Improvements in I/O systems for field devices can make your process control system installations and upgrades quicker and more cost effective.
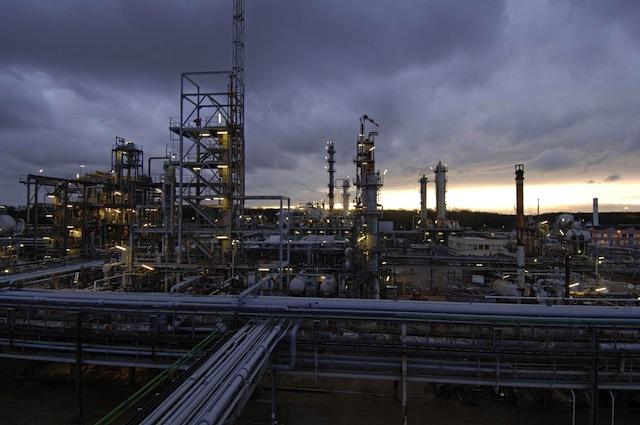
For years, and even decades, connecting field devices to process control systems has used essentially the same technology. Sure, there have been advances in fieldbus and even wireless networks, but for plain old wired devices, you connect a cable to a matching slot on an I/O (input/output) board at your controller. This works as long as the device matches the slot: a 4-20 mA with HART flowmeter requires a corresponding input. You don’t connect it to a terminal designed for a thermocouple.
Most of the time this sort of thing is tolerated, but it can cause problems. Let’s say you have a level switch mounted on a tank to trigger when the liquid goes past a specific point. That comes into the system via a digital input. What if your boss wants that changed to a magnetostrictive level sensor providing a continuous reading? You can’t put that in on the same input channel because it has a different signal type. That means changing the board or adding a new one. But maybe there isn’t room on your I/O rack. A small project can get complicated.
Control system providers hear customers ask things like, “Why can’t I assign the I/O at will to accommodate any kind of field device?” Well, given some product developments over the last few years, often the answer now is, you can. A growing number of manufacturers are now offering more flexible, or smarter, I/O systems that allow for greater flexibility. How do these work, and what can they do for you?
Depending on which control platform you use, smart I/O uses a combination of hardware and software to talk to field devices. All systems currently available require replacement of at least some components and possibly some wiring.
Two different concepts
There isn’t a one-size-fits-all approach for I/O, at least not yet. While it’s true that Foundation fieldbus, Profibus PA, or other similar approaches are platform agnostic, they require field devices that work with those specific protocols. These new smart I/O systems work with any field devices (within reason), but you need to buy a system that works with your controller. If you are using DeltaV, you need to get a system from Emerson.
There are two conceptual approaches currently at work to fill this space: Emerson’s hardware approach vs. a more software-centered idea from others like Honeywell and Invensys’ Foxboro division.
The latter is more modest in its scope. Both Honeywell’s Universal Process I/O (available early 2013) and Foxboro’s FBM247 (available now) use the same I/O device form factor and go into the same cabinets as their current offerings for Experion series C and I/A series 200, respectively. Both are designed such that any channel on any module can be configured through the control system to interact with multiple types of devices:
- Analog in/out plus HART
- Digital in/out, or
- Pulse.
Foxboro sees it as a small but strategic product improvement. Thad Frost, director of product management for control and I/O for Foxboro, explains, “It’s not an entirely new product line; it’s a subset of an existing family. We did that because it’s a proven technology. Our 200 series I/O has been out a long time, so it’s another module in the family, but it’s a really special module in that it can support a wide variety of signal types. We can take an existing controller and add this module, and there’s no real difference in the functionality.”
The appeal is apparent where a new system is being constructed or there is an extensive upgrade that may require new or more field devices. The installer does not have to match the signal type to a given input device.
“You can use any channel on the module to serve as any I/O type, and it is all software configurable using the existing control builder tools,” says Joe Bastone, solution manager for Experion control and I/O at Honeywell Process Solutions. “No configuration has to be done in the field to make that happen. You could land all the field wiring on your Universal Process I/O module, close the box, walk away, and never have to open that box again. Everything else is done from the engineering station.”
This concept replaces conventional I/O where the card or module is fixed to communicate with only a single type of device. One obvious advantage of this approach is that any module can work in any situation so that only one item is necessary for a backup. Moreover, the configuration information is resident in the host system, such that if a module needs to be replaced, one can be taken from the box and plugged in place with no preconfiguration. The host system does that automatically.
Both companies want to carry that concept one major step farther, offering complete cabinets that can be dropped in place on the plant floor ready to go. The only variable that matters is the number of channels. “The universal cabinet that is under development allows a user to have a set deliverable,” Bastone says. “It’s a remotely mounted cabinet that can hold some number of Universal Process I/O modules, perhaps 64, 96, or 128 I/O. It will be equipped with the modules, mounting hardware, power supply, and fiber optic converters to take the I/O link back to the control room.”
A different direction
Emerson, on the other hand, has created a different approach for its DeltaV architecture. Here every field device communicates via a single small characterization module or Charm. Each field device needs its own Charm that matches its signal type. A cabinet is, for all practical purposes, a 96-channel I/O card.
Keith Bellville, DeltaV SIS product marketing manager for Emerson Process Management, explains, “You don’t have the limits of conventional I/O where you had to bring all your field wiring in, land your multi-core cable on a marshalling strip, and then pick out the 4-20 mA analog inputs to take eight of them over to an individual card. We’ve replaced that marshalling with the actual multi-core coming in, and we characterize the signal there with the Charms I/O card. Each one of those is an individual channel. It is DeltaV I/O, so it’s designed to work with DeltaV controllers.”
The output from each module is Ethernet, so a single fiber optic cable can carry all the data from the cabinet back to the controller. The practical result is a small cloud within the control network that allows a user to send the information from a given field device to as many as four controllers. Functionally, this is the largest difference with the other systems already mentioned.
“Typically when you lay out your I/O in the field, it’s grouped by location, not functionality,” Bellville adds. “So in a given junction box, you might have cables from some transmitters that are part of your reactor area, but inside that same junction box, you might have transmitters that are really dedicated to the utilities area. With conventional marshalling and conventional I/O, when you bring those in, you have to say, ‘I have to bring these eight channels over to my reactor area control cards, and these other 12, I have to bring over to my utilities controller I/O card.’ With electronic marshalling, you bring them all in on one charms I/O card and send them to the reactor controller or the utilities electronically in how you target the device to which controller. You don’t have to physically wire it up to the actual I/O card on that controller.”
Putting the concept to work
These new approaches offer some functional benefits:
First, users don’t have to be concerned with the communication method for a given device. If circumstances change and you need to use a different type of field device, you can adjust that either via a software change or, at worst, a single Charm change.
Second, these platforms can facilitate upgrades and migrations, whether that means upgrades of field devices, wiring infrastructure, or the control system itself. However, there is the basic limitation that each platform is tied specifically to its respective control system, so this element could be a significant point in the vendor evaluation process.
Third, these platforms can apply to safety devices as well as conventional I/O. Unlike the others, Honeywell’s first product in this area related to safety devices and the company is now readying the standard control system I/O version as a follow-up. Given the more complicated nature of safety-related equipment with its associated testing and certification, it decided to approach this first. Emerson has conventional, intrinsically safe, and SIS Charms. Foxboro has safety modules in its product pipeline.
Fourth, hardware flexibility makes for smaller stocks of replacement parts. The ability to use one device for multiple applications has obvious advantages.
What talks to what?
As mentioned earlier, one aspect that Emerson discusses extensively is its ability to send data from any given field device to any one of up to four controllers. Foxboro and Honeywell have kept the same level of communication functionality as comes with their standard I/O, so adding these new modules doesn’t affect that ability. There are methods to send information from controller to controller on a peer-to-peer basis, but these methods are relatively complicated.
“The intimate connection between the I/O module and controller is something that our more sophisticated customers see as beneficial, mainly due to the ever-increasing security concerns that exist today,” says Bob Bristow, product manager for series C I/O at Honeywell Process Solutions. “This intimate relationship through the I/O link keeps anything that could happen at that single fabric layer from getting between the controller doing its job and the I/O performing for that controller. Bad things can happen that disconnect the I/O from its integral partner in the control operation. That’s why we picked this particular architecture.”
Foxboro’s Frost echoes that sentiment: “We call it unbounded I/O when an I/O point is not bound to a particular controller. Our I/O is typically bound. To move a specific point to a different controller would take some effort. It’s something we’re looking at for the future, but right now we don’t have that ability.”
Could this make you change?
While these new I/O systems offer additional functionality and can save both hardware and engineering costs, they are each connected to a specific control system platform and only that platform. If you are already using Foxboro I/A series 200 or one of the others, the change is very simple. If not, they’re of no help, but it is reasonable to expect that other manufacturers will follow suit one way or another.
The other choice is to change your control system provider. Adding these capabilities alone is probably not compelling enough to make you undertake a migration, but it might influence a choice of manufacturer if a migration is already planned.
In some respects the most interesting attraction may be what doesn’t exist yet. The modularity of these systems makes them easy to modify as circumstances demand. By contrast, one of the things that has impeded adoption of protocols like HART in support of larger asset management programs has been the difficulty of upgrading older hardwired device-level networks. Operators of those old platforms find it effectively impossible to add such capability because the hardware won’t allow it. That type of limitation doesn’t have to exist going forward. Adding a new communication method or protocol may require nothing more than switching the appropriate modules. It may even be changeable via software.
Peter Welander is a content manager for Control Engineering. Reach him at [email protected].
Key concepts
- Smart and flexible I/O for field devices overcomes hardware limitations.
- New systems only work with their corresponding control system, but extend field connectivity.
- Various manufacturers have tailored their own strategy for operational details.
- Arguments for adoption may not drive a larger migration project, but they could influence vendor selection.
Go online
Visit the companies mentioned in this article:
https://iom.invensys.com