Siemens machine tool announcements at IMTS aim to simplify operations, increase productivity, manage machine tool resources, advance related ecosystems and digital thread, with collaboration to integrate additive and subtractive CNC machining technologies.
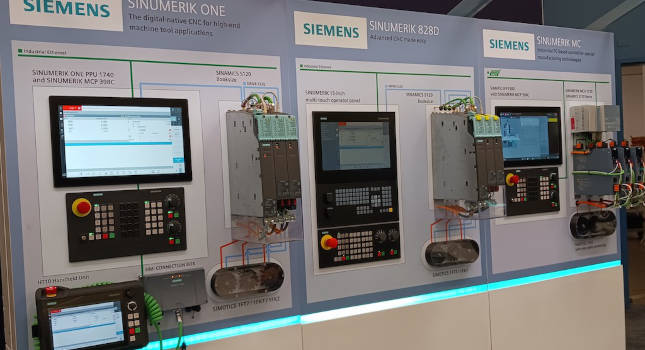
Advances in machine tool hardware, software, subtractive and additive manufacturing processes and related system integration were among four major Siemens IMTS announcements.
- New technology functions for the Siemens Sinumerik One computer numerical control (CNC) simplify operation and increase productivity. The Y-turning and Advanced Rapid Movement functions provide greater machine tool productivity and up to 10% faster machining. Reduced Dynamic Mode reduces wear and increases availability. End-to-end keyboard and machine control panels are available in 15 inches to 24 inches sizes.
- Siemens D Mcenter is a centralized, open-interface, on-premises platform to enable those with CNC machine tools to achieve optimum efficiency in managing manufacturing resources on the shopfloor.
- Siemens Xcelerator accelerates the digital transformation of the machine tool industry with a portfolio of IoT-enabled hardware, software and digital offerings for the machine tool industry. Software applications for cloud, edge and customer servers help machine tool business. The first partner applications are based on industrial edge for machine tools, an open ecosystem for IoT.
- Siemens, DMG Mori USA, Walter and Trak Machine Tools collaborate on next-generation part-manufacturing digital thread, involving software, machine tool building, tooling hardware and machine tool CNC automation. The new project demonstrates the power of the Siemens Xcelerator business platform. It includes a partner ecosystem in designing and manufacturing next-generation electric vehicle (EV) components using additive and traditional CNC manufacturing.
Sinumerik One upgrades, advancements
Siemens expanded its Sinumerik One “digital native” CNC. The new system software Sinumerik V6.20 has new technology functions for Sinumerik One that simplify machine tool operation, reduce machine wear and increase manufacturing productivity. The changes demonstrate how the Sinumerik One control system can be used for digital transformation in a highly productive, flexible and modular way.
With the new Y-turning function enables up to 3-times the feed rate, resulting in increased productivity. New tool types were created for this purpose, and all turning functionalities and cycles were adapted for these tools.
The Advanced Rapid Movement function enables time-optimized movement, which means faster movements take place between machining operations. The part program does not require a change. Overall, machining can be up to 10% faster. The function can be implemented in tandem with the machine builder.
The reduced dynamic mode reduces wear on the machine and increases its availability. The numerical control kernel (NCK) function enables the machine tool builder to automatically transfer the machine to reduced operation, if the axis becomes too warm. When the temp stabilizes, the machine can be returned to full load. It enables individual operation of machines in motion.
New hardware changes for Sinumerik One are designed to simplify operation. The new keyboards and Machine Control Panels (MCPs) are available from 15 inches to 24 inches to match the human-machine interface (HMI) design — and Simatic Industrial Thin Clients (ITCs) and industrial PCs increase performance and provide resolution up to 1920×1080 pixels.
The MCPs are integrated in the digital twin of Sinumerik One (Create and Run MyVirtual Machine), so the appearance and operation correspond to the real CNC. Sinumerik One digital twin features simplify engineering and work preparation. The 3D option offers support for a second channel. Each tool can be assigned an individual color, so ablated surfaces are color-coded, depending on the tool used. The integration of the STEP format is an important new feature, especially for complex geometries of the clamping in a turning operation. Collision detection displays all collided bodies, shows an NC program line and other features, so the cause of collisions can be quickly investigated and rectified.
Mcenter manufacturing and resource management platform
The Siemens Mcenter, a new manufacturing and resource management platform, is designed to enhance the preparation of tool scheduling, workflow supervision and NC program management. It networks machine tools with the company’s information technology/operational technology (IT/OT) landscape.
Vivek Furtado, head of Siemens machine tool digitalization, said, “Mcenter breaks into a new horizon of overall machine monitoring, comprehensive manufacturing management and resource utilization to produce the ideal workflow and production scenario for any manufacturer with CNC machines.”
Part manufacturing companies across several industrial sectors face ongoing and increasing pressures to make production more cost-efficient, more flexible and more sustainable. Companies of all sizes wrestle with the issues of digitalization and improved asset management, the challenges of preparing production orders, materials and tooling acquisitions. Devising the best use of machines on the floor for optimum workflow and output can be daunting.
Machine tools traditionally communicate with the central server of a machine shop or factory network via clients that are directly integrated into the control. Web applications are used that can be accessed via a PC or tablet web browser. In contrast, user dialogs embedded in the CNC’s HMI are provided for tasks performed directly at the machine. Connection to existing IT systems in the production environment can usually be established via application programming interfaces (APIs). Mcenter balances these conditions to achieve the desired outcomes and reduces IT administration complexity through centralized platform functionalities such as connectivity, security roles, rights, application management, and other functions. This is the backbone of the Siemens Smart Shopfloor protocol.
Siemens Mcenter has:
Tool management: The application Manage MyResources/Tools provides full transparency about available tools and locations. This feature enhances productivity by minimizing the time needed to pair the right tool with the right machine at the right time.
Program management: Manage MyResources/Programs provides an immediate overview of all available NC programs and status for easier programming and setup.
Overall equipment effectiveness (OEE): Analyze MyPerformance/OEE allows the important indicators to be identified for the improvement of machine or work cell utilization to eliminate production bottlenecks.
Mcenter can:
Encompass all machine tools — With Mcenter, it is possible to manage all types of machines, regardless of their age or controller brand, across the shopfloor. Deeper onboard integration with Sinumerik CNC machines provides additional value. Siemens continues to improve CNC integration with other CNC brands.
Increase overall productivity with minimal effort — Mcenter enables companies of all sizes to increase productivity by providing the user detailed insights on tooling, NC programs and machine utilization. Enhanced integration of higher-level systems with the CNC on the machines makes it possible to manage workflow on the shopfloor with reduced effort. This feature significantly lowers set-up times, the chief impediment to productivity. It optimizes resource utilization, thereby lowering overall cost to the manufacturer.
Integrate with existing IT infrastructure — Mcenter provides open interfaces that allow flexible integration into existing IT infrastructure and processes such as connecting to pre-setters for automated data transfer. It offers additional opportunities for the manufacturer to use the Siemens Teamcenter digitalization portfolio.
Siemens Xcelerator optimizes machine tools
Potential for optimizing machine tools is improved with continuous analysis of production data. With the open digital business platform Siemens Xcelerator, IoT-enabled hardware and software, the physical world can be connected to the digital world to accelerate digital transformation and enable flexible and sustainable action in the building and use of machine tools.
The Siemens open, digital business platform, Xcelerator, enables customers of all sizes in industry, buildings, power generation, public utilities and mobility to accelerate digital transformation and increase value creation. The business platform makes digital transformation easier, faster and scalable. It has a curated portfolio of internet of things (IoT) enabled hardware, software and digital services from Siemens and certified third-parties; a growing ecosystem of partners; and an evolving marketplace to facilitate interactions and transactions between customers, partners, and developers.
Siemens applications include Manage MyResources/Tools, Manage MyResources/Programs, Analyze MyPerformance/OEE, Manage MyMachines, Manage MyMachines /Remote and Analyze MyMachine/Condition, and the Industrial Edge for Machine Tools platform.
The apps provide intelligent resource management that allows production orders to be prepared by providing the right tools and NC programs. A central solution at the manufacturing level manages real instances of tools, tool locations and programs for parts production, using the data from the CNC. Workflows in machining environments are optimized, tool circulation and tool inventory are efficiently organized.
Utilization of production capacities can be improved by analyzing overall equipment effectiveness (OEE). Applications increase connectivity even for CNC machines not equipped with Siemens Sinumerik CNC, a significant development. Manage MyResources/Tools can provide other tool use information, such as the duration of the different life phases for certain tool types.
Tool planning can improve with reservation of tools for a machine or production order or as a standard tool. With the help of unloading lists for balancing, the planning of tool requirements will increase efficiency.
Manage MyResources/Programs adds file types such as drawings to NC packages. In Analyze MyPerformance/OEE, machine status can be configured individually. The app provides detailed insights into workpiece statistics and production progress.
In the new version of Manage MyMachines, it is possible to examine reports of technical faults even more closely. Seamless transition between the two apps Manage MyMachines and Manage MyMachines/Remote improves the user-friendliness and efficiency of service calls. Manage MyMachines has broader connectivity, supporting machine controllers from other manufacturers.
Siemens openness to partners is demonstrated by the Industrial Edge for Machine Tools ecosystem. Based upon the Siemens Edge Platform, Schunk, the global manufacturer of gripping systems and clamping technology, developed its iTendo Service. By combining sensor data from the tool tip and data from the NC, Schunk wants to help machine tool operators improve the machining process and prevent tool breakage.
Siemens, DMG Mori, Walter and Trak Machine Tools
Greater collaboration on next-generation part manufacturing digital thread results from Siemens, DMG Mori, Walter and Trak Machine Tools work together. Potential for integrating optimization as a fundamental part of the design and engineering workflow, when considered alongside the power of additive combined with traditional manufacturing, is enormous. Converging projects prove out, validate, and embrace reduction of waste and maximization of resource utilization during design, and in reduction of mass and energy consumption during use.
The new digital thread leverages technologies from all four companies beginning with Siemens NX software to generate the initial design, taking operating parameters of an electric vehicle and using them to drive the development of an optimal part design for a critical suspension component with integrated generative engineering tools like design space exploration. During the design for additive manufacturing phase, the part concept is validated using structural simulation technologies and optimization is performed to ensure performance requirements are met and to optimize the manufacturing processes to produce it. Simulation-driven design ensured the optimal part is created with a minimal amount of material, resulting in an innovative steering knuckle design that reduces weight by 45% and improves performance so it can better handle stresses.
The next phase, Process Planning, demonstrates how comprehensive manufacturing plans are developed with Siemens Teamcenter software and Opcenter software. This helps manufacturers automate programming by applying their own standard CNC programming, inspection path methods, tools and program templates, and ensures that correct revisions of parts are programmed and measured on the shop floor, creating one source of data for the digital manufacturing process.
The manufacturing phases show how the Siemens eRod component is manufactured using a combination of additive and traditional manufacturing methods then finished to achieve the necessary dimensional accuracy and tolerances while reducing the programming time by 60% with automation of routine tasks.
Advanced capabilities in NX CAM such as 5-axis simultaneous programming, cloud-based post-processing, and integrated simulation help prepare the part for both additive manufacturing using Ti6Al4V powder on a DMG Mori Lasertec 30 Dual SLM Selective Laser Melting machine, and finishing using a DMU 85 monoBlock 5-axis machining center by DMG Mori equipped with the Sinumerik 840D sl CNC system for a two-step machining process. The tools for next-generation, hybrid process chains aim to improve cycle times, reduce waste, and allow customers to re-imagine part design.
Walter tooling hardware will be used for the finishing and cut-off operations to ensure the required tolerances are met. This helps address new machining challenges such as the light-weighted component featured in this digital manufacturing demonstration. Machining of additive manufactured titanium presents challenges beyond the usual ones encountered in machining titanium components. The advantages of additive for generating complex components are clear, but the finish machining of those components is often not as straightforward as might be expected. Challenges addressed include removing support structures in 3D printed Ti6Al4V stock material that tend to be more brittle than the bulk material, difficult to access features, and minimizing vibration during machining where clamping for the component is weak due to the complex geometry.
A highly efficient machining process uses a combination of tools to address all challenges and provide a finished component that meets dimensional accuracy and surface finish requirements.
When evaluating the assembly, the design team determined that certain components could still be manufactured more efficiently with traditional subtractive processes. The spindle, designed in NX, lends itself to a traditional turning process. By using Run MyVirtual Machine, the digital twin of the CNC control, it was possible to add a Trak Machine Tools TC820si turning center in the digital manufacturing process. The spindle was virtually programmed in the Sinumerik ONE control using ShopTurn conversational programming and validated with the TC820si’s 3D twin.
To close the loop, Quality Control and Production Preparation will be carried out using automated CMM processes driven by dimension and tolerance data captured and stored using PMI (Product Manufacturing Information) and leveraged within NX CMM Inspection Programming software to ensure the part is within the tolerances expected and ready for assembly. During final assembly, the more traditional spindle component is married to the newly optimized knuckle and installed on the Siemens eRod.
– Edited by Mark T. Hoske, content manager, Control Engineering, CFE Media, [email protected].
KEYWORDS: Machine tools, computer numerical control (CNC)
LEARNING OBJECTIVES
Computer numerical control (CNC) technology functions are designed to simplify operation and increase productivity.
An efficient machining process uses a combination of tools to address all challenges and provide a finished component that meets dimensional accuracy and surface finish requirements.
CONSIDER THIS
How are you integrating advanced machining processes?