Using digitalization and open automation provides opportunities and challenges for original equipment manufacturers (OEM) offering faster technology iteration and redefining customer value.
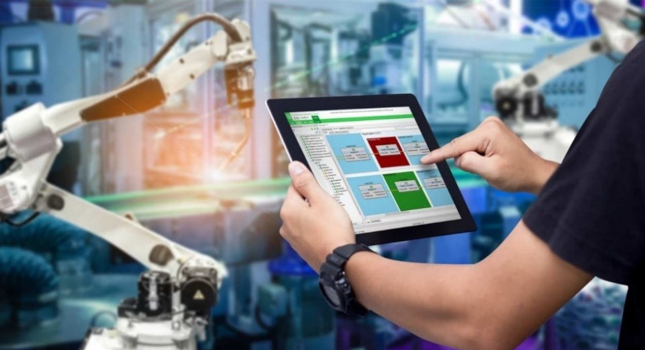
OEM digital transformation insights
- Manufacturing original equipment manufacturers can add value by providing service digitization for installation, repair, maintenance, remote service, spare parts and product improvement.
- OEMs can go to market more quickly with equipment and services by applying digital transformation, open standards and more intelligent controls, decoupling hardware and software and adding interoperability.
In today’s original equipment manufacturer (OEM) market, where industry growth is slowing down and profitability of stand-alone equipment is decreasing, technology iteration and value reconstruction are an inevitable requirement for OEMs. For a more competitive future, it’s key to understand how to:
- Use the current new digital technology to go beyond the low-end product competition of winning by volume
- Move to higher value-added mid-range and high-end products, service business, and even full production line and workshop integration business
- Create more value for customers through digitalization and use of open automation.
Manufacturing, OEM value reconstruction, service digitization
Creating a digital factory has been the inevitable choice of manufacturing enterprises to improve production efficiency, flexibility or reduce energy consumption and costs. A digital intelligent factory, smart manufacturing, helps achieve that. OEMs also have changed from supplying only equipment to providing digital product and service system operators, or even industry-wide service providers, participating in customers’ operations processes. Such a transformation has undoubtedly reconstructed the value of OEMs in the industrial supply chain, further enhancing value.
Today, customers demand more services and downtime from machine and equipment failure or maintenance has become more unbearable. OEMs need to increase customer lifecycle value by providing predictive maintenance and connected services. OEMs are digitizing their offerings and creating new business services.
Five areas of OEM digitalization: installation, repair, maintenance, remote service, spare parts, product improvement
The first step for OEM digitalization is to support equipment after-sales service management, including the five areas of installation, repair, maintenance, remote service, spare parts, and product improvement. Even where past OEM data flow has been important, enhanced two-way feedback ensures when devices or systems need maintenance or replacement parts. In the case of user permission, OEM manufacturers can understand the actual operation of the device in real time, can be more proactive in the corresponding management, and even service customers, which will bring the whole efficiency improvement.
Faster technology iteration, digital transformation
According to a Futurum Research survey, most business owners believe OEM partners are very important in helping them achieve their key business goals, and more than 88% of respondents said existing OEM partners help them overcome innovation barriers and accelerate time-to-market plans. Customers increasingly want OEM partners to help with digital transformation.
In this environment, OEMs need to consider repositioning products, services, internal processes and employees to meet customer needs in rapidly changing markets. Technology iteration will helps enable of this process.
OEM technology iteration is reflected in the digital transformation of the five segments of research and development (R&D), production, supply, sales and service. Enabling technologies include digital twin, open automation technology, flexible manufacturing technology and cloud services.
Digital twins empower OEM machine lifecycle value
Digital twins can be used across the full lifecycle of device, systems and equipment, from concept prototyping, design and manufacturing to sales and services. With digital twin software, OEMs can create digital models of physical devices and perform virtual design and device commissioning to improve and validate product prototypes, reduce risk and quality costs, and accelerate time-to-market before machines are manufactured. In the production stage, digital twins can save personnel time and material resources for on-site hardware and software debugging during production processes. Many procedures that needed to be completed on-site in the past can be done virtually and safely.
In the sales process, digital twins can transform the design concept into a persuasive and dynamic sales presentation solution, and present the final product to the customer in a visual way. In the later stages of equipment operations and services, using a digital twin can play an even greater role. Users can use digital twin for machine repair, maintenance and operator training. OEMs can use digital twins to improve services to users, improve and test software upgrades virtually, reduce machine downtime and extend delivery of value to customers.
Open automation, controls add efficiency, flexible machine development
The control system is the brain of OEM machines and equipment, which directly affects the equipment cost, performance, interconnection, maintainability and other important indicators. The industry has been seeking a more open automation control system to reduce development costs and improve performance and maintainability. More open automation helps, including initial replacement of dedicated controllers with a universal industrial PC (IPC), open communication networks such as fieldbus and industrial Ethernet and using the unified PLC programming system standard IEC 61131-3. These have changed machine automation control systems from dedicated and closed to different degrees of common, open and interoperable.
These technologies have failed to decouple software and hardware. Evolution of IEC 61499, the standard for distributed control systems enables plug-and-play, software reusability and hardware versatility of automation systems, creating fully open automation.
Shorten commissioning time by 30% with open automation
The Schneider Electric EcoStruxure open automation platform based on IEC 61499 has promoted the application of open automation technology in OEM machines and equipment. A refrigeration equipment company using such an open automation platform shortened commissioning time by 30%, improved system management while also locking access to OEM’s function block source code and encapsulate and reuse automation objects to enhance service capabilities while protecting existing assets.
Flexible conveying system makes mass customization production possible
Large-scale customized production has always been a problem in the manufacturing industry. The production mode of automated factories is often single-design, high-volume “rigid production,” while multi-option, small-scale, personalized products need “flexible production.” In recent years, flexible, stable and efficient conveying systems have been applied to the machine or production line.
While enabling “flexible production,” the flexible conveyor system offers OEM machine builders and users many benefits, significantly reducing equipment design and deployment time to operation, simplifying installation and commissioning processes. Flexible conveying also makes equipment more compact to ensure better integration into the production line, supporting fast production batch changeover. Integration of new magnetic drive technology and modular designs ensure easier part replacement, simplifying maintenance and optimizing overall efficiency.
Digital cloud platforms, from reactive maintenance to predictive maintenance
Predictive maintenance is one of the core values of OEMs in services. Although predictive maintenance was proposed more than a decade ago, practical applications have been slow. A key inhibitor has been a lack of economical and convenient technology implementation. Today, cloud-based digital service platforms are creating tremendous new opportunities for predictive machine maintenance.
Through cloud-based service platforms, OEMs can equip machines with advanced remote testing, monitoring and repair capabilities. With big data analysis and machine learning, OEMs can build machine predictive maintenance models that use remote data collection to automatically trigger maintenance tasks when equipment operation shows abnormal indicators. This allows OEMs to track the full lifecycle of equipment from purchase, use, maintenance to end-of-life, adding value to the equipment lifecycle and bringing economic value to customers.
For OEM machines, the key to applying a digital cloud service platform is convenience and security. Convenience refers to the simplicity and ease of installation and use, while the required data acquisition, transmission, processing, visualization, analysis and other functions should be complete, and can be achieved with low code and drag and drop. Cybersecurity means the data flowing to the outside of the machine should be secured. Cybersecurity also secures remote-control operation of the machine with sufficient encryption and security measures, key customers accepting machine to cloud connections.
Stone Shi is executive editor-in-chief, Control Engineering China. Edited by Mark T. Hoske, content manager, Control Engineering, CFE Media and Technology, [email protected].