Albert Kao, CEO and co-founder of the company, offered some background about his company, i-5O, and their work with digital twins powered by computer vision systems.
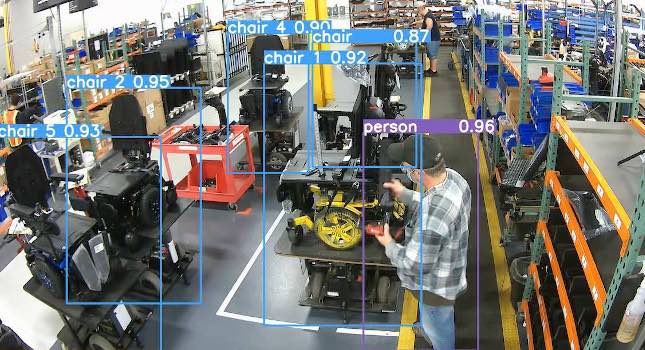
i-5O is an early stage Silicon Valley based start-up that developed a proprietary digital twin powered by computer vision to help manufacturers track, measure and improve their manual production processes. Albert Kao, CEO and co-founder of the company, offered some background about the company.
Question: What is the background of your company, how and why did your company get started?
Kao: Our company’s founding team brings manufacturing experience from Toyota and Schlumberger optimizing and automating both discrete and continuous processes. While working to bring visibility and traceability to manual processes at Schlumberger back in 2014, our co-founder and CTO Khizer Hayat experimented with many different technologies including IoT sensors and wearables and found that none were suitable for tracking manual movements. From this experience, Khizer determined that the best solution was using deep learning powered computer vision software that can replicate the visual observation work performed by human industrial engineers. Back in 2014, Khizer tried to find a supplier that could provide such a solution but found none since at the time, artificial intelligence technology was not yet sufficiently developed to support such an application.
i-5O was started in August 2018 as soon as the deep learning algorithms, hardware and data processing power advanced to the point where they were ready to build a commercial solution.
Question: What problem(s) do your products, software, and or services resolve?
Kao: Despite the advancements in automation and robotics, the fact remains that many processes in a manufacturing environment are difficult and expensive to automate. As a result of this, over 70% of manufacturing tasks today are still performed by human operators. While humans are great for complex operations that require dexterity, flexibility and problem-solving skills, they are not as consistent as machines and contribute to over 80% of process deviations in production.
When manufacturers want to analyze and improve their manual processes, they would currently have to send human industrial engineers to do visual root cause analysis or manual time studies. This outdated technique has been used for over 100 years and is flawed because the data generated is in half hour to one hour samples and human operators tend to perform work at an unrepresentative rate when working under a stop watch. The result is that manufacturers today are essentially running blind when it comes to tracking and optimizing their manual processes.
This is why we have developed a deep learning powered computer vision system that can track the interactions between man, machine and material on the shop floor. Our system continuously and automatically generates time-stamped cycle time data for any process on the shop floor. The data generated by the system can be used to detect manual process deviations in real time and for process improvement projects.
Question: Which specific industries or market segments would benefit the most from your solutions or are your offerings targeted?
Kao: Our offerings are currently targeted for the automotive, medical device, steel, industrial machinery, and household appliances segments.
Question: How do your offerings differ from what else is available?
Kao: Current offerings that are in market today target a single element of man, machine, or material in isolation for optimization. From the experiences that we’ve gained from working on the shop floor, we observed that the primary challenges that manufacturers face were not created by one of these three elements in isolation but rather was the result of the complexity created by the interaction between all three elements. As such, we’ve built our solution so that engineers can visualize the complex interactions that create the most problems.
Question: What are the steps involved with preparing to take advantage of your offerings?
Kao: The most important step to be prepared to take advantage of our offering is to be cloud friendly and have a stable, fast internet connection. Our solution is a hybrid edge and cloud system where we process data on premises and on the cloud to deliver a seamless and modern user experience.
Question: Are you incorporating standards (which ones) to offer interoperability and how?
Kao: Our solution can be integrated with existing database systems using ODBC/JDBC connections.
Question: What transitions are you making from development/startup to commercial availability that would be important for your customers and prospects to know?
Kao: We’re currently working with a select group of forward thinking clients that are eager to leverage the latest developments in AI and have the ability to influence our product roadmap. The lessons from this work are then translated for the mass market.
Question: Where do you see this market and your solutions in 5+ years and what can engineers do now to prepare for the future?
Kao: We see the computer vision and remote monitoring market growing significantly over the next five years because of a confluence of technological advancements in artificial intelligence, need to be more efficient in a competitive global market, reshoring of factories from China to the United States,and continued demand for remote monitoring systems for socially-distanced work environments.
From what we have seen, the most successful engineers have taken time to study artificial intelligence and computer vision systems. Another important factor is that the most successful engineers have a deep understanding of their organizational structures so that they can drive truly transformational changes involving numerous stakeholders.
Question: How are you getting the word out and educating potential buyers about what you’re doing?
Kao: We are currently reaching out and educating potential buyers via a direct sales strategy and strategic partners. One of our key partners is the Next Generation Manufacturing Canada Supercluster, which has $230 million (CAD) to deploy in advanced manufacturing projects over the next three years. Next Generation Manufacturing Canada has invested in a consortium for digitizing steel production led by ArcelorMittal in which we are a member.
Question: What are your go-to-market strategies? (What mix of direct sales, distributors, system integrators, services, licensing?)
Kao: We are currently pursuing a direct sales strategy and are open to working with forward-thinking distributors.
Question: What is your website address and how can interested engineers get more information about your offerings?
Kao: Our website address is https://i-5o.ai. To get more detailed information, interested engineers can use the link https://i-5o.ai/success-stories and use the password manandmachine.
Question: What other things should our subscribers know that we didn’t cover?
Kao: The manufacturing industry currently looks at overall equipment effectiveness (OEE) as the key performance indicator for measuring shop floor productivity. The companies that we’re working with have found OEE metrics alone to be insufficient since machines at the end of the day still require human operators for material handling, changeovers, and maintenance. By focusing on OEE alone, manufacturers are leaving out the catalyst for action on the shop floor which is the human operator. That is why the most innovative companies in manufacturing these days are starting to look at the less popular metric overall labor effectiveness (OLE) for managing their operation. OLE calculations are now only possible because deep learning powered computer vision software can perform the time studies that used to be performed by human industrial engineers.