See five attributes of the factory of the future. Information technology (IT) and operational technology (OT) organizations, hardware and software synergy should be part of the roadmap.
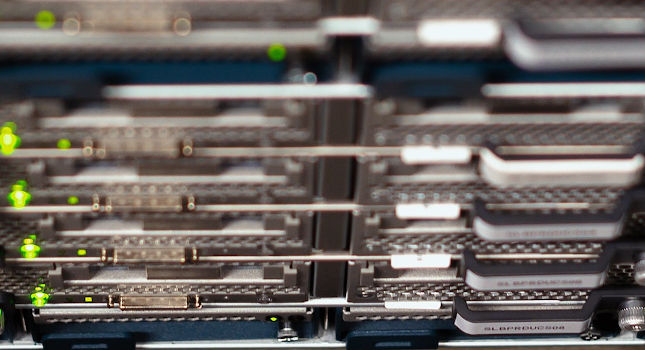
Automation remains a critical part of the designs for factories of the future. If you observe that industrial digital transformation has stalled or just hasn’t taken off, motivation and advice follow to apply intelligent automation, Industrial Internet of Things (IIoT) technologies and cybersecurity.
The global industrial automation market is projected to be worth $326.14 billion by 2027, growing at a compound annual growty rate (CAGR) of 8.9% in the forecast period, according to Fortune Business Insights June 22 report on Intrado GlobalNewswire. While this surge in the growth rate has been triggered by the COVID-19 pandemic, it is amply clear that factories will not be the same again.
In the next few years, enterprises may rely on machines to perform more than half of all tasks, which means the operating processes that govern them will become critical. This bodes well for the process industry, but there are lingering questions to address first.
Are businesses prepared for the factory of the future that is heavily reliant on artificial intelligence/machine learning (AI/ML), process automation, and Internet of Things (IoT)? How far along are they on their digital transformation journeys? What are the necessary process evolutions for future readiness? Most importantly, what are the key principles upon which to base future factories?
A good place to start is building a clear picture of the current scenario, the existing manufacturing processes and an enterprise’s near- and long-term business objectives.
Once the roadmap and strategy are clear, enterprises must work towards synergizing information technology (IT) and operational technology (OT) to optimize costs, reduce time to value and improve efficiencies.
Transition to factory of future in five areas
Five focus areas can help enterprise make the transition to the factory of the future:
- Intelligent automation
- Internet of Things (IoT)
- Data analytics
- Digital twin
- Cybersecurity.
Intelligent automation: Humans and robots empowering each other
Enterprises across industries, particularly in manufacturing, are heavily investing in automation. Since the dawn of Industry 4.0, business leaders have turned to emergent technologies such as AI/ML and robotic process automation (RPA) to build ecosystems that minimize human intervention. With intelligent automation, repetitive or predictable work can be performed faster while human resources focus on higher-order tasks such as monitoring, troubleshooting, and decision-making.
As AI/ML evolves, robots will become smarter and will soon “learn” from their tasks and responses. With the growing use of RPA on factory floors, robots can easily take over repetitive tasks in the assembly line with precision and speed. But such large-scale robot usage will require process evolution and intelligent, insightful decision-making. To make this happen, enterprises will need to upgrade infrastructure and ensure seamless process support and operational continuity.
Internet of Things: Using real-time operational intelligence
IoT devices equipped with smart sensors transmit and share data in real time through high-speed, secure, and reliable networks. Data analytics that emerge from such smart, connected systems yield key operational and business intelligence, all of which can be viewed on user-friendly dashboards. Enterprise leaders can then use these insights to drive decision-making and achieve growth objectives.
An IoT ecosystem gives enterprises end-to-end, round-the-clock visibility into operations. This ensures safety, transparency, optimal productivity and a smooth functioning of the supply chain. Moreover, high visibility allows human resources to preempt possible issues and take proactive, corrective measures. Process efficiency soars, which results in seamless operations, reduced costs, and improved productivity.
In manufacturing units that deal with hazardous materials, chemical plants for instance, employees and systems need to follow the strictest safety protocols; failure to do so could pose significant health risks. With the use of IoT, enterprises can strengthen operating processes and deliver optimal safety and business value. IoT-enabled devices and smart sensors can be programed to trigger alerts when operations reach certain pre-determined hazard levels. The operations team can preempt and prevent disasters, protecting lives and saving recovery costs.
Data analytics: Making informed decisions for process optimization
Data analytics is critical to process engineering evolution. With advanced analytics, enterprises can have real-time insights into processes, meaning operational intelligence is always accessible. Advanced analytics automatically analyze data, ensure proactive monitoring and predictions, and enable process simulation and optimization.
In a hyper-connected enterprise environment, data analytics is critical for decision-makers to factor in all possibilities and prepare for any eventualities. Through advanced analytics, enterprises can optimize processes by making informed and timely decisions. This also helps integrate operations and make the best use of engineering talent.
Digital twin: Creating the most effective process models
While the digital twin has disrupted the manufacturing industry in the last few years, its application has mostly revolved around product lifecycle optimization. In its evolved state, the digital twin today has a crucial role to play in process modeling. In the Industry 4.0 spectrum, digital twin capabilities are not limited to visualization and collaboration; they now can be used to understand manufacturing operations as a whole and create a manufacturing process digital twin.
This is valuable for the process industry as it redefines processes. In the food processing industry. For instance, digital twin technology can help enterprises remodel operating processes by initially replicating physical processes in a virtual scape and making necessary adjustments to see where greater value can be generated.
When combined with AI/ML, IoT, and augmented reality/virtual reality (AR/VR), the digital twin allows enterprises to create holograms that enable collaboration between physical and virtual models. A process digital twin enables people and machines to work in tandem independent of location. This radically improves process efficiency, reduces time to value, and accelerates digital transformation.
Predictive maintenance is another important area for digital twins. Digital twins increase plant reliability by proactively monitoring equipment, identifying issues, and offering vital insights to mitigate the problem areas before they can cause operational disruptions.
In the process industry, digital twins help manufacturers recognize possible irregularities in plant operations. Doing so enables preventive and predictive maintenance, which results in reduced maintenance costs and improved uptime and productivity.
Cybersecurity: Keeping data safe, confidential
Today and in the factory of the future, cybersecurity cannot be a secondary consideration. Smart manufacturing is inherently dependent on secure and reliable digital networks. Robust cybersecurity is a foundational element of industrial communications.
A cybersecurity breach in a smart factory can have devastating consequences that can, at best, stall production, and at worst, cause losses in intellectual property (IP) and brand reputation, requiring years of recovery. Breaches of confidential or sensitive data can result in serious ramifications for regulatory compliance. As governments, enforcement bodies, and regulatory institutions emphasize the need for watertight data security, failing to comply with those requirements may result in hefty fines and long-term penalties.
As technology evolves, so do the sophistication levels of cyberattacks. A strong cybersecurity foundation that is constantly monitored and upgraded can help companies mitigate cyber threats. Process evolution is paramount for cybersecurity.
By bringing in process developers with capabilities in cybersecurity modules, enterprises can benefit immensely from holistic process upgradation and integration.
Driving value by partnering with process experts
As enterprises progress on the digital transformation journey and work towards building factories of the future, the need for careful thought and planned processes grows. To get there, enterprises must find innovation partners who can offer the technological knowhow and engineering prowess across domains and processes. This is critical for the process industry, which tends to rely too much on technology solutions providers for digital transformation needs.
This creates a gap between technological implementation and process engineering. By forging a knowledge partnership with process specialists, enterprises can achieve composite IT and OT excellence. Specialists help make use of mature and nascent technologies and build secure, hyper-connected and automated factories that provide a competitive edge.
Vinay Bhanot is executive vice president (North America), L&T Technology Services. L&T Technology Services is a Control Engineering content partner. Edited by Mark T. Hoske, content manager, Control Engineering, CFE Media and Technology, [email protected].
KEYWORDS: Industry 4.0, digitalization, augmented reality
CONSIDER THIS
Are Industry 4.0 and Industrial Internet of Things automation technologies increasing operational effectiveness?