The Industrial Internet of Things (IIoT) is changing how food and beverage manufacturers approach safety, product quality, packaging, and how personnel work in their day-to-day operations.
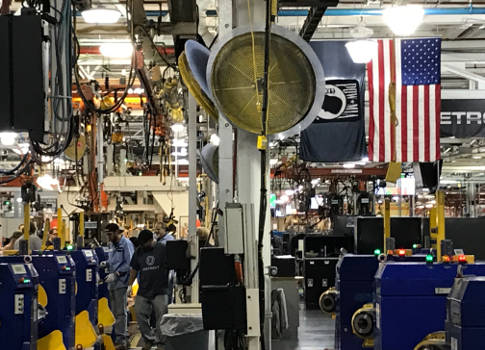
The Industrial Internet of Things (IIoT) is revolutionizing the food and beverage industry. We’re seeing more connected sensors, motors and controllers on the plant floor than ever before. This technology is being used in innovative new ways to optimize processing and inform operational decisions. There are four main areas of a food plant, in particular, where IIoT technology is having a major impact:
1. Food safety
Preventing recalls is crucial for the health of the consumer, the company’s reputation, and the bottom line. Today’s IIoT technology can stop food recalls by preventing bad product from even leaving the facility in the first place. This can be done if the system is set up correctly with the right sensors and data collection points.
Consider a facility producing sauce that needs to be heated to 192°F for five minutes to ensure all hazard analysis and critical control points (HACCP) and regulatory requirements are met. In the past, users may not realize they have a bad batch until it is packaged because of how long it would take for a manual report to be delivered to the quality control department.
However, internet-connected sensors can measure those time and temperature set points in real time and immediately send a notification if they are not met. This helps save time and money while reducing the risk of the product leaving the facility. Thanks to real-time IIoT technology, potential food safety issues can be detected quickly and dealt with internally before getting to the point of a recall.
2. Product quality
A well-connected plant also benefits production by improving consistency and accuracy in product quality. Today, product recipes and procedures can be stored on a single server and pushed to all of a company’s processing facilities. This helps ensure product consistency regardless of where the product is produced.
Companies can also send quality benchmarks and metrics, such as cook time and temperature, to internet-connected equipment. The machine knows, based on its programmed instructions, to run a certain recipe at a certain time by adding certain ingredients and process them in a certain way.
A plant utilizing IIoT technology can be remotely monitored and controlled. This helps improve recipe accuracy and product consistency.
3. Packaging
When it comes to packaging, changeovers and downtime are the biggest factors today. The goal, as always, is to maximize revenue by running the most amount of product with the least amount of assets as quickly as possible. A well-connected plant can help achieve this goal by making packaging more efficient.
Sensors on packaging equipment can be programmed to understand what SKUs to expect from the processing side at a given time. The sensors can verify the correct packaging is being used for various products and immediately halt the process if there is a discrepancy. Traditionally, if an operator ran the wrong product in the wrong packaging film, it may not be detected until much later, resulting in wasted product and packaging that has to be thrown away. Today, these discrepancies can be virtually eliminated by catching packaging mistakes in real time.
In an IIoT-based plant, labeling parameters are downloaded from a server as well. Instead of an operator manually typing in the information, it can be sent to internet-connected equipment. This reduces potential operator error on the plant floor. It also allows operators to focus on verifying if the computer is correctly running the labeling.
4. Personnel
IIoT technology is making plant personnel more connected to their work rather than squeezing them out. Thanks to the unprecedented access to data provided by sensors and software, employees understand their facility’s processing more than ever before.
Today’s facilities can “talk back” to employees and notify them when something is wrong. This enables plant personnel to do their jobs better. However, employees are still needed to change film, perform certain processing aspects, and conduct maintenance. IIoT technology helps make communication between plant personnel and equipment a two-way street.
The future of internet-connected food plants
IIoT technology has empowered food processing facilities with unprecedented access to real-time data. However, many food manufacturers are still learning about these capabilities and what they can do with all of this new data. Many customers are still learning what is possible and how they can harness this data to meet their goals.
The adoption of IIoT technology is starting, but there is still a long way to go before it is ubiquitous. There is a lot of potential for how this technology will impact the food manufacturing industry, but widespread adoption will take time.
Rao Kolla, senior controls engineer, Stellar. This article originally appeared on the Stellar Food for Thought blog. Stellar is a CFE Media content partner.