ZF Group, an automotive manufacturer, provides motion controls for automotive, industrial, wind power and is using digital transformation on the way to smart factory implementation to meet sustainability requirements.
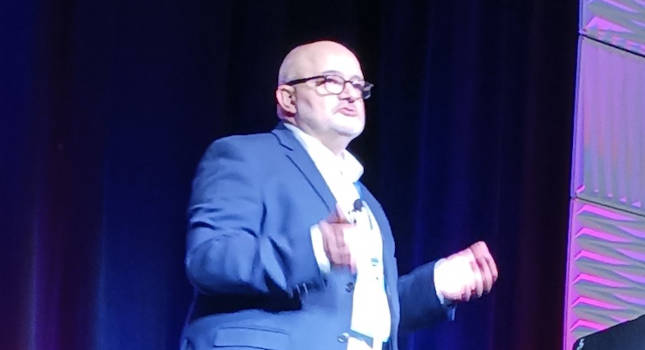
Learning Objectives
- ZF Group, an automotive manufacturer, provides motion controls for automotive, industrial, wind power. Digital transformation on the way to smart factory implementation.
- Smart factory prerequisites are required prior to implementation.
- The 2023 ARC Industry Forum, in Orlando, Feb. 6-9, included discussions about digitalization helps optimize operations, helps with energy efficiency, workforce shortages, supply chain, climate change and cybersecurity.
2023 ARC Industry Forum keynote insights
- Automotive, industrial and energy manufacturer ZF Group provides motion controls for automotive, industrial and wind power. Digital transformation on the way to smart factory implementation.
- Smart factory prerequisites are required prior to implementation.
- The 2023 ARC Industry Forum, in Orlando, Feb. 6-9, included discussions about digitalization, optimization of operations, energy efficiency, workforce shortages, supply chain, climate change and cybersecurity.
For the global automotive industry supplier ZF Group, the hope is to be carbon emissions free by 2040, and, by 2030, an 80% reduction from its plants’ CO2 emissions versus 2019 levels and 40% less CO2 emissions from supply chain and product use versus 2019 levels, according to Gabriel Gonzalez-Alanso, senior vice president, corporate production management, ZF Group.
He was among the keynote speakers at the ARC Advisory Group’s 2023 ARC Industry Forum, Feb. 6-9, in Orlando, and online Feb. 27-March 27.
This year’s forum, according to Peter Manos, director of research, ARC Advisory Group, has more than 860 attendees, 200 speakers, 250 companies, and 70 workshops in 4 days. Andy Chatha, ARC president, in welcoming attendees noted education, sharing best practices and relationship building are endemic to the forum.
Motion controls for automotive, industrial, wind power
Gonzalez-Alanso, who worked for Renault prior to automotive supplier ZF Group, said the ZF Group has 38.3 billion euro in sales and 157,549 employees. ZF supplies primarily passenger cars, but also light commercial machinery with vehicle motion controls, automated driving, integrated safety, electric mobility (small bus). Gonzalez-Alanso noted the non-automotive market includes industrial applications and supplying 25% of global wind power with the ZF gearbox, powering the equivalent of 100 million households.
Digital transformation on the way to smart factory implementation
New technologies are needed to meet sustainability goals, and there’s a need to adapt business processes also. Using agile methodologies leads to better outcomes for innovative topics. It is not cheap or fast, he said, noting ZF has been working at digitalization for 4 years. The effort began in 2019 with seven teams, working on moving from digital transformation to an IIoT ecosystem by pushing digitalization to cloud.
“In DMP, we are one team. We never met during pandemic, over 10 months, but people in Seattle, Detroit and Germany were all working together,” said Gonzalez-Alanso.
The process includes enriching existing technologies, shifting and replacing as needed, harmonizing applications from plant-specific to common solutions, enabled by co-development along the way.
The ZF smart factory of future of the future will be a digital manufacturing platform (DMP) connecting partners via cloud capabilities, such as advanced analytics and optimization, data lake, product lifecycle management (PLM) and enterprise resource planning (ERP). Working with Microsoft and PWC, ZF is creating a ZF industrial internet of things (IIoT) platform in the cloud as one point of information, to be downloaded and applied for fast decision-making for 250 plants globally.
Smart factory prerequisites, elements, applications, benefits
“The purpose is not to reinvent everything,” Gonzalez-Alanso said, “but put what we need in the cloud, download and customize for use. We need to go fast.” Some plants lack certain skillsets and this will help, he suggested.
Smart factory elements will incorporate logistics, quality and inspections, factory management, production maintenance and shopfloor management. Before implementation, however, ZF had to ensure data and infrastructure security, use of standards, digitally-enabled organization and workforce, and Industry 4.0 maturity roadmap, with strategic prefunding to optimize smart factory development, said Gonzalez-Alanso.
Smart factory progress, competitiveness
First plant was medium in size, with 700 personnel. Second had 8,000. Early adopters, up to 8 plants came next, and 2023 will include 48 or more plants. To complete before 2030, the pace will need to increase to up to 100 plants, which may not initially include connectivity all the way to machines.” Even so, he said, “we trust in the system,” expecting 5 to 7% improvements at each plant. Benefits are enhanced productivity, increased efficiency and transparency, flexibility and quicker value to company, along with reduced complexity for the workforce.
The smart factory enables competitiveness, using one global production network, lean standards and digitalized, end-to-end processes, operational excellence and productivity.
With information technology/operational technology (IT/OT) collaboration to solve common problems, step by step, they’re more likely to be able to control factory costs related to people, material and machines. Top management needs to buy into the change process, said Gonzalez-Alanso.
Changes also require additional budget, personnel and training to enable the changes. With everyone’s schedules, change cannot happen without additional resources. Transparency helps.
Coverage from ARC Industry Forum
Control Engineering will post related coverage on the 2023 ARC Industry Forum meeting as it is available.
Petrochemical company shifts attention to digitalization, optimization, sustainability
Automation, IT convergence, standards at ARC Industry Forum
Articles from prior ARC Industry Forums include automation and controls digitalization, interoperability, sustainability and interoperability:
Factories born digital save 10x conversion cost
Digitalization, interoperability help with industrial sustainability
Building interoperable control systems
Mark T. Hoske is content manager, Control Engineering, CFE Media and Technology, [email protected].
KEYWORDS: ARC Industry Forum, ARC Advisory Group, digital transformation
CONSIDER THIS
How are you using digital transformation for smart manufacturing and sustainability.
ONLINE