Faster deliveries, movement toward carbon neutrality and motion control designs that decrease reliance on lubrication are among trends from igus, a German-based manufacturer of motion plastics.
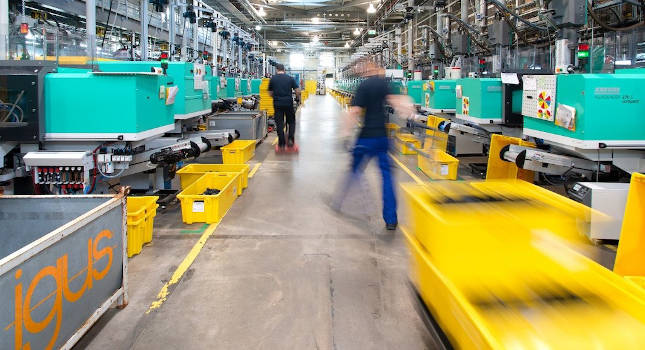
Learning Objectives
- Learn about supply chain modifications, manufacturing additions for a motion component supplier.
- Examine steps toward a climate-neutral production goal by 2025.
- Understand moves to eliminate lubrication in many motion control applications.
Decreased delivery times amid COVID-19 and supply chain challenges of the past two years, increases toward carbon neutrality, and motion control designs that decrease reliance on lubrication are possible in the automation industry. These are three trends outlined in a March 24 press release from igus, a manufacturer of motion plastics based in Germany. The announcement also detailed record revenue growth and customers. More details and other trends from igus follow.
Supply chain modifications, manufacturing additions
Customers of motion plastics products, from drive cables to gears, continued to receive a very high proportion of orders quickly in 2021. More than 80,000 items have since been in stock additionally or in higher quantities. In 15 global distribution centers, the rate of catalogue products shipped the same day or within 24 hours increased to at least 25%. Online sales increased 55% in 2021.
Shortages in many markets have led to more investments. Since 2020, production in Cologne has been increased or modernized by 300 injection-molding machines; 200 are ordered. The new production building in Cologne with an additional 20,000m² of production space is expected to be completed May 1, 2023. New storage locations for 12,000 pallet positions were built in 2021. Plans for a further expansion in after igus acquired adjacent areas of 20,000m², are in progress. At the 35 foreign subsidiaries, expansion areas totaled 60,000m².
“Novel flexible cable solutions such as the e-skin flat [cleanroom cables for chip production] are in high demand, especially in the booming semiconductor industry,” said Peter Mattonet, industry manager cleanroom at igus. “Being able to replace a cable in a matter of minutes is a revolution for manufacturing and increases much-needed output,” he said.
Increases toward carbon neutrality
On the way to climate-neutral production goal by 2025, 100 older injection-molding machines were replaced with models that are 40% more energy-efficient. Energy management was further optimized; an ISO certificate for this will follow at the end of March. The company planted 15,687 trees in 23 countries. Plastic waste in production that cannot be directly recycled was reduced by 21%.
Less lubrication, other trends
The igus global energy chain recycling program, called “chainge” grew in recent years and was rolled out internationally. This spring, igus will present its first energy chain product made from 100% recycled materials.
Improving the world of motion with motion plastics without lubrication, continues to be a company goal.
The four-year-old smart plastics business unit also launched 12 new products for condition monitoring, preventive maintenance and the Internet of Things (IoT) in 2021.
Low-cost robot integration via online consultation at a fixed price is offered with igus RBTXpert in 2021 and a digital and human service. Costs for typical solutions amount to €8,500 for hardware and 20 hours of integration work, which means a few months’ worth payback time. Internationally, the service is available in seven countries, with another 14 in the pipeline. Three new online tools brought the online services total to 58.
“Customers’ do-it-yourself engineering in the web doubled last year to 5,000 value-added uses per day,” said Frank Blasé, igus ceo.
About igus
igus GmbH develops and produces motion plastics. Motion plastics are self-lubricating, high-performance polymers improve technology and reduce costs where things move. In energy supplies, highly flexible cables, plain and linear bearings, and lead screw technology made of tribo-polymers, igus is the global market leader. The family-run company based in Cologne, Germany, is represented in 35 countries and employs 4,150 people. In 2020, igus generated a turnover of €764 million. The company has 234,000 articles from stock; service life can be calculated online. Recent internal startups include ball bearings, robot drives, 3D printing, the RBTX platform for Lean robotics and “smart plastics” for Industry 4.0. Environmental investments include the “chainge” program (recycling used e-chains) and participation in an enterprise that produces oil from plastic waste (Plastic2Oil).
– Edited by Mark T. Hoske, content manager, Control Engineering, CFE Media and Technology, [email protected], from an igus March 24 press release.
KEYWORDS: Motion plastics, motion control
CONSIDER THIS
How are your organizations environmental goals being met; and are you helping your customers, as well?