End users and machine builders must find common ground to implement more efficient actuation technology and go green in many ways.
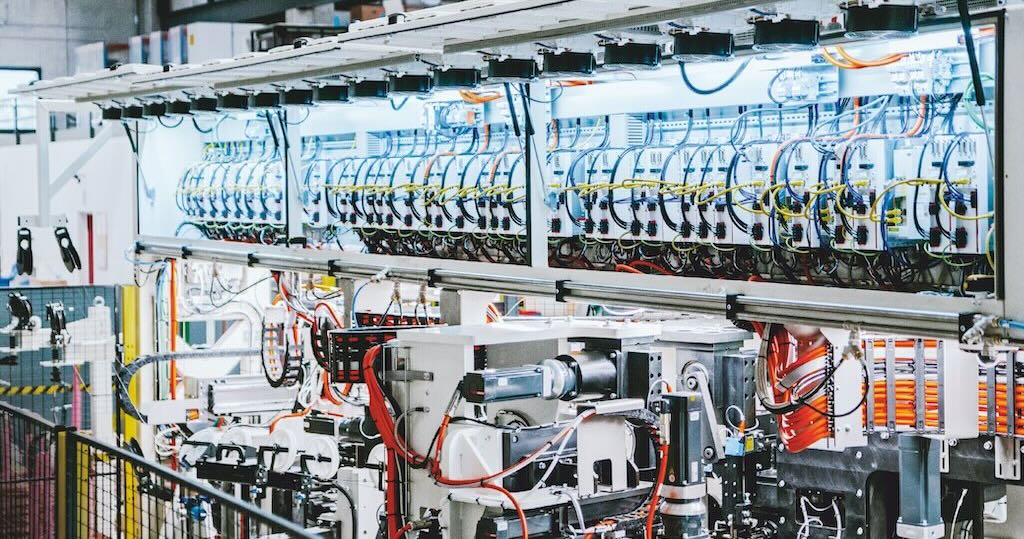
Learning Objectives
- Learn why energy efficiency is good business and how it benefits manufacturers on multiple levels.
- Understand how motion control with electric cylinders and regenerative energy solutions reduces total cost of ownership (TCO).
Energy efficiency insights
- Focusing on energy-efficient motion control not only aligns with sustainability goals but also offers substantial long-term cost savings and operational efficiency.
- Electric cylinders and regenerative energy solutions not only improve efficiency but also cut down maintenance costs and facilitate smoother operations for manufacturers.
When it comes to energy efficiency, the gears are always turning. It’s not just for feel-good vibes – there are many reasons to make industrial motion control consume less power. Sustainability is more important as businesses look to the future and work to meet standards. More than anything, though, it makes good business sense.
Of course, no one sets out to waste more money and resources on inefficient equipment. What often causes these situations is miscommunications between the original equipment manufacturer (OEM) and the end user. Rather than focusing on the total cost of ownership (TCO), the two more often duke it out over the upfront costs.
Providing a cost-competitive system that meets all throughput and quality requirements is important. However, some long-term considerations can be missed in this process.
Building a comprehensive energy efficiency plan for motion control must take a two-pronged approach. First, machine builders need to take a long-term view of component selection. Second, OEMs and end users must start capturing all the electricity that’s wasted to make the plant more efficient overall. Consider these examples that cover both aspects.
How electric cylinders push the limits of energy efficiency
At the device level, energy efficiency in motion control is a mixed bag. Rotary motion technologies keep evolving in ways that save energy. But linear motion faces continued challenges, especially in high-speed, high-force actuation applications.
Pneumatic or hydraulic cylinders were often used in these scenarios. However, on top of their excessive footprint, they’re inefficient tools. Pneumatic and hydraulic actuators need to run compressors or pumps even when the cylinders are idle. Their efficiency rates average 10 to 25% for pneumatics and 40% for hydraulics. However, with damaged seals, leaky hoses and general wear, those numbers drop.
Electrification can offer a clear path forward. Electric cylinders consume power when enabled and while the cylinder is in motion, so their rate of efficiency can be measured up to 80%. While most will note the higher price when compared to the cost of a traditional solution, electric cylinders offer an optimal TCO and a much faster ROI through the combination of higher efficiencies, reduced maintenance and enhanced ease of use.
The advances in electric cylinder technology ensure users don’t have to sacrifice performance to gain these advantages. Some electric cylinders offer peak forces of 6.5 to 25 kN with stroke lengths from 150 to 250 mm.
When evaluating options, be sure to select a feature-rich device with integrated safety encoder, temperature and current monitoring for predictive maintenance, and auto configuration that requires the user to scan in the electronic nameplate. This removes the mystery of implementing these systems, which previously felt closer to “dark arts” than engineering.
Electric cylinders with optimal mechanical designs can deliver direct-drive solutions, with no belt or gearbox, and a backlash of just 15 µm. By selecting a device that’s ISO 15552 compatible, users will have a direct drop-in replacement for pneumatics or hydraulics. Users can adapt machine designs or retrofit legacy equipment. As a result, users can make wide-ranging motion systems more efficient on the component level.
Greener plants with effective regenerative energy
When looking at the plant or just machine level, eliminating compressors, pumps and other energy-leeching devices can have some effect. However, that doesn’t account for all the usable energy that often goes untapped. Engineers often handle regenerative energy in motion systems by bleeding it out through a braking resistor. It’s an age-old, low-tech answer to a complex problem that’s ripe for an update.
With universal energy recovery modules, end users can route that electricity back into the power grid. Users can connect one of these innovative devices to the 24 Vdc supply on the drive and mains along with a DC-link connection. Then they manage braking power as it gets kicked out by the drive.
By adding this, OEMs can help guarantee their machines deliver efficiency. However, with universal energy recovery devices, end users also can add them to existing equipment with third-party motors and drives and still capture the energy that would otherwise be wasted.
Universal energy recovery modules with an EtherCAT connection allow for monitoring of these savings as well. Engineers can connect the unit to a central PC-based controller and access the data locally or at a higher level. For some units, this doesn’t require any special configuration. Implementing these connected technologies in greenfield or brownfield environments helps companies ensure they’re hitting sustainability targets and can help the manufacturing team prove they’re doing their part.
A comprehensive look brings things into focus
Updating motion control with electric cylinders and regenerative energy solutions reduces TCO on any piece of equipment and the return on investment (ROI) is almost immediate. Eliminating energy-sapping compressors, pumps and other mechanical devices that also gobble up floorspace allows end users to do more in their existing facilities rather than expanding or taking up new real estate. Finally, implementing servo-electric technologies speeds up commissioning and reduces support calls for the OEM and maintenance costs for the end user.
Taking a comprehensive view of energy-efficient motion control technology helps machine builders and end users find common ground. This makes the future of manufacturing look greener in many ways.
Matt Prellwitz, drive technology product manager, Beckhoff Automation LLC. Edited by Chris Vavra, web content manager, CFE Media and Technology, [email protected].
MORE ANSWERS
Keywords: energy efficiency, motion control
ONLINE
www.beckhoff.com/condition-monitoring
CONSIDER THIS
How are you making your plant facility more efficient?