Modern instruments employ advanced digital technology to enhance accuracy, reliability and ease of use in liquid analysis applications.
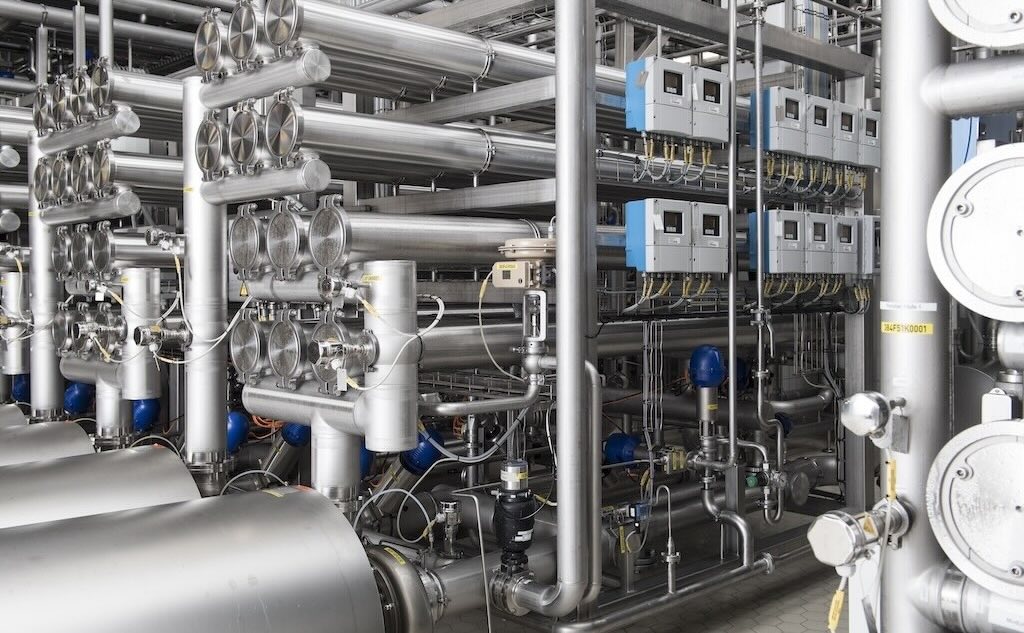
Learning Objectives
- Understand how digital analytical instruments for liquid analysis can help improve digital transformation.
- Learn about the role process sensors can play in gathering and synthesizing data for engineers.
Process instrumentation insights
- Traditional analog sensors for liquid analysis were prone to environmental interference, required meticulous calibration, and were challenging to maintain, leading to significant time and resource investments.
- Digital sensor technology revolutionizes liquid analysis by eliminating environmental vulnerabilities, enabling lab-calibration, and drastically reducing calibration and maintenance time, ultimately enhancing safety and efficiency in various industries.
Liquid analysis has become increasingly important in many process industries, including but not limited to water/wastewater, food and beverage, dairy, chemicals and pharmaceuticals. Monitoring — and responding to changes in — relevant parameters is essential for improving product quality, optimizing yield, and ensuring safety as well as regulatory compliance and environmental protection.
In the past, online process liquid analytical measurements were made using basic analog instruments with limited diagnostic and measurement quality parameters, but today, digital communication protocols and smart instrumentation have significantly expanded sensor functionality and user-friendliness.
Analog sensor limitations
Before digital protocols were developed and deployed at scale, liquid analysis was typically conducted using basic analog instruments, each comprised of a sensor, cable, and transmitter, to make online process measurements. The measured process variable from each instrument was then sent to a supervisory, control, or other host system via a 4 to 20 mA analog signal.
These instruments were often cumbersome to work with, requiring meticulous reagent setup, for instance.
The analog transmission between sensor and transmitter was susceptible to moisture ingress at connection points, in addition to corrosion, salt bridge formation, and electromagnetic interference — all of which could adversely affect the raw signal received by the transmitter, before even sending the scaled value to the host system via a 4 to 20mA current signal.
On top of environmental factors, sensor cables and transmitter idiosyncrasies could degrade a measurement value, so these nuances had to be included in calibration procedures. These issues preclude calibration in a laboratory setting, instead requiring technicians to transport calibration equipment to the field site and perform calibration in potentially difficult or hazardous conditions. Calibration in the field also typically took much longer than in the lab. For example, calibrating a single pH loop can take 40-60 minutes and often requires more than one technician.
Basic analog sensors are not only challenging to calibrate, but they also are complex to commission and difficult to maintain due to the lack of instrument health diagnostic indicators. As a result, plant personnel inevitably spend a great deal of time and resources on configuration, troubleshooting and maintenance.
Inductive digital instruments burst the analog bubble
To address these and other issues, inductive digital sensors digitize measured values and relay signals to their transmitters via non-contact connections. Digital signals are unaffected by the aforementioned environmental factors, and galvanic isolation between the sensor and transmitter eliminates potential interference signals.
This type of digital sensor technology also makes laboratory calibration viable because digital communication removes the effects of sensor cables and analog signal transmission on values received by the host system. Key sensor data, including calibration information, is stored in the sensor head, so sensors can be easily exchanged in the field following lab calibration. Having calibrated sensors ready to go minimizes downtime due to device failures because staff can replace a problematic sensor in minutes. Calibration is typically valid for twelve months prior to field deployment, providing a long shelf life for pre-calibrated replacements.
Compared to the hour or so required for field calibration, a digital pH sensor can be lab-calibrated in under ten minutes, while simultaneously eliminating the need to transport calibration equipment to the field. Meanwhile, switching out a questionable sensor on the plant floor with a pre-calibrated replacement requires only a few minutes (Figure 1).
Initially developed for pH measurement, inductive instrument technology has grown into a wide-reaching platform for many liquid analysis qualities, including conductivity, ORP, dissolved oxygen, turbidity, disinfection properties, UV/Vis, spectrophotometry measurements, and more. These sensors are capable of driving further improvements in reliability, process management, and predictive maintenance with a host of additional instrument and process information stored (Figure 2). Such parameters include programmable CIP cycles, load matrix of pH and ORP probes, a distinction between calibration checks and adjustments, digital sensor labels, operating hours, and electrolyte consumption monitoring for amperometric disinfection, conductivity, and dissolved oxygen sensors.
Improving sensor accuracy and maintenance in gold processing
In gold mining, cyanidation is a common process for extracting gold from low-grade ore. Cyanide is extremely toxic, and safe cyanidation requires accurate and reliable pH measurement.
A Finnish mining company was experiencing measurement accuracy issues, and staff were spending too much time and too many resources on calibration. Unsatisfied with its current process instrumentation, the company sought to improve safety and efficiency, while reducing maintenance efforts, with new solutions.
The mining company performed a yearlong trial in which they compared instrumentation and services from multiple vendors, and in the end, they moved forward with Endress+Hauser. Working in close collaboration, the team installed inductive digital Memosens pH sensors and transmitters throughout the facility to solve the technical challenges.
Using the aging, previously installed instrumentation, sensor cleaning was difficult, inconvenient and time-consuming, and it had to be conducted manually in the field, which was unpleasant during the winter months when temperatures fell as low as -40 °F. By contrast, the new instruments perform automatic self-cleaning, improving efficiency and staff satisfaction.
Altogether, instrumentation calibration and maintenance efforts were cut by nearly 90% from 2,200 to only 240 labor hours per year after the switch. Decreasing the amount of demanding field maintenance reduced costs and improved worker safety and convenience. In addition, the accuracy improvements provided by the new pH sensors increased cyanidation process safety and efficiency, reducing the consumption of chemicals such as sodium metabisulphite by up to 50%.
High-precision chlorine measurement in vegetable wash water
In food production, cleaning vegetables with a hypochlorite wash improves consumer safety by killing harmful pathogens. Higher chlorine concentrations translate to faster and more powerful disinfection, but before wash water is disposed, chlorine must be neutralized to stringent regulatory limits — potentially as low as 0.2 mg/L. However, many chlorine sensors have trouble measuring at such low concentrations, often entering a sleep mode when chlorine levels remain this low.
To meet the low concentration requirements demanded in this application, one processor installed a cabinet-mounted solution with inductive digital chlorine and pH sensors, a flow assembly, and Liquiline transmitter. The chlorine sensor is designed to measure trace levels of chlorine, and it can be configured to avoid sleep mode, even at low concentrations (Figure 3).
With precise chlorine measurement, bisulfite dosing for chlorine precipitation can be executed with high efficiency, reducing operational costs. Chlorine measurements are transmitted by the installed a transmitter to regulate the bisulfite pump, using a proportional-integral-derivative (PID) controller to maintain a chlorine setpoint of 0.08 mg/L, safely below the 0.2 mg/L discharge requirement.
pH monitoring prevents damage in whey processing
The process of separating whey protein from lactose and minerals uses polymer or ceramic filtration membranes that can be easily damaged in unsuitable pH conditions. During polymer membrane cleaning in particular, pH must be carefully monitored and controlled to prevent such harm (Figure 4).
The ceramic membrane cleaning solutions contain enzymes that break down organic materials in the membrane pores, as well as chemical buffers used to maintain safe pH levels. However, inaccurate pH measurements can quickly compile and cause problems because these systems are frequently cleaned, as often as four times each day.
Unlike polymer membranes, ceramic membranes are cleaned with a caustic solution that does not pose the same risk. However, monitoring is still important during regular operation to prevent damage and ensure effective separation.
A whey processor installed inductive digital pH sensors at the inlet and outlet of each of their process skids to monitor the separation process and prevent damage to its membranes. On separators with polymer membranes, the processor installed sensors inline, which are therefore cleaned during every cycle. For the other application, sensors on the ceramic separators were installed in a retractable assembly to avoid exposure to the caustic solution used during cleaning. These sensors must be removed and cleaned separately.
The setup has remained effective over time, without any noticeable sensor degradation after 300 cleaning cycles, and the low calibration frequency of every six to twelve months is very manageable for the processor.
Digitalization propels liquid analysis
Modern instrumentation with digital data transmission resolves many of the issues with analog sensors, including susceptibility to environmental conditions, lack of instrument diagnostics, and required field calibrations.
These advanced digital instruments help plants continue their digital transformation—improving production safety, process efficiency, and product quality—while maintaining regulatory compliance and optimizing operations in liquid analysis applications.
Thomas Chirdo is the national product marketing manager for liquid analysis at Endress+Hauser. Edited by Chris Vavra, web content manager, CFE Media and Technology, [email protected].
MORE ANSWERS
Keywords: process instrumentation, liquid analyzer
CONSIDER THIS
How can digital analytical instruments help your facility?