There are many currently available technologies that can help keep manufacturers productive right away as everyone adjusts to the new normal.
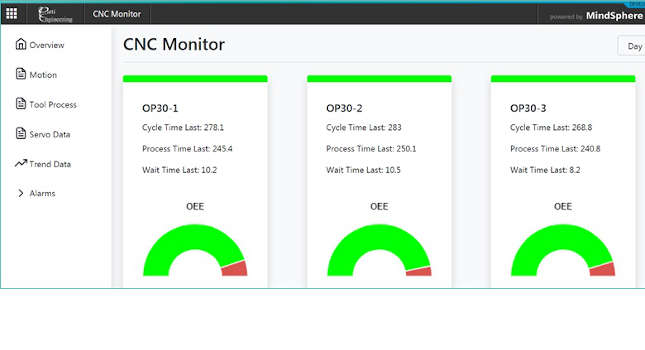
The most immediate need for workers returning to the plant floor in the wake of COVID-19 are social distancing and contact tracing. Many facilities that have been shut down are reopening at a cautious pace. In order to do that safely, the challenges workers and companies face are:
- Maintaining 6 feet of distance whenever possible
- Limiting the number of people on the plant floor
- Designing workplace contact tracing procedures.
By and large, these solutions already exist. And we’ve seen this play out in other industries. Work-from-home infrastructure was already in place before this pandemic just waiting for more companies to adopt it. Zoom is the most infamous, but messaging apps like Slack, cloud-based file storage systems, and virtual private network (VPN) providers have been around for years.
Those office-based departments and companies that have been investing in that technology over the years had little transitioning to mandated work-from-home policies. Those slower to adopt crashed their VPNs a few dozen times in the first couple of weeks. Restaurants that adopted online ordering and curbside takeout within days are largely still around, while many who decided to “wait it out” may never open their doors again.
Five technologies to help manufacturers adapt
As manufacturers look to what comes next, we can take these lessons from other businesses. The technology is already here; those that adopt and adapt will survive.
1. Real-time locating system (RTLS). A real-time locating system enables real-time tracking of objects that are attached to a tag. Pre-COVID, these applications were geared more toward asset tracking and equipment locating. For social distancing, these RTLS tags can be attached to a belt clip or a hardhat to track people. Alarms can be set if proximity dips below 6 feet. Most promising, the data can be collected and stored; in the event of contact tracing need, there is a record of who the person interacted with during their contagious period.
2. Simulation. Masking tape on the floor may not cut it on a production line the way it (sort of) does in the grocery stores. Side-by-side work stations may need to be separated and recipes may need to be adjusted to limit or eliminate tool sharing. Before moving several tons of equipment, simulation can help companies nail down a plan. Users can port in original stations and equipment, and watch how proposed changes will play out. This helps companies and users resolve inevitable hiccups in advance.
3. Virtual commissioning. Our customers have been loving virtual commissioning for its ability to reduce downtime during the installation process. Now, virtual commissioning can reduce the number of people needed onsite and their amount of time spent onsite during an installation process. Most of the testing and debugging can be completed remotely so that equipment is ready to startup quickly once the team assembles on the plant floor.
4. Remote monitoring. Another way to improve social distancing is to provide remote monitoring capabilities. Not only can this technology be used to view overall trends or to troubleshoot from home, it also can be used to create distance within the facility. For example, if a human-machine interface (HMI) does not need to be viewed from its location mounted to the equipment, it could be viewed “remotely” from behind plexiglass or in another room. Then, operators are close enough to resolve issues quickly, while not standing so close together.
5. Data analytics and condition monitoring. A proximity conundrum will arise when maintenance needs to be performed on equipment. Before, the maintenance team often worked side by side with the operators, quickly fixing issues as they arose during production. Now, do you take production offline so that the operators can clear out while the maintenance team swoops in? One way to prevent this dilemma is with data analytics and condition monitoring, which can predict maintenance needs.
All of these technologies are solutions that we implemented for our customers before these crazy times. Back then, they just solved different challenges. While we never could have predicted the challenges you face today, we’re ready to solve them because we are fluent in smart manufacturing.
– This article originally appeared on Patti Engineering’s website. Patti Engineering is a CFE Media content partner. Edited by Chris Vavra, web content manager, Control Engineering, CFE Media and Technology, [email protected].