Networked safety: Unify your design. You can do without a separate safety architecture. Industrial safety networks lower risk as needed, while simplifying automation for the plant floor or within a machine. Don’t forget security, which can impact safety.
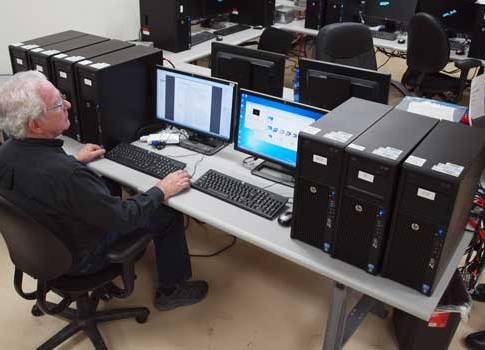
Learn everything you wanted to know about safety networks and their functions but were afraid to ask. Machine safety network checklist provided includes one often overlooked point. Machine safety networking can be simplified by combining safety and standard industrial networking into one solution.
The end of Microsoft Windows XP support raises concerns about industrial networks, connections to PC-based assets, and software patching. Assess software patching risks with 11 critical questions. In manufacturing plant floor applications, security and safety are an integrated concern. Control system cyber security is not the same as desktop PC security. Link to each of the longer online articles below.
Check out this network security checklist to lower risk while simplifying automation design. Very few safety networks existed 10-plus years ago; what existed were covered by little understood safety standards, and most networks were proprietary. In 2014, all kinds of new safety network capabilities and ideas are certified, standardized, and available off the shelf.
Today, there are DeviceNet Safety (CIP Safety), Profisafe, AS-Interface Safety at Work (ASi-SaW), EtherCat FSoE, and Powerlink openSafety, just to name a few machine safety networks. How do you choose a network? Many features and benefits make selection a daunting task without significant familiarity with machine safety, let alone safety networks.
Simplify industrial networks and machine safety
I can appreciate a really well-designed safety system, one that has all the emergency stop buttons positioned in locations easy enough for anyone to press, or the guard locking switch that is smart enough to allow the mold injection machine to finish its part before it allows the maintenance person in to make a conveyor repair. The safety control system is easy enough to manage with just a few devices and when it is focused only on safety.
Then management starts to go crazy and add a vision system to inspect the parts and delta robots to load good parts into trays. Oh yeah, they forgot to tell you that they want to see the status of everything from a human machine interface (HMI). Before you know it, the demands have you looking at managing a whole host of different systems. It’s nerve-racking just thinking about it. As you’re driving home contemplating how to handle this, you get a brilliant idea. All you need is an easy way to network everything into one system.
Software patching is vital to secure operations, but introduces more risks
It’s common to think of security updates as self-contained packages, as if the latest anti-virus or Microsoft Windows update was simply a new feature that gets added to the security stack, keeping trouble that much farther away. Yet, when it comes to patching cyber assets on industrial control systems (ICS), one needs to take a little more care than for an office or home PC. In an industrial plant setting the continuity of operations is critical. Even a minor communication hiccup or loss of view can have undesired results such as interruption of operations, or even catastrophic damage to major equipment [which can increase risk for personnel as well as production]. Regularly applying tested and validated software patches helps maintain access to plant infrastructure and provides critical cyber protection and reliability for daily operations. When operators/owners take a do-it-yourself approach to patching, they often experience unanticipated challenges and risks because of the bandwidth and resources required to properly identify and test software updates before uploading them onto the cyber assets. Manufacturer-provided patching is an excellent starting point for operators to safely execute updates and maintain operational conditions in the plant…. Assessing the relevance of a given patch can be a complex exercise. Knowledge base articles from software manufacturers that provide details on updates are generally comprehensive, and quite detailed. See 11 questions to ask.
– Edited by Mark T. Hoske, content manager, CFE Media, Control Engineering, [email protected].
Online extras
Click the section headlines above to see more on each topic.
See the Control Engineering machine safety blog, which includes networked safety information.
Control Engineering has an online cyber security training series of videos.