Remote management and monitoring applications help keep operations up and running. External remote management and monitoring teams provide specialized operational knowledge to help with automation and control system issues.
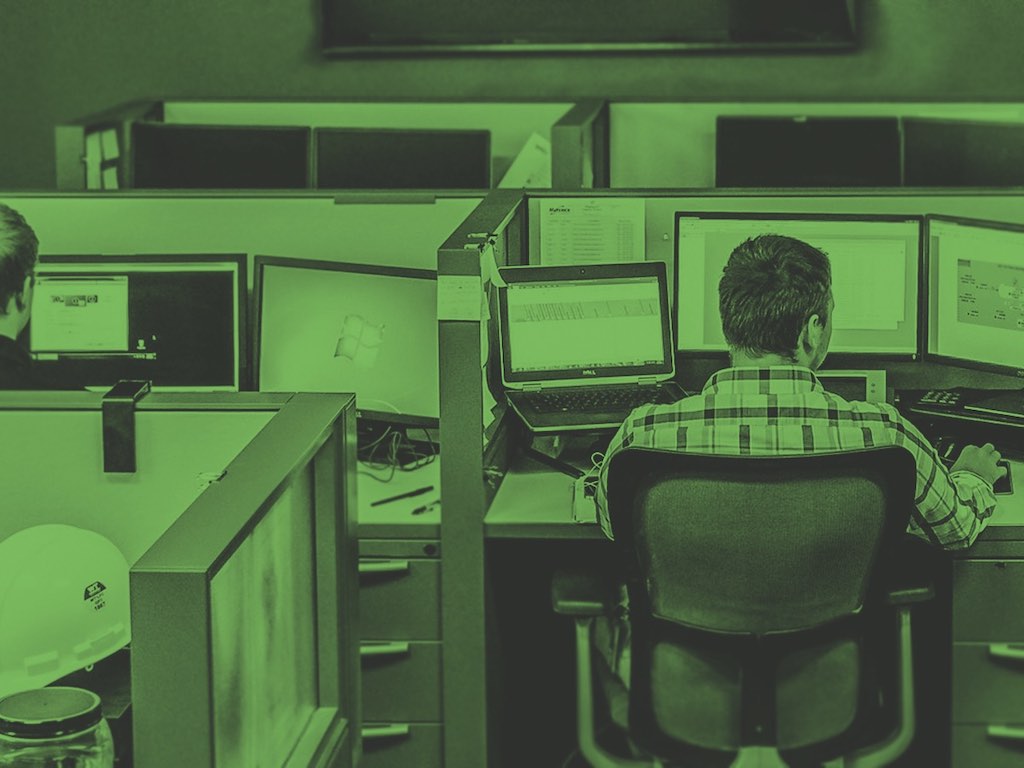
Remote monitoring technology is not new. However, due to technological advances (e.g., open systems, wireless technology, smart manufacturing devices, high-speed network connections, etc.) over the past several years, the ability to remotely manage and monitor critical automation and control systems in real time has come to the forefront as a secure and cost-effective means for manufacturers to improve operational efficiency and tap offsite resources for additional production support.
Offsite remote service support can handle a variety of tasks and services including incident management, system backup and recovery, data analysis and retrieval, software updates and patches, real-time monitoring of software and systems, and online automation and system programming.
Key advantages manufacturers should consider when engaging a remote offsite team include:
- Provides 24/7/365 support
- Offers a broad platform-agnostic knowledge base to support a mix of systems
- Reduces costs by helping prevent downtime
- Eliminates the need to find and retain additional in-house automation expertise
- Delivers positive return on investment (ROI) as benefits exceed costs for process improvements
- Often results in lower cost than onsite alternatives
- Supports flexible, customized services for specific facility requirements
- Performs upfront assessments on new projects
- Offers system scalability, flexibility and customization
- Builds a working relationship with automation experts who deliver continuous improvement and sustaining services support.
Workforce woes
In today’s competitive world, manufacturers are having to transition from their traditional systems to more modern tools and strategies. Often, however, they find it increasingly difficult to justify, recruit and train automation personnel on new system upgrades or infrastructure. They also face workforce attrition and retirement, which places additional tasks on personnel who already have heavy workloads. They simply do not have the bandwidth or, in some instances, the level of experience to effectively diagnose system failures or deal with the daily process issues that arise, leading to the potential for equipment failure and downtime.
To help ease the load, external remote management and monitoring teams provide specialized operational knowledge to help with automation and control system issues. Typically, legacy and new systems alike require original equipment manufacturer (OEM) expertise and support. However, due to equipment obsolescence, few OEMs are supporting the spare parts manufacturers’ source for their legacy systems.
A platform-independent third-party automation solutions provider can provide operational expertise on a mix of hardware and software platforms, working with OEMs directly, based on your manufacturing facility requirements. They can deliver application support services and production optimization solutions, while helping to remotely maintain, continuously improve and prevent automation and control issues from happening.
Managing the unexpected
Despite system or procedural warnings, situations can and do arise when manufacturers least expect it, especially during the weekend, evening, holiday or vacation hours. Often, a manufacturer’s in-house team can handle many of the day-to-day automation and control issues that come up if given enough time. However, who do you call when the unexpected happens and staff resources are stretched thin or unavailable?
At any time, automation hardware and software issues (e.g., malfunctioning control valves, faulty wiring, poor process loop performance, control system and software updates, data recovery and more) can quickly escalate and cause facility downtime, safety risks and increased operational costs. How long it takes your in-house team to respond is critical to personnel safety and the manufacturing facility.
During these times, a third-party remote management and monitoring application support team can work with in-house personnel to:
- Ensure 24/7/365 immediate response and proactive support
- Identify, diagnose and debug automation equipment issues (e.g., server failures or malfunctioning control valves) before they disrupt production
- Identify and monitor key parameters that typically indicate most failures. Examples include hard disk usage, percentage of used memory, warnings generated by the automation system, 24/7 network data and information related to equipment operation, such as vibration parameters, temperature readings, etc.
- Diagnose, interpret and communicate current system code issues
- Monitor faults and processors
- Monitor network usage and connectivity
- Perform daily routine system checks
- Help get production going again more quickly after equipment failure
- Help perform routine system backups so operational improvements are captured and preserved
- Supervise software updates and patches for cybersecurity protection
- Monitor key alarms.
Now that we’ve looked at some challenges and how working with external remote teams can help resolve automation application issues, let’s look at how manufacturers can choose the right partner and move past any uncertainties or fears about their intellectual property.
Documentation is key
As with any contractual agreement between parties, it all comes down to good documentation. Before the team lead signs on the dotted line, consider the following items when looking for and working with a trusted platform-independent third-party automation solutions provider or systems integrator:
Safety. Before starting any project, both the manufacturer and remote partner need to be aware of all safety policies and procedures. Any tasks can be performed in-house or remotely, with manufacturers making decisions based on their specific circumstances. When remote changes are made to a facility’s systems, both parties should follow precautionary measures to mitigate safety risks and ensure the working environment remains safe at all times.
Security. Manufacturers should have good security policies in place and use best practices when working with secure setups across the enterprise. Depending on where the remote monitoring will be performed, a manufacturer’s highly-qualified information technology (IT) personnel need to ensure a secure location to protect intellectual property (IP).
They must also ensure safe and secure remote firewall access to systems, giving unique access via usernames and passwords to the third-party solutions provider. Security coverage to prevent hackers is a two-way street in remote setups, so high priority should be placed on it from both sides of the firewall.
Manufacturers also should consider visiting the third-party locations to see first-hand what lockdown protections are in place, including building security.
Flexibility/customization. Being able to have the flexibility to customize and make changes on the fly is nice, but upfront planning to prevent surprises from happening ultimately keeps costs from escalating later. Engaging a third-party partner early on in a project is key, as they become more familiar with your platforms, as well as intimately knowledgeable about your specific product manufacturing process. Ideally, they can help write the process code needed for any future programming changes.
Chain of command. Ensure both teams have the proper escalation protocols—a point of contact and knowledgeable staff available that can escalate issues for resolution. This is where on-call, 24/7/365, third-party remote operation teams are extremely important in off hours.
Project tracking. Find someone who is flexible to your needs and will use some form of ticketing system for tracking calls and issuing reports. It is important to document every call and incident for archiving purposes and historical recall.
Costs. Cost is always a major factor for any business. If the remote services deliver a positive ROI, then the benefits exceed costs for process improvements. A cost savings also can be realized when you reduce the amount of in-house personnel having to perform or be trained on critical automation tasks, which limits disruptions to their daily operational routines. Another factor to consider is the potential cost associated with system failure or downtime, resulting in lost production and product quality. Can you really afford to have a full-time employee “on call” solely to field potential problems that arise? Proactive third-party remote management and monitoring handles the problems for you and can prevent any safety lapses as well as increase efficiency saving costs in the long run.
The right third-party partner can be a major advantage for manufacturers who want to use the latest remote management and monitoring tools and techniques as part of their day-to-day routine. A trusted partner will answer any questions to remove any uncertainty and doubt from the process. A platform-independent automation solutions provider can provide unbiased remote management and monitoring experience for a range of products and technologies to keep facility operations up and running 24/7/365.
Case study: Loop performance optimization sweetens product quality
Remote management and monitoring of automation and control systems helps manufacturing facilities react quicker to situations to prevent unexpected events from happening. The following is an example of such an event.
The customer needed an automated method to detect poor process loop performance in a legacy control system. Loops optimized during commissioning and startup quickly experienced performance degradation. The goal was to correct poor loop tuning before significant process losses were incurred and to monitor and to communicate loops trending in the wrong direction.
Engineers in the Maverick Technologies PlantFloor24 global operations center teamed with our operation consulting group to mine the customer’s extensive historical controls database to analyze trends and data patterns (see Figure 1). The team tested algorithms to create actionable reports, which were then verified to prove the underlying effectiveness of the proposed solution. The team also analyzed the total time valves were in auto/manual mode, total valve travel, the flow coefficient (CV) percentage of the valve and other relevant variables and assigned a final score to each loop. The score of each loop was updated automatically. Threshold limits were defined, and triggers were set once a loop started trending toward an unoptimized state.
Control room operators now are notified of critical loop trends. A daily report is compiled for the facility operations team that indicates unoptimized loops. On a weekly basis, the operations team receives a top 10 list.
Many of the loop problems were symptoms or indicators of more important process issues. For automated monitoring systems to be effective, the systems must be more robust than the systems they are monitoring. Several commercial software solutions exist. However, they are not well-suited for legacy automation systems and cannot accurately identify process issues.
Simple repeatable solutions were the core of this effort. In one case, a loop allowed periodic product loss due to poor tank level control. While the product loss was important, the volume was not sufficient to make the correction of the loss an actionable priority. Further investigation helped the team determine the product loss was an indicator of a poorly coordinated process that was ultimately affecting product quality and significantly reducing the value of the finished product.
This article appears in the Applied Automation supplement for Control Engineering and Plant Engineering.
Maverick Technologies is a CFE Media content partner.
– See other articles from the supplement below.