The first step to bringing fieldbus networking and the Industrial Internet of Things (IIoT) into process manufacturing plants and refineries may be changing device-level networking practices.
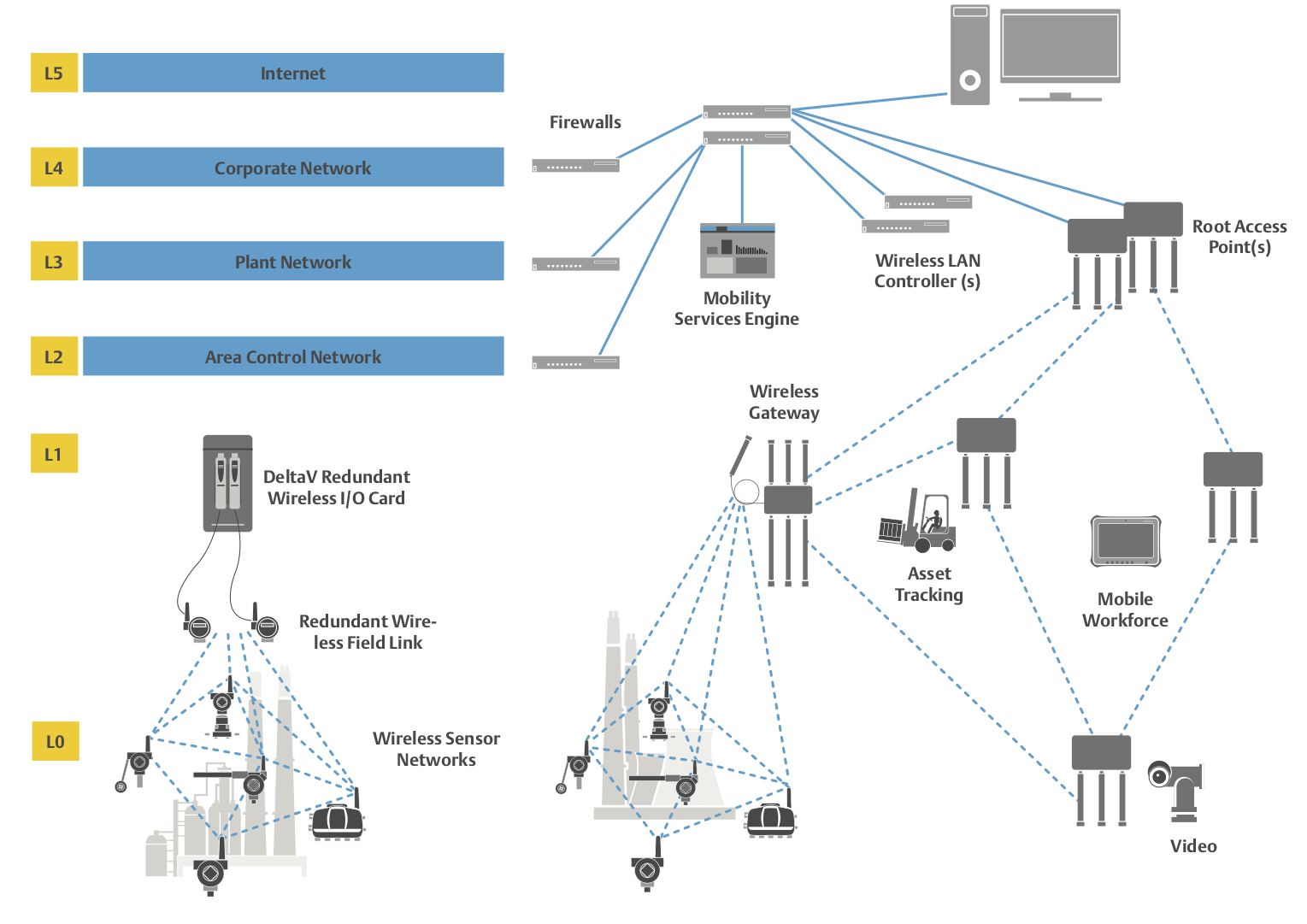
As the digital transformation of process industries has unfolded the last few years, wireless device-level networks are an important implementation element, extending the reach of higher-level networks to the process itself. The Internet in and of itself connotes wireless Ethernet such as Wi-Fi, but process industry complexes have enormous populations of field instruments and actuators using analog and digital fieldbus communication. Wi-Fi has not been adopted for these devices and there are no signs of a change in that direction.
What has happened is the adoption of wireless communication for device-level networks. The leading protocol for this purpose is WirelessHART, which has grown steadily in hardware availability and deployments since its first release in 2007, and its adoption as global standard IEC 62591 in 2010.
Emerson Automation Solutions uses WirelessHART, but since it is a global standard, all devices certified by the FieldComm group interoperate regardless of the supplier. Emerson was an early adopter and has provided equipment using WirelessHART since its inception. Its transmitters and gateways are installed on more than 38,900 networks. This record of service puts to rest any questions about WirelessHART reliability and performance.
In the real world
WirelessHART deployments reduce instrumentation installation costs by eliminating expensive cabling. The cost of adding a wired instrument in a refinery can range anywhere from $5,000 to $50,000. Avoiding that cost should be welcome. Nonetheless, the heavy refining and petrochemical industries don’t adopt new technologies on a whim, even if promised a cost reduction of 75%. Given the potential harmful consequences of a bad decision related to something as complex as the Industrial Internet of Things (IIoT), or even WirelessHART, it must be reviewed extensively beforehand.
Internal teams try to think through the risks and the pros, and cons of a new technology. They consider where appropriate applications can and should be used, along with areas where they should be avoided.
Early on, many companies had to be convinced that WirelessHART was as reliable and easy to work with as advertised, so they often launched small deployments in the least critical parts of their plants to prove the concept. Nowadays, few users go to such lengths, but some still need convincing.
Emerson works with end-user companies on technology review programs for WirelessHART. Some questions and discussion points are specific to a company or site, while other, more universal considerations, also have emerged. To help those considering WirelessHART and larger IIoT concepts, some of these points are outlined below.
What is WirelessHART?
IEC 62591 WirelessHART (Figure 1) was developed by the HART Communication Foundation (now part of the FieldComm Group). This wireless protocol is based on the traditional 4-20 mA wired HART protocol. It leverages existing instrumentation practices for deploying and maintaining instrumentation, but without the traditional cost of running signal wires and supporting infrastructure, including junction boxes, cable trays, marshalling cabinets, and others.
WirelessHART networks use the 2.4 GHz spectrum, with up to 15 channels able to operate simultaneously and coexist with each other. It also coexists with 802.11 Wi-Fi systems operating in the same spectrum. All transmissions through the network are encrypted, with additional security features available on the gateway for secure integration into the host system.
The key infrastructure requirement for a WirelessHART network is a gateway that manages the wireless network. It also integrates process data and diagnostic data into the host system via a hardwired Modbus RTU, Modbus TCP, OPC, HART IP, or Ethernet IP connection-as well as with other vendor-specific protocols.
Application selection
Figure 4. WirelessHART adapters, such as the Emerson THUM, can be added to any HART 5.0 or later device. Courtesy: Emerson Automation Solutions[/caption]
However, moving back to the earlier box, not every type of process instrument is suitable for battery power, hence the question: Can an adapter be used? A WirelessHART adapter (Figure 4) can be added to any HART 5.0 or newer device. The adapter sends the primary process variable and additional data to the host system via the gateway.
In some cases, an adapter is added to instruments already wired via 4-20 mA to capture secondary variables and diagnostic data. In other situations, adapters are added to instruments such as a Coriolis flow meters, where power consumption is too high for internal battery power. Adapters usually don’t have internal power, so in some cases it may be necessary to provide wiring to the instrument and adapter setup to carry power, although not to carry the signal. This usually is not a problem. In most process plants a suitable instrumentation-grade dc power source is available near the installation.
If the application is appropriate and the mechanical issues solvable, WirelessHART device use can proceed. It may seem the winnowing-out process is too severe, but in real-world environments, the number of practical applications often is higher than initially expected.
Gateway requirements
In basic terms, the gateway receives data from the WirelessHART instruments and conveys it to the larger plant networks and host system. Since this represents a single point of failure for the instruments communicating with that gateway, most plants use a redundant system (Figure 5). Because gateways integrate into plant networks different ways, this area requires review.
The growing availability of WirelessHART equipment condition monitoring sensors (Figure 6), such as the vibration and bearing condition sensors deployed on critical rotating equipment should be considered. Sensor data usually does not need to go to the main automation host system since the data doesn’t affect process control. Where data from all sorts of devices-both monitoring and process-come in through one gateway, a plant may divert some data to the control room while other data goes to maintenance department platforms, such as for asset management.
As WirelessHART networks get larger to cover more areas, most plants adopt multiple networks run in parallel. Keeping similar devices associated with each other makes it easier to send data to the right destination. This segmentation must be approached methodically to ensure appropriate numbers of devices are on each network to support effective meshing, with enough redundant paths for individual transmitters to communicate with each other.
Distance and network density
WirelessHART uses self-organizing mesh networking. Individual wireless devices automatically communicate with each other and adjust communication paths to use each other as data relay points; if a given device cannot reach the gateway directly. Consequently, the more devices within reach of each other, the more reliable the communication. The system engineering guidelines IEC 62591 WirelessHART provides an in-depth discussion of networking mechanics and is an excellent reference manual. Fortunately, designing an effective network is not a complex undertaking. By following a few basic best practices, most plants can expect wireless reliability of more than 99%.
Some of this can be determined by simple proximity and expected transmission distances. Getting more positive performance data depends on using network diagnostic tools provided by the gateway manufacturer. Since the gateway manages the network, it should include tools that show how the network has organized itself. Sophisticated tools (Figure 7) indicate how communication paths formed, as well as their reliability. If there are parts of the network where meshing opportunities are too few, an additional transmitter can be inserted to act as a repeater while generating no data of its own.
WirelessHART radio transmissions are robust and can cover long distances, despite their low power use, but are subject to limitations. The massive steel structures common to refineries and chemical plants must be considered, and the conditions under which signals are reflected or absorbed can be difficult to predict. Site surveys to plot suitable transmission paths can be helpful, but network performance analysis is best. A wireless planning tool can help evaluate your facility against deployment industry-best practices.
Rules of thumb developed by one refinery bases viable transmission distance on equipment density, as follows:
- Heavy obstruction: 100 ft.—Typical heavy-density plant environment, too congested to drive a truck through the area.
- Medium obstruction: 250 ft.—Less dense process areas, lots of space between equipment and infrastructure.
- Light obstruction: 500 ft.—Typical of tank farms where there are big obstructions but with lots of space between.
- Clear line of site: 750 ft.—The maximum distance is possible when the antenna is mounted above obstructions, and the angle of the terrain change is less than 5 degrees. Specialized antennas help span even longer distances.
These are guidelines. Actual results may vary, but these estimates should provide realistic expectations.
Being a champion
WirelessHART networks have proved effective at self-organizing. Many networks operating today were installed, turned on, and for all practical purposes, simply started working. Their built-in capabilities do the job as expected. However, the smartest software cannot overcome physical hardware constraints.If some part of the network is underperforming, the antenna for a certain transmitter may have to be moved to a better position or a repeater added to create an additional communication path. A few simple actions can improve performance, but someone must take the initiative to perform them.
There’s more to implementing IIoT concepts than simply installing WirelessHART networks, but this form of communication extends the ability to reach down into the networking architecture. The need for this is changing as the nature of industrial automation evolves.
Distributed control systems (DCSs) and asset management platforms tended to be large and monolithic but are now supplemented and replaced by smaller, less overhead-intensive systems using mobile devices and the cloud. For example, the mechanical condition of a centrifugal pump installation can be checked via a smartphone app. The app can reach back through the plant networks and gateway to the WirelessHART diagnostic sensors installed on motors and pumps.
While the same app should reach a wired device to acquire similar data, the communication path may be too complex to be practicable. Conventional HART devices typically send data to an input/output (I/O) card of a DCS or other host system, so the app must find a path through the equipment, which, depending on its age, may be easier said than done.
Therefore, the value proposition for WirelessHART is growing in the IIoT age. To the cost savings associated with eliminating wiring, add the advantages of easier accessibility. This may be more difficult to quantify, but it delivers quick payback for many applications.
Dan Carlson is a solution architect at Emerson Automation Solutions. He holds a Bachelor of Arts in Physics from Carleton College, and a Master of Business Administration from the University of Minnesota. Dan has been with Emerson for 15 years, working on wireless technology and applications.
This article appears in the IIoT for Engineers supplement for Control Engineering and Plant Engineering.
See other articles from the supplement below.