Leverage Industry 4.0 to build the foundation for an industrial architecture that integrates operations to drive data from field to edge to cloud to create a boundless automation future.
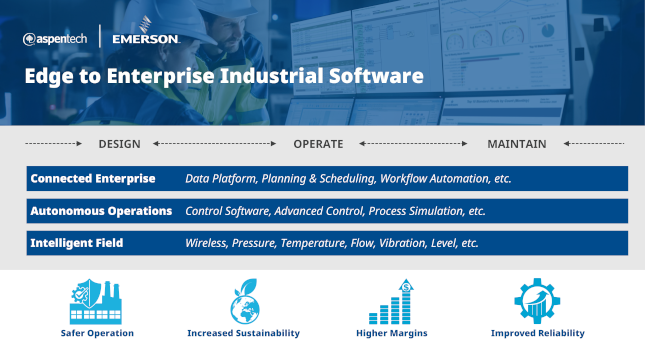
Learning Objectives
- Learn how breaking down data siloes can lead to system- and enterprise-wide efficiencies.
- Learn about advances in technology that will enable real-time, enterprise-wide connectivity.
Industry 4.0 insights
- Manufacturers are discovering the traditional architecture of keeping operational technology (OT) isolated from the internet is no longer viable.
- Improving operations at the enterprise level by leveraging the software and technology available to optimize operations and interaction among multiple plants and process lines.
- Technologies and protocols such as Ethernet advanced physical layer (Ethernet-APL), 5G communication, OP UA, hyperconverged infrastructure and containerization are key components of creating a boundless automation future.
Safety, reliability and increased production are still critical drivers for industrial process manufacturers. However, shifting corporate goals and public opinion has created an increased focus on sustainability and improved energy, adding yet one more constraint to optimization. Finding the best operating limits to maximize all these requirements necessitates more cross-domain information than ever.
Manufacturers are discovering the traditional architecture of keeping operational technology isolated from the internet is no longer a viable path to best-in-class operational excellence. However, the cybersecurity advancements emerging alongside Industry 4.0 include enhancements providing users the best of both worlds: increased connectivity without the risk of harming systems.
Even so, accomplishing these goals requires integrating multiple operational domains to move data seamlessly from the field to the edge and into the cloud across all data silos — creating a boundless automation architecture. At the heart of this automation vision are natively-integrated operations and applications operating within a unified data model and secure connectivity between next-generation automation technologies regardless of where the data resides or applications reside.
Forward-thinking automation suppliers will integrate technology and software across every domain in the coming years. They will break down silos, democratize data and bring reliability, sustainability, energy use, quality and other critical operational data together with real-time control to create an interoperable, extensible and scalable unified data model. This paradigm shift in automation will empower operations teams across all domains to increase performance while meeting the organization’s and public’s needs and goals (Figure 1).
From edge to enterprise
The need to optimize operations is not new, but today’s global marketplace has increased competition and tightened budgets. As a result, few organizations today seek to increase production by building new plants. Instead, operations teams are focused on optimizing — or more likely revamping — existing assets to increase flexibility, scalability, throughput and efficiency. However, most teams have been optimizing their plants for years and have reached the point where localized action brings diminishing returns. The next step is improving operations at the enterprise level by leveraging the software and technology available to optimize operations and interaction among multiple plants and process lines.
For example, based on years of instrumenting facilities with affordable sensing technologies, the amount of visibility into real-time operations is the greatest it has ever been. Operations teams can monitor almost every piece of equipment across the enterprise for fleet-level visibility of performance and reliability.
The data from that equipment — if it is free to move across all layers of the enterprise — can be sent to remote domain experts or even to artificial intelligence and machine learning tools for deep analysis. The results provide a clear picture of process health. They can also deliver actionable information to help organizations improve scheduling, reliability and performance across all plants while reducing energy use and waste.
Other teams also are using simulation software and digital twin technologies to replicate processes, or even entire facilities, to test process changes, train personnel and optimize operations. Operators working on a digital twin also can make changes to the process as though they were working on live equipment, with no risk to operations. As the simulation runs, they can see — in real-time or even faster — how the changes they made cascade across all areas of operation. Operators can see not only how a change will impact their plant or process but also plants and processes that depend on their output.
These tools, and many advanced tools that have yet to emerge in the marketplace, depend on a reliable flow of contextualized data, across domain silos and beyond typical data boundaries. The organizations that win the future of manufacturing will not install a siloed and targeted application to solve a specific problem. Instead, they will be those that can deliver the right data to the right place at the right time to maintain flexible, scalable operations leveraging all the data they already have (Figure 2).
Unlocking the future of automation
The architecture that best prepares an organization to meet the future of process manufacturing is based on a boundless automation vision. A boundless automation architecture integrates industrial software, Industry 4.0 technologies and a next-generation automation fabric to democratize data across every operational domain.
Comprehensive architecture
Today’s high-performing operations teams expect and rely on instant access and constant visibility to critical information. By providing the correct access to information by the right people, organizations foster the innovation that leads to constant improvement and, with the right technologies and collaboration, toward self-optimized facilities.
Providing this access means changing the traditional operation paradigm to decentralize models and eliminate data silos, enabling contextualized data to stream across the enterprise.
This model of constant, intuitive, standardized access to data looks much like current, highly integrated business solutions, like enterprise resource planning software.
All operational domains — intelligent field devices, the next-generation control system, edge solutions, cloud technologies, and more — will be integrated into a cohesive software ecosystem.
This system will standardize data into a unified data structure, connected to context provided by all the other sources, and made available across the enterprise to cross-functional teams through many tools in natively-integrated industrial software platforms.
Advanced technology fabric
A new, more modern technology fabric will provide the critical technologies operations teams will rely upon, such as analytics, simulation, energy management tools, field-based insight applications and more. Technologies and protocols such as Ethernet advanced physical layer (Ethernet-APL), 5G communication, OPC UA, hyper converged infrastructure and containerization are forming the foundational technology infrastructure that will simplify connectivity among systems and smooth data flow.
Instead of building solutions as an edge layer on top of automation, new technologies will deliver an integrated ecosystem with fit-for-purpose apps, delivering a more intuitive experience between operational and information technology. This will be the case whether content originates from the cloud, a field device or an on-premises hyper-converged infrastructure.
Tensioned domains across the enterprise
Many plants have been around for decades and have reached the point where optimizing operations domain by domain is no longer effective. Most of the easy fixes and optimization strategies have been found and implemented, and each domain works well in its own silo, but those same silos impede progress.
If a team needs to know the source of wasted energy, but a critical part of the cause is found in reliability data trapped in a siloed system, a key insight may need to be made public. Boundless automation architecture solves this problem by focusing on a broader strategy and tensioning those domains against each other to deliver continuous, enterprise-wide optimization.
Within the boundless automation’s integrated ecosystem, data is contextualized, democratized and centralized so it is instantly and securely available to appropriate personnel at any level of the organization. The future industrial edge will be built on hyper-converged infrastructure and universal fleet deployment and support.
Many applications that are not operations-critical can move to the cloud and enjoy the same benefits as IT systems and technologies: outsourced infrastructure, no software installed on client devices, universal access, elastic scalability, pay-as-you use consumption models and more. These systems will integrate with enterprise cloud systems such as enterprise resource planning (ERP), artificial intelligence and machine learning (AI/ML) analytics, simulation systems and more.
A boundless automation future with Industry 4.0 technologies
Only some technologies that will drive the boundless automation architecture are available today, but many are here or on the horizon. However, the wide range of Industry 4.0 tools available today are helping teams build the foundation they will need to take advantage of next-generation automation solutions coming in the next five to 10 years. Today’s optimization decisions should be made with that future in mind, looking toward building the flexibility, standardization and visibility necessary to improve performance and efficiency across the enterprise.
Nathan Pettus, president, process systems and solutions, Emerson. Edited by David Miller, content manager, Control Engineering, CFE Media and Technology, [email protected].
MORE ANSWERS
Keywords: Industry 4.0, Enterprise Connectivity
CONSIDER THIS
What efficiencies can you achieve by focusing on system-wide optimizations?