Digital twins can help model-based technologies provide a basis for continuous process optimization and efficient plant operation.
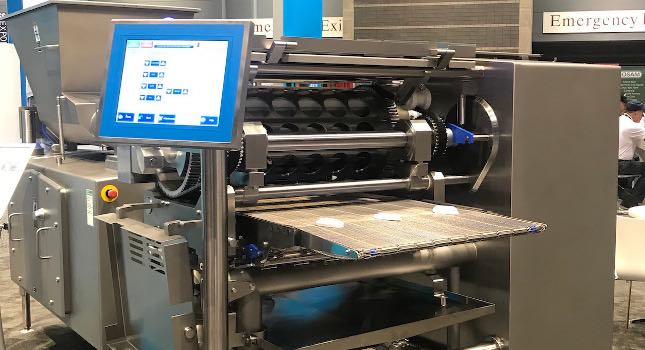
Learning Objectives
- Digital twins can help plant managers see the future of their plant with absolute certainty.
- All knowledge flows into a process flow diagram (PFD), the basis of the digital process twin.
- Digital twin simulation benefits increase if they are interlinked or transferred within each other.
Imagine being able to see the future with absolute certainty while operating your plant. The key to achieving this lies in simulations that are very close to reality. In a model such as a digital twin, the reality – in this instance comprising all the plant components and their characteristics and functionalities – is described using mathematical equations.
The digital twin can map not only reality, but also “what-if” scenarios to provide reliable predictions of a plant’s future behavior. It can do this because the model is bound by neither the technical limits of a device nor safety restrictions and the work of process optimization can therefore be completed in a safe, virtual environment.
Because the simulations have no time limits, even accurate predictions of the plant behavior are no longer a pipe dream. In an ideal scenario, three “independent” digital twins collaborate on a single process plant: The digital twin of the product, the virtual image of the production plant, and the digital modeling of product and production performance. To understand the concept of a “digital twin” it is important to remember the depth of detail – the accuracy of the twin – is dependent on the intended purpose. Depending on the specific job, for example, production simulation, optimization of the production process, or solving economic problems, models of greater or lesser accuracy are required and useful.
A new manufacturing approach
New perspectives are emerging from the approach of integrating the individual models and software tools into a consistent, semantically linked system over the entire life cycle of a plant. A great deal of in-depth process engineering expertise, combined with many software systems, is required to produce these types of systems and models. It is therefore possible to use existing system knowledge and the latest published information to produce an initial digital process twin using simulation software. This is used to design the plant and its components – the so-called “conceptual design.”
In this phase, all knowledge flows into a process flow diagram (PFD), the basis of the digital process twin. In the next engineering phase, the digital process twin is transferred to the system planning tool to form the basis of the digital plant twin. This is sequentially extended by further system-specific elements. The basic structure of the digital plant twin can then be created using plant engineering tools.
Once the process engineering is complete, all the required information is transferred to the engineering system in a process control system. In addition to this, the field level is mapped in a simulation platform so the automation software can then be virtually commissioned. Virtual commissioning has many benefits – on the one hand, all the automation functions can be tested in advance while the simulation can also be used to prepare and train plant operators, particularly for critical scenarios which can be played out in the virtual environment without any risk to the actual plant. Training is therefore provided for both standard operation and plant behavior in the event of disruption.
More than reality
Soft sensors are an important application of a digital twin in the operating phase. They estimate process variables which are not available using a process model to optimize process control as required. This model is ideally the existing digital twin of the plant. Previous experience has shown model-based technologies are the key for simulations, process optimization and accurate forecasting.
Consistent use of the three digital twins of product, production and performance mentioned earlier maximizes the economic benefits over the entire lifecycle of a process plant. These benefits can be increased if the simulation models are interlinked or transferred within each other.
Eckard Eberle is CEO of Siemens Process Automation. This article originally appeared on Control Engineering Europe’s website. Edited by Chris Vavra, web content manager, Control Engineering, CFE Media and Technology, [email protected].
MORE INNOVATIONS
Keywords: process simulation, digital twin
CONSIDER THIS
What benefits could your process facility gain from digital twins and simulations?