If you’re stalled with Industrial Internet of Things (IIoT) implementations or haven’t begun, consider these eight expert tips.
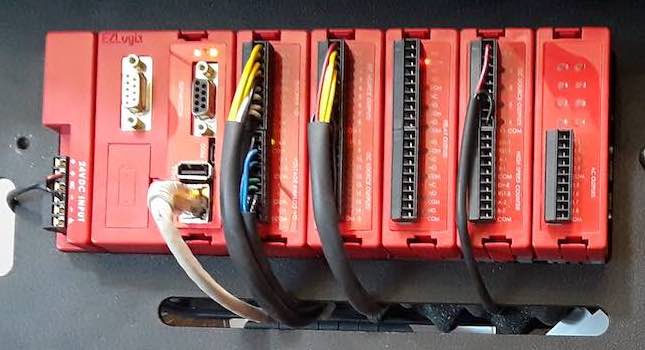
Most industrial businesses know they need to advance productivity with Industrial Internet of Things (IIoT), Industry 4.0, or Smart Factory initiatives. Choosing, migrating, updating, and integrating the required technologies often seem like an insurmountable obstacle.
If so, inertia about technology upgrades may enable competitors to gain an unfair advantage. Here are some tips from system integrators, end users, and automation vendors at the 2019 Inductive Automation Ignition Community Conference in September. Among IIoT enablers discussed was Ignition software, described as a universal industrial application platform for human-machine interface (HMI), supervisory control and data acquisition (SCADA), manufacturing execution systems (MES) and IIoT applications.
1. Don’t let the cost of updating automation or operations-related software kill a system integration or upgrade project. Steve Hechtman, founder, president, and CEO of Inductive Automation was a system integrator prior to founding the software company. He said he was laughed out of a prospective customer’s office after quoting a system integration/upgrade project because of the high price of the software required for the project. After working with developers to write his own software for automation projects, his system integration project “close rate was close to 100% after that point. Software should be easy, fun, and affordable,” Hechtman said.
2. Ensure those integrating, installing and using software have appropriate training and support. “Give those involved with a project a state-of-the-art toolbox they know how to use, and you’ll win,” said Don Pearson, Inductive Automation’s chief strategy officer. While his company offers paid training, experts there also spent more than 10,000 hours producing free videos online, where students can receive free education and certification. System integrators in the company’s program get free support. Developers can use the Ignition Exchange to share templates and projects.
3. Use an intelligent data hub to standardize industrial data structures and add context to the raw data, said John Harrington, co-founder and chief business officer, HighByte. Industrial data operations (DataOps) incorporates the operational activities needed prior to data being used by end applications, he said. DataOps software helps create intelligent industrial data, otherwise often unusable because of missing or unknow data tags, structures and context. “Industrial DataOps is focused on the challenges of working with industrial data or data from industrial automation and IoT devices,” Harrington explained.
4. Reconsider project functionality to move past traditional architecture definitions, suggested Vikram Kumar, president, EZAutomation and AVG Automation. For example, a major automaker had to call controllers “health monitoring stations” to move around traditional purchasing agreement bias, take advantage of IoT capabilities and continue interacting with traditional PLCs to improve productivity. Cybersecurity efforts and new industrial data communication methods also are helping process improvement initiatives with IIoT applications, Kumar said.
5. Get data where it needs to be when it’s needed to get the desired outcomes, said Benson Hougland, vice president, Opto 22. Using IIoT architectures can democratize data on the plant floor. Using message queuing telemetry transport (MQTT), edge devices and database connectivity enable operations to look at problems differently, cost effectively and in a way that can scale. Rip and replace isn’t always possible, Hougland acknowledged. Risk can be mitigated using I/O to cloud platforms with edge computing that supports familiar controls programming languages and enhances security. Doing so helps in the effort to get rid of programmable logic controllers (PLCs) and office computers on the plant floor in favor of DIN-railed mounted industrial edge devices capable of data processing and real-time control, and even secure existing programmable controllers (PLCs) where necessary. Secure VPN tunneling directly from the edge devices can reduce communications risk and enhances cybersecurity, he said, and IT can help.
6. Use best practice automation standard templates to enable IIoT implementations, suggested Dennis Brandl, chief consultant, BR&L Consulting. It’s faster to get from A to B by following a pattern. Updating and creating new assets can be more flexible and adaptive by using tools available in established standards, he said.
ISA 88 Batch Control Systems extends well beyond batch software and should be considered for any flexible, modular, object-oriented control software designs.
ISA 95 Enterprise/Control System Integration lowers the time and cost of integrating operations with the enterprise. It enables integration in weeks instead of months or years and improves the changes.
ISA 99 Security for Industrial Automation and Control Systems provides a framework for lowering cybersecurity risk to acceptable levels.
ISA 101 Human Interfaces for Process Automation Systems explains how to design high-performance HMIs.
7. Consider lifecycle costs when looking at hybrid operations technology (OT) and information technology (IT) technologies for the edge and an organization’s digital transformation, suggested Rick Cedrone, the head of Americas field marketing for Stratus. Using available, rugged edge computing resources creates setup and maintenance improvements and efficiencies. Virtualized architecture helps reduce costly IT involvement and makes it a strong platform for oil and gas and other challenging environments, Cedrone said.
8. Ensure communications are appropriate for the scale of the project. Device-to-device communications can bog down large IIoT systems. MQTT for industrial communications can provide an open-standard architecture and a cost-effective digital transformation and bridge the OT/IT gap, said Arlen Nipper, chief technology officer, Cirrus Link Solutions. Cirrus Link provides MQTT centric software for industrial automation and IIoT implementation, which expand use of sensors, data and analytics, on on-premise or off-site cloud applications. In 2018, using MQTT became less proprietary as Cirrus Link donated its MQTT Sparkplug B communications engine to Eclipse Software Foundation. It’s now an open, community-driven specification under the Tahu working group.
Mark T. Hoske is content manager, Control Engineering, CFE Media & Technology, [email protected].
KEYWORDS: Industrial Internet of Things, IIoT implementations
Overcoming IIoT obstacles can be easier by taking advice from experts.
Best practices provide structured, proven methods.
Lower-cost, easier implementations may help IIoT efforts.
CONSIDER THIS
If you’re stalled or don’t have an IIoT strategy underway, will watching competitors accelerate provide incentive?
ONLINE extra
Learn more about ISA 95 benefits and MQTT communications below. https://www.controleng.com/articles/optimize-manufacturing-value-in-real-time/
Learn more about MQTT communications. https://www.controleng.com/articles/mqtts-role-as-an-iot-message-transport/