Coupling strategic engineering techniques with integrated management software helps unlock best-in-class alarm solutions. See five rules of alarm relevancy, three examples.
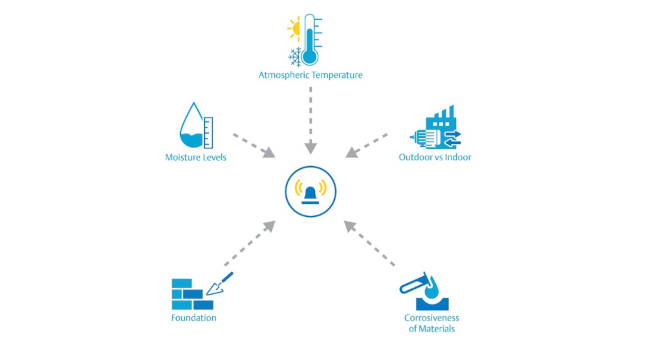
Learning Objectives
- Effective alarm management needs a system that provides consistency and context for situations.
- Tying an alarm management solution to maintenance also helps operators resolve problems before they become an issue.
- The best alarm solutions are designed with operators and technicians in mind.
Process Safety Insights
- A good process manufacturing facility needs a strong alarm system and management to provide visibility into process and equipment health.
- Companies developing an alarm system can cut down on the number of alarms and provide better context for them as well as maintain visibility.
- Alarms can do more than let someone know if something is wrong. They also can be used to let operators know about something before it goes wrong, letting them cut down on downtime before it occurs.
In an ideal world, nothing would ever go wrong in a plant and alarms to alert and guide operators and other experts wouldn’t be needed. Unfortunately, process upsets occur, machines fail and even the best personnel make mistakes. To mitigate the risk of these problems and ultimately improve safety and eliminate shutdowns, engineers must design powerful alarm solutions to provide visibility into process and equipment health.
The two primary categories of alarms – process variations and mechanical changes –must be managed holistically to achieve peak safety and performance. In many cases, these alarms are managed by two separate and often siloed groups of engineers. Moreover, they are often managed in two or more separate, disconnected applications, leading to inefficient alarm management in the plant. When process engineers and rotating equipment engineers work together using integrated control and reliability tools to develop comprehensive alarm strategies, they can create a holistic alarm management practice.
Three ways to engineer better process alarms: Design, context, visibility
When developing alarms for process operators, expert engineers focus on three main strategies. First, they ensure operators are not overwhelmed by the sheer number of alarms. Next, they prioritize and contextualize alarms to help operators know where to direct their attention. Finally, they focus on visibility, ensuring operators have instant awareness of any alarm states, no matter where they are.
1. Fewer, better alarms: 5 rules of alarm relevancy
Expert engineers focus on the number of alarms presented to operators, trying to reduce the number as much as possible. Alarm floods are the leading cause of operator confusion during a crisis. When hundreds or thousands of alarms come flooding in, sometimes in mere seconds, even the most experienced operators have difficulty focusing attention – especially when receiving multiple alarms of varying severity for the same event.
However, alarm reduction is about quantity and quality. By implementing only the most effective alarms, engineers will reduce the number by default. The simplest strategy is to check every created alarm to ensure it satisfies each of these five criteria:
-
Abnormal – The alarm is not planned or expected and is a surprise to the operator.
-
Actionable – Operator action in response to the alarm is required and available.
-
Consequence – If no action or incorrect or insufficient action is taken, an undesirable result is likely to occur.
-
Unique – Only one alarm sounds to announce an abnormal deviation.
-
Relevant – The alarm is understandable to the operator and needed in the current operating state.
By ensuring every alarm is relevant using these five guiding principles, engineers can dramatically reduce the confusion of a process upset. But to do so, engineers must also have access to the right tools for alarm design and management. Processes are dynamic, so to design the best alarm systems, the alarm management tools should also be dynamic.
Dynamic alarm management enables engineers to set scenarios for when alarms are valid and when they are not.
Example: During startup of a distillation column, operators may need to fill the column to a specific inventory and then start it boiling – a process that will result in varying flow rates and pressures. During such an operation, static alarm thresholds are far less useful than dynamic alarms that trigger based on process state.
Today’s advanced control systems feature integrated dynamic alarm management software options to monitor process states and vary alarm rules across the process, preventing nuisance alarms and operator confusion.
2. Context of the alarm is key
Today’s best alarm systems are integrated with the distributed control system (DCS) to not only display alarms to operators, but also to help them understand those alarms. When the alarm system is integrated with the DCS, alarm information is populated from the master alarm database and available for use. These contextualized alarms make it easier to deliver actionable alerts to the right people at the right time.
Example: A high vibration alert can mean many things. If it indicates under lubrication, the associated alarm should be delivered to maintenance for inspection and remediation (Figure 1). However, if that vibration alert indicates a bearing failure with imminent equipment shutdown and potential safety risk, the alarm should instead be sent to operators so they can intervene in the process. Differentiating these alarms – manually or automatically – requires the deep contextual data provided by the DCS, working in conjunction with built-in analysis tools to help cut through the noise and identify the cause of the aberration.
With thousands or hundreds of thousands of potential alarms and alarm combinations, operators need access to tools so they can better understand each alarm when it is active. The most advanced alarm management tools offer alarm help, so if an operator sees an unfamiliar alarm, one click will provide detail on causes, consequences, and corrective action.
3. Maintaining alarm visibility
Even the best designed alarm is of little value if nobody sees it. If an alarm appears in the control room, the potential to miss an important alarm increases because operators are constantly on the move. Even if operators are in the control room constantly, they may miss alarms in front of them because their human-machine interfaces (HMIs) are complex and crowded.
Today’s HMI software not only enables engineers to design visible, intuitive alarm dashboards in HTML5, it also provides mobility tools to give operators and technicians access to alarms from anywhere in the plant via mobile devices. Providing engineers with these tools will unlock far more flexibility to ensure the right people always receive the right alarms and alerts at the right time.
Tying reliability to the alarm process
To operate the plant at peak safety and performance, operators and technicians must monitor more than process performance. Plant personnel also must be notified when rotating equipment experiences problems severe enough to disrupt performance or result in a serious malfunction.
For the most critical equipment in the plant, alarm design is regulated by industrial standards. However, critical equipment often makes up approximately 5% of plant assets. Yet with balance-of-plant equipment, there are many machines that can cause safety issues or shutdowns if they fail.
Balance-of-plant equipment often relies on International Organization for Standardization (ISO) guidelines and regulations for alarm configuration. But while ISO standards are a good starting point, there are factors that fall outside of the guidelines that have an impact on alarm effectiveness. Thus, there is flexibility and reason to fine tune alarms beyond ISO standards.
Depending on where and how equipment is installed, the operating environment changes. Atmospheric temperature, location of equipment (outdoor or indoor), corrosiveness of manufactured products, moisture levels, and even the equipment foundation are just some of the environmental factors impacting alarm thresholds (Figure 2).
Asset monitoring software provides options for fine-tuning alarms to better account for environmental factors. These applications use statistical alarm calculation, leveraging historical data from sensors and the DCS to define alarm limits for specific machines. The most advanced asset monitoring tools include built-in analytics to help users identify common faults in plant rotating equipment and intervene before they cause performance upsets or safety risks.
Example: One North American power producer implemented wireless vibration monitoring with embedded analytics software and configured its alarms to identify any problems with an essential cooling water pump motor. Shortly after startup, alerts not only identified high vibration in the pump, but also – through embedded analytics – identified the problem was likely the result of a severely dry motor bearing. The alert met all five requirements of effective alarms, and it arrived in plenty of time for operators and technicians to respond before failure, while providing actionable information to speed resolution. After the bearings were lubricated the alerts stopped, and technicians and operators could see the pump operating at peak performance.
Bringing alarm management elements together
One key method to improve alarm management is simplifying connectivity between condition monitoring and control systems. Process manufacturers having the most success with a holistic alarm management program often work with condition monitoring and control technologies that are part of the same ecosystem. Robust solutions from the same provider are typically easier to integrate, as they are designed to work together.
But the benefits of integrated solutions go beyond better alarms to include better lifecycle protection. When integrated systems change due to updates and patches, those changes do not break connectivity between the systems. Integrated systems also use standardized protocols for more efficient and effective communication, and typically offer a wider range of tools for mobile connectivity. These tools are built into the software and don’t have to be bolted on and separately secured after the fact.
Perhaps the most substantial advantage of operating with a single ecosystem is operator effectiveness. Operators use a single toolset across nearly all their responsibilities, improving visibility and awareness, while reducing the hours spent training. When process tools have been selected, designed, and engineered holistically, an effective operator on one system is an effective operator on every system.
Making the most of every alarm
The most effective engineers design alarm solutions with operators and technicians in mind. They must develop systems that alert users across a wide variety of conditions, technologies, and use cases. Accomplishing this feat requires having the best alarm design and management tools from the earliest stages of engineering. Intuitive, dynamic alarm management tools that can be integrated with the control system for improved visibility and contextualization turn complex data into actionable information that can make all the difference when seconds count.
Asad Mailk is senior manager of reliability solutions; David Lee is an operator performance senior consultant and manager; both with Emerson. Edited by Chris Vavra, web content manager, Control Engineering, CFE Media and Technology, [email protected].
MORE ANSWERS
Keywords: alarm management, process safety
ONLINE
See additional process safety articles at Process Safety