I/O wiring can be among the most challenging (and perhaps feared) of upgrades. When replacing input/output connections, what are key considerations? Jason Haldeman, Phoenix Contact product marketing lead specialist for I/O, offered answers to some key questions.
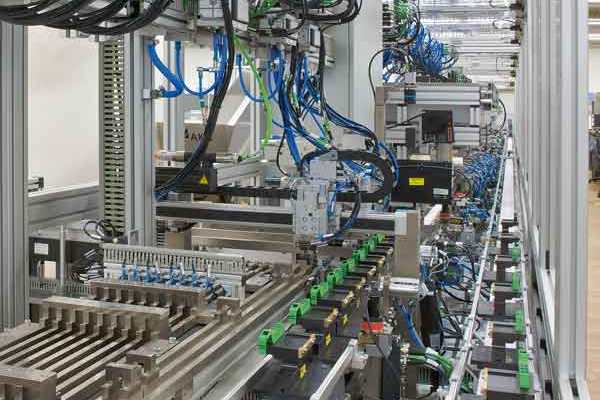
Control system wiring, at input/output (I/O) connections, can be among the most challenging (and perhaps most feared) of upgrades. When replacing I/O connections, what are key considerations? Jason Haldeman, Phoenix Contact product marketing lead specialist for I/O, offered answers. When replacing or upgrading I/O modules, consider documentation, controllers, application needs, and support.
Q: Control Engineering: Is there documentation?
A: Jason Haldeman, Phoenix Contact product marketing lead specialist for I/O: Good documentation is very important at all stages of I/O installation. You count on documentation to help with the upgrade. If you don’t know what you have, it will be much more difficult to upgrade your connections. Your supplier should have all the proper supporting documentation to simplify the I/O installation.
CE: What network protocols are required and will they be wired, wireless, serial, digital, or a combination?
Haldeman: Choosing the desired bus network is very dependent on the PC/PLC used in your current system. These suppliers provide interfaces to specific networks, limiting your options and locking you into specific networks. Moving away from their PC/PLCs would require rewriting your entire control program. For this reason most people stick with what they are comfortable programming, dictating what I/O network they use (for example, DeviceNet, Profibus, Interbus, Modbus RTU, EtherNet/IP, Profinet, and Modbus/TCP). Most new application are moving to Ethernet protocol, providing greater flexibility to incorporate options like redundancy and wireless.
CE: What functionality do attached applications need to integrate? What types of signals (analog, digital, serial, mixed…), what units (current, volts, resistance, AC, DC…), what range, and how many channels are needed? What are the sensing, signal conditioning, distributed control, isolation, and other requirements?
Haldeman: Questions like this make it very important for you to select an I/O provider that meets the flexibility your application demands. Your provider should be able to supply you with a wide, modular range of inputs, outputs, special functions, integrated wireless communication, and connectivity to fieldbus and industrial Ethernet networks. On top of your I/O needs, the supplier should be able to supply all the supporting components, such as power supplies, Ethernet switches, and terminal blocks.
CE: Will the application expand and by how much?
Haldeman: Modular I/O systems allow the user to custom-configure an I/O station to meet their exact application needs. In the future, if you need more I/O, you simply purchase additional I/O points and attach them to your existing I/O station.
CE: Will the I/O connections be enclosed or exposed?
Haldeman: This is a very important part of your decision-making. Do you use IP20 I/O inside a cabinet or lose the cabinet and go with IP67 I/O mounted directly on the machine? IP67 I/O initially costs more, but saves you with ease of installation and the cost saving of not having as many cabinets.
CE: What are among the most-overlooked considerations?
Haldeman: Support is a topic that is always overlooked until it is needed. Your I/O provider needs to be able to supply the necessary support functions to assist with questions during the installation of the I/O modules.
– Jason Haldeman, Phoenix Contact product marketing lead specialist for I/O, and Mark T. Hoske, CFE Media, Control Engineering, www.controleng.com
www.phoenixcontact.com