Tour of the Lift manufacturing innovation institute reveals advances in automated metal forming, control design, control software, digital transformation, training and automation optimization.
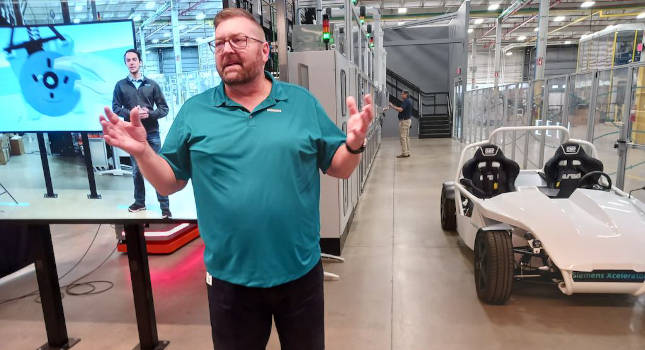
Learning Objectives
- Understand ways the Lift manufacturing innovation institute in Detroit is helping to advance automated metal forming, controls, training and optimization.
- Review examples of how automation design software optimizes design, manufacturing, implementation and repairs as shown at the Lift manufacturing innovation institute in Detroit.
- Learn the steps that lead from manual processes, to digitalization and finally to full-blown digital transformation.
Digitalization, automated manufacturing insights
- The Lift manufacturing innovation institute in Detroit is helping to advance automated metal forming, controls, training and optimization.
- Automation design software optimizes design, manufacturing, implementation and repairs as shown at the Lift manufacturing innovation institute in Detroit.
Advanced manufacturing techniques are advancing and on display at Lift in Detroit. Lift is operated by the American Lightweight Materials Manufacturing Innovation Institute (ALMMII). Lift is a public-private partnership among the U.S. Department of Defense, industry and academia, and it is part of the national network of manufacturing innovation institutes. Major participants in the Lift facility include Hexagon, Kearney, Siemens, U.S. Department of Defense and Department of Commerce.
Others, such as ABB, Fanuc and Festo, have supplied equipment to the advanced manufacturing demonstration and training facility. Siemens experts Tom Hoffman, Drew Whitney, Ed Chenhalls, Isaac Sislo, Matt Sislo and Alec Hopkins provided the Lift tour and information on April 13, during the Manufacturing in America event, in Detroit. The Siemens area at Lift headquarters can hold about 50 people for workshops on topics such as digital threads, digital twins, simulation, automation, controls, design, maintenance and industrial machinery.
Lift also works with Detroit schools to provide training and certifications in welding, robotic welding, computer numerical control (CNC), industrial technology maintenance, machining, metrology, robotics and other areas.
Demonstrations and research at Lift include how to fix industrial machines and heavy equipment with easily transported devices and systems, including robotics, controls, additive manufacturing, material sciences, metallurgy and powder metal forming in a mini, transportable foundry.
Incremental sheet forming (ISF) uses two Fanuc robots with advanced programing and motions controls to do what several larger, less portable pieces of dedicated equipment would do.
In another case, two robots work together in a welding booth using a wire arc-welding additive manufacturing process, where one robot holds and positions as another robot welds.
Linear friction welding moves one piece of metal against another, controlling speed and friction, to create a successful weld.
Other metal-forming methods in use include direct-metal laser solidification (DMLS) and a cold-spray method where high-speed impact of small amounts of metal melts and creates a bond.
Automation design software optimizes design, manufacturing, implementation, repairs
Software enables redesigns of modified equipment improve safety. Shielding added to High Mobility Multipurpose Wheeled Vehicle (HMMWV or Humvee) led to a redesign of brakes, decreasing braking distance from 150 ft to 40 ft and reducing fatal rollovers by 74%.
Another demonstration sorts pucks by color, optimizing the process first in simulation software first to speed implementation.
An explorer lab uses radio frequency identification (RFID) and real-time location services (RTLS) on pallets to help with material tracking and training. Training for work instructions and digital fabric help shorten design times. Algorithms are tested and improved many times in software so self-driving vehicles can improve safety and performance. A plug-in sensor keeps intellectual property proprietary. Virtual reality (VR) provides ergonometric testing for manufacturing methods improving operations and maintenance. Design-realize-optimize iterations improve applications of industrial Internet of Things (IIoT) applications.
Small, modular manufacturing cells
A compact assembly line is being expanded. Manufacture of an electrical control box is demonstrated on an 18-by-18-inch pallet. A Universal Robots’ collaborative robot uses machine vision to check the automated build for accuracy and sends information via a Profinet industrial Ethernet network with an RTLS. RFID routes the control box for manual rework if needed. Products are routed among Festo work cells with magnetically-driven pallets in three lanes, any direction, as needed to avoid blockages and starvation in supply and workflow. The design enables automated production with small production runs not always considered for automation down to custom work with lot size of one.
Cybersecurity automation, alarm, responses
Cybersecurity uses a unique monitoring method of security, orchestration, automation and response (SOAR) which detects and responds to anomalies in less than 1 second, as opposed to an information technology (IT) data expert analyzing and calling the plant for troubleshooting, which could take days. The Siemens solution runs codes in switches and firewalls and communicates severity alerts to a connected programmable logic controller (PLC), providing a message for low severity, light for medium and alarm and controlled system response for severe. It moves to a quarantined state, and switches over to an isolated PLC to continue operation, with a safety pause or human in the loop, as needed.
Automation design software
Using Siemens design software prior to setup of the automated line of work cells, an entrapment situation was detected and corrected in software. The need to flip orientation of an access panel door was noted, saving installation time and reducing risk.
Another software demonstration showed how a simulated redesign of a 1991 Mazda Miata part could optimize the design, keeping strength and lowering weight by 30%. Virtual commissioning validates logic used for production before part designs and the automation that make them hit the shopfloor.
Manufacturing process simulation software noted an interference point between two robots with a welding process, using virtual commissioning to save an estimated 40% time.
Mark T. Hoske is content manager, Control Engineering, CFE Media and Technology, [email protected].
KEYWORDS: Manufacturing tours, automation training, digitalization
CONSIDER THIS
When seeing automation applied in other locations, what will be your takeaway?
ONLINE EXTRA
See additional images below.