New crane combines hybrid engine with automation technology to lower emissions, reduce fuel use while making workers more productive.
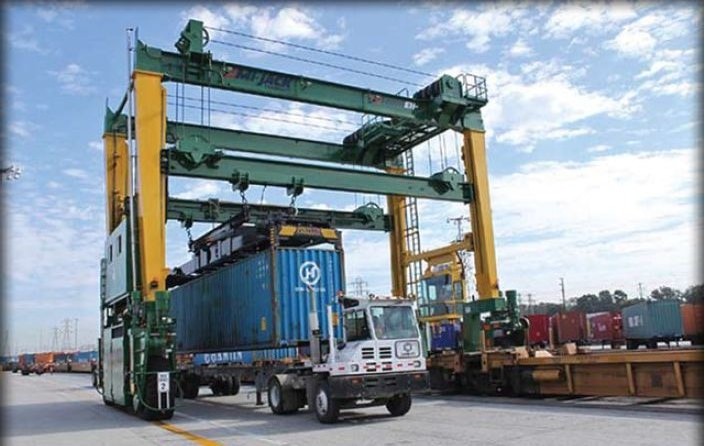
If you’ve ever spent any time in a rail yard, you’ve seen the large cranes that are used to move cargo around. Historically, these massive machines have relied on hydraulic pumps to lift heavy objects as if they were small toys.
Recently, however, crane manufacturers have been under pressure to reduce both the emissions and potentially hazardous waste that come with the use of hydraulic pumps, which consume large amounts of oil.
This has inspired crane manufacturers to follow the path of automakers in developing electric and hybrid models that are environmentally friendly but still powerful enough to keep customers happy.
An early entrant into the hybrid crane market was Mi-Jack, a Hazel Crest, Ill., company that’s known as a leading supplier of the rubber-tired gantry (RTG) cranes that are standard equipment for moving heavy items around in rail yards, industrial sites, and shipping ports.
With its new MJ 1200 REH hybrid RTG crane, Mi-Jack is not only helping its customers reduce their carbon footprint, it’s also giving them the ability to complete more work in a shorter amount of time. This became apparent after the first MJ 1200 REH was deployed in a large rail yard in Long Beach, Calif.
“Our customers are seeing 60% to 70% in fuel savings and 80% lower emissions over a traditional hydraulic crane,” says Harry Schmidt, vice president, research and development for Mi-Jack.
Operators’ favorite crane
Operators also note that the Mi-Jack hybrid allows them to pick and lift containers 20% faster than a traditional hydraulic crane. “The 1200 REH is the operators’ favorite crane,” Schmidt declares. “They love how smooth it is; it’s very easy to drive. It allows greater productivity, and has lower maintenance costs.”
Schmidt attributes this crane’s performance—and resulting popularity—to its underlying technology platform, which consists largely of off-the-shelf hardware and software from Schneider Electric.
When it set out to develop a hybrid crane, Mi-Jack wanted to deliver a product with a rechargeable battery pack. This way, if the crane was low on power it could recharge itself.
Mi-Jack’s first step was forging a partnership with EcoPower, a Montreal-based company that had developed a power source that combines batteries with a small diesel engine.
“Since we only needed to size the generator to charge the batteries, not actually lift the load, we were able to use a generator that’s one-third the size of a typical generator,” Schmidt recalls. “Obviously, our customers also see a substantial decrease in fuel costs since the generator is much smaller and only used part-time.”
To take full advantage of EcoPower’s hybrid engine, Mi-Jack needed to collaborate with a company that had experience with electric drives. That’s where Schneider Electric entered the picture.
“When we got serious about developing the hybrid platform, we started evaluating companies that could support the development of our product,” Schmidt explains. “We weren’t drives people and we needed to utilize someone else’s expertise. Schneider Electric was the only company that had both the required technical expertise and a platform that was compatible EcoPower’s hybrid engine.”
Technology platform
The Schneider Electric platform starts with its Modicon LMC058 controller, which is both a motion controller and programmable logic controller (PLC) in one product, along with 1 Altivar 71 drive and a Magelis human machine interface (HMI).
The LMC058 controller is part of the Schneider Electric MachineStruxure architecture, an integrated solution for managing industrial machines, based on flexible hardware platforms and SoMachine, a single modular, reusable software suite.
Though this is off-the-shelf technology, a bit of customization was needed to maximize the performance of Mi-Jack’s new hybrid product. To that end, eight Mi-Jack employees were flown to Schneider Electric’s OEM Technology and Solutions Center in Raleigh, N.C., to collaborate with Schneider’s drive experts.
Designing and commissioning the HMI control panel also was an intricate process. “The crane operates in -30 F up to 120 F,” Schmidt says. “We needed a panel that was climate controlled and could withstand the vibration of the crane driving through the yard. We were really looking to Schneider Electric for their expertise in building a pretty complex panel.”
“So far everything has been easy,” Schmidt concludes. “The SoMachine software allows us to incorporate the drive, HMI, and PLC parameters all in one envelope. We also get the benefit of any new or enhanced function blocks because they can be reused between applications or machines.”
To assist with programming, Schneider Electric brought one of its German crane programming specialists to the United States. A lot of time was spent translating hydraulic functions to drive functions — not an easy task since the drive controls are not as forgiving as hydraulic. Therefore, precise math calculations were required for stopping and starting, and the group spent a lot of time fine-tuning the drives and synchronizing multiple motors.
After receiving training on the SoMachine software, Schmidt says, Mi-Jack’s primary programmer has taken over all programming functions and is finding the transition a smooth one.
The success of the MJ 1200 REH hybrid RTG crane has led Mi-Jack to develop other electric cranes and products, including a crane with two Hoist VFDs and controls for lowering and raising mining equipment into an extremely deep coal mine.
Learn more about energy management at the Schneider Electric website.
Visit the Mi-Jack website to learn more about its products.
This article appears in the June Industrial Energy Management supplement to Control Engineering.