industries for adopting 3D bin picking are those where product sets are controlled and well known. This makes it easier to create 3D models for image matching, which results in higher accuracy of the bin picking system. Logistics applications use bin picking, and as this sector grows and expands, it continues to offer excellent potential for increased use of 3D machine vision technology. Also, applications involving the use of sheet metals or reflective materials, which are challenging for conventional vision systems, are good candidates for employing the power of 3D vision and picking.
Challenges of deployment
Despite technological advancements and the growing number of companies developing and supplying 3D bin picking systems today, integrating those systems can be far from trivial. At RightHand Robotics, Senior Product Manager Annie Bowlby draws a key distinction between applications where the bin picking system is integrated alongside human-centric workflows versus fully automated ones. “If this is a retrofit, constraints around safeguarding can impact robot arm reach and overall throughput, whereas with a greenfield installation, the bin picking application can be used as a starting point for your entire layout to create optimum throughput,” Bowlby said.
Beyond installation type, system designers must meet other challenges typical of vision system deployment. For example, are the parts arranged in a consistent manner or are they randomly assorted in a bin? Dark, reflective or generally poor contrast parts require high dynamic range image sensors. The environment itself is a factor when considering the effects of vibration, dirt, humidity and temperature, as these can all affect the quality of the vision system and the function of the robots and grippers.
Petráš sees the solution to overcoming barriers as having the right mind-set from the start. “Instead of focusing on rigid expectations and the customer’s perspective of what they want,” he said. “We must approach the application from the perspective of the challenge or problem and how to best solve it.”
Advice for new adopters
Among those with experience designing and supplying components for bin picking systems, there is abundant consensus on at least one thing: the bin picking system shouldn’t be thought of as an isolated element in the manufacturing process. To ensure the greatest odds of success, companies seeking to adopt the technology need to view the entire workflow of their operation holistically. From Bowlby’s perspective, “Choosing integration partners who are both experts and willing to articulate an entire vision as opposed to a single element will help to create a successful, cohesive system.”
Donlon emphasized conceptualizing a design and simulating results often isn’t enough: “We highly recommend testing real parts with a clear understanding of the environment where the system will need to perform, complete with the variations that it will encounter.”
This level of rigor can add to scope, complexity and project timelines but in the long run will pay off in terms of actual results, accuracy and reliability of the implemented system. A holistic design helps to validate the interoperability of system components and lends confidence the vision systems and other precision elements will retain calibration in deployment.
The role of vision and AI in the future of bin picking
Although 3D bin picking already relies heavily on machine vision, and industries are starting to see the effects of machine learning in these applications, the belief is we are only scratching the surface of our potential. At Zivid, Leonard noted that “breakthroughs in 3D imaging capability have made it possible to capture 3D point clouds of transparent items, something that has recently been seen as impossible.”
This advancement could open the door to potentially new applications for 3D vision and bin picking that are currently served with manual labor. With the ongoing maturity of image processing sophistication, we can also expect to achieve increases in the reliability of 3D point cloud processing, bringing with it improvements in overall system performance.
Finally, the inclusion of machine learning in image processing and object identification also has the potential to lower barriers to entry for 3D bin picking by leveraging AI to bridge gaps in data quality and expand the availability of entry-level systems. This may entice new industries to start evaluating automation in place of manual process, resulting in a broadened landscape and an increased addressable market for everyone.
– The Association for Advancing Automation (A3) is a CFE Media and Technology content partner.