With 2D, 3D, and even deep learning inspections all being realistic product inspection options today, it's can be hard to choose. Five tips for picking the right system are highlighted.
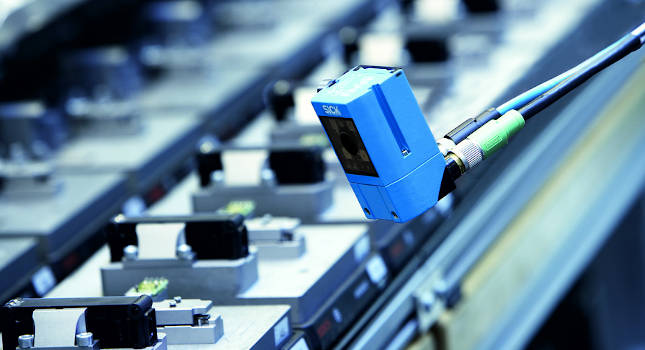
Not long ago, machine vision applications would only be attempted by the courageous few; those with no choice but to eliminate the risks of human error from repetitive, repeatable quality checks. Today, many 2D and 3D systems are plug-and-play solutions. Configuring a bespoke system is straightforward, even for someone without specialist programming skills. The following tips might help potential users to make the most of what is on offer.
1. Ignore the hardware: The latest CMOS sensors and on-camera chip calculation power is impressive. Easy-to-use quality inspection sensor Apps can run directly onboard small devices with impressive resolutions, higher processing speeds and a wide array of image processing tools. Despite this, even if you are tempted to upgrade to the latest model, it’s good to go back to the drawing board to consider the process from first principles.
2. Ask simple questions: It is important to understand exactly what you are trying to inspect – and why. Where are the pain points? Where is the waste?Deceptively simple questions, but whether you are checking that a mould is empty, a biscuit is baked correctly, or that a flow wrapper has sealed a meat pack, go back and audit the effectiveness of your quality processes and you may be surprised by what you uncover.
3. Be an early bird: The fundamental challenge of specifying any vision system has always been finding the best way to discern the differences between a product or pack that is good or bad. The earlier you spot the bad, the less value you will have added to it. If a user is inspecting a printed label, do so immediately after the printer; if you are checking the right number of baked goods in a tray, then inspect right after they have been placed. Then consider, what corrective action might be needed. Is a warning sufficient, do you want the line to stop, or to divert a rejected product?
4. Consider the “eyes on:” Advances in “smart” sensors and connectivity have enabled operators to visualize what is happening with their inspections in real time. Whether you are in the control room, working from home, or walking around site with a smart phone, you can ‘see’ inside each sensor on a machine via a simple dashboard, check its operation, and monitor the inspection results. Consider the ability of the vision system to display all the data you need, when you need it.
5. It always comes back to profit: Vision inspections are no longer about the art of the programmer, but the art of the possible. Users also can expect the highest machine availability even in the high-speed environments of the food industry, with multiple batch changes, or where ambient light, dust or moisture is challenging. So do keep looking for opportunities to automate. Even complex inspections, such as robot-picking naturally grown produce, can now be configured in a matter of hours using all-in-one deep learning vision sensors.
Specifying a vision system has always been ultimately revolved around the return on investment (ROI) whether its replacing human checkers with a machine or upgrading to a more advanced system. Every investment needs to be balanced against the cost of releasing an imperfect product into the next process or shipping it out of the door.
This article originally appeared on Control Engineering Europe’s website. Edited by Chris Vavra, web content manager, Control Engineering, CFE Media, [email protected].