Avoid trips and maximize steam output by reviewing your control equipment, strategy, and tuning.
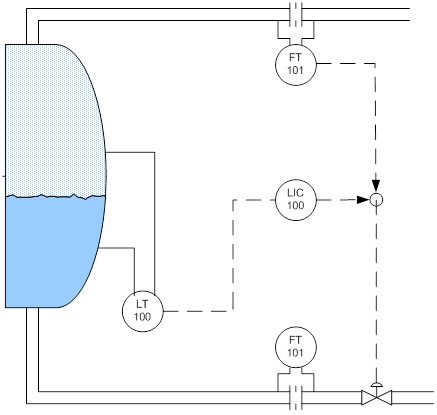
Inadequate control of drum level in a natural-circulation boiler can cause trips on a frequency ranging from a few times a year to once a day. Each boiler trip generates expenses that can cost from tens-of-thousands to hundreds-of-thousands of dollars depending on the circumstances. Control engineers can substantially improve level control performance by following a structured approach to troubleshooting the boiler drum level control system including reviewing the control equipment, the strategy, and the controller tuning. This approach can substantially reduce the number of boiler trips, providing a substantial financial benefit.
Drum level control basics
Natural-circulation boilers are widely used in various chemical processing and related industries. The design principle uses the difference in density between cooler water in the downcomer and the steam/water mixture in the riser to drive the steam/water mixture through the tubes. The boiler drum separates steam from water and contains inventory to accommodate operational changes. Water enters the riser tube, is heated, and undergoes a transition from a single-phase liquid to a mixture of saturated liquid and steam. As heat input increases, the proportion of steam vapor in the riser tube increases.
A high-priority challenge to the control engineer is the ability to control the water level in the drum very precisely. When the water level gets too high it can result in water carryover into the superheater or turbine, potentially causing damage or outages in the turbine or boiler. A level that is too low can expose the water tubes where they connect to the drum, causing them to crack or break. A boiler trip interlock is supposed to prevent these types of damage, but boiler trips can take considerable time to clear, during which the expensive production equipment is often forced to sit idle.
Shrink and swell
The void fraction is the percentage of steam by volume in the riser tube. The quality is the percentage of steam by weight in the riser tube. As the quality increases, so does the void fraction. Faster changes in the void fraction are seen at lower steam quality and lower steam pressure. Increasing the boiler firing rate increases the void fraction, which in turn pushes water out of the riser tube into the drum, increasing the level of the drum. This effect is known as swell. Likewise, reducing the boiler firing rate reduces the void fraction and water flows downward from the drum into the riser tube, reducing the level of the drum. This effect is known as shrink.
If the steam flow out of the boiler increases, the drum pressure will drop and the boiling rate will increase, increasing the void fraction in the tubes and drum. The increase in the void fraction will push water into the drum, causing swell. The inventory of the boiler must be reduced to accommodate the increased void fraction. The opposite effect is seen when the steam flow out of the boiler decreases or when cold feedwater is added to the drum. The resulting reduction in drum pressure causes the boiler level to shrink.
While the control engineer must pay careful attention to shrink and swell in determining the boiler drum level control strategy, he or she may be surprised to find that changes in these factors sometimes have the opposite effect as was expected. For example, an increase in cold feedwater flow would be expected to increase the inventory in the boiler and increase the drum level. But in the short term, increasing feedwater flow tends to quench the boiling in the drum and also potentially in the tubes. As shown in Figure 3, this may result in a temporary drop in the boiler drum level. Eventually the drum level increases due to increasing inventory. On the other hand, a decrease in feedwater flow tends to increase boiling in the drum and tubes. The result is a temporary rise in the boiler drum level. If the feedwater temperature is higher, close to the drum temperature, these effects will be less noticeable and may disappear completely.
Drum level measurement
Naturally, the control engineer’s first step in maintaining drum level control is to ensure accurate boiler drum level measurement. However, this may be complicated by the fact that the steam drum itself may not be perfectly level. Even at steady state conditions, turbulence in the drum can cause the level to fluctuate. A changing rate of water inflow and steam outflow adds to the potential for measurement error. Measurement of boiler steam drum level using a differential pressure transmitter must take into account the physical properties of the fluid. The drum contains a two-phase mixture of water and steam at saturation conditions. The densities of water and steam vary with saturation temperature or pressure. The density of saturated steam above water must be considered, as well as the density of saturated water in the drum. Suppliers of boiler drum level transmitters will provide instructions for calibrating transmitters that take these factors in account.
Understanding response dynamics
Tuning the control loops requires an understanding of the response dynamics. Open-loop step testing as shown in Figure 5 can help provide this understanding. The feedwater valve is stepped while monitoring the response of the feedwater flow, boiler drum level, and steam flow. In the example shown in Figure 6, the feedwater flow does not respond well to changes in the feedwater valve at the points indicated by the red marks. The problem is a sticky valve. The controller cannot be tuned to fix this problem. Instead, the control valve needs to be fixed. Of course, it’s not possible to make a control valve that responds perfectly, but it should respond to 0.5% steps or smaller in the controller output. Figure 7 shows a flow control valve that responds well to control signals.
After the feedwater loop is operating correctly, it’s time for the control engineer to focus on the drum level. The goal is to achieve sharp transitions in the level slope in response to a change in feedwater flow rate because dead time or delay is destabilizing. Figure 8 shows a good example of a response without any delays. The dynamics of the boiler may include dead time that cannot be eliminated, so to maintain stability in this case, the tuning of the controller must be slowed down.
Types of level control systems
Single-level element control as shown in Figure 9 uses only the level measurement and the feedwater valve. The controller responds to a proportional signal from the drum level transmitters by generating a proportional output to the boiler feedwater valve when needed. This approach is often used when starting up a boiler and there is no steam flow or when a flowmeter has failed. The drawback of this strategy is that the level is subject to uncontrolled disturbances from the steam header and the feedwater. For example, if the feedwater header pressure rises, the feedwater flow to the boiler also increases. Without a feedwater control loop, this situation would be uncorrected until the level changes. In addition, the installed characteristics of the feedwater valve may compromise level control performance over a large operating range.
Two-element level control as shown in Figure 10 adds the steam flow as a feedforward element to the level controller output. A steam mass flow rate signal is used to control the feedwater flow so that feedwater demand can be adjusted immediately in response to load changes. The level controller is used to correct any imbalance between the steam mass flow out of and the feedwater mass flow into the drum. This approach delivers more effective drum level control than a single element. It is well suited for use on a single boiler with a single feedwater pump using a constant feedwater pressure. A potential weakness is that the installed characteristics of the feedwater valve may compromise level control performance over a large operating range. In addition, steam feedforward may need to be characterized when using this approach.
Three-element level control as shown in Figure 11 is the most common boiler drum level control strategy. A feedwater flow loop slave is added to the two-element strategy. Three-element level control linearizes the feedwater flow with respect to the steam flow and the level controller output. The control loop now requests volumetric flow change, not just a change in the valve position. This strategy attempts to compensate for changes or disturbances in steam flow and feedwater flow based on the principle that flow in equals flow out. The installed characteristics of the feedwater valve are no longer an issue because the flow controller can compensate. Using this approach, the steam feedforward element can be a simple gain without requiring characterization.
Tuning the control loop
The recommended procedure for level control tuning is to tune the feedwater flow loop first to ensure that it’s fast, stable, and does not overshoot. Then the control engineer should perform open-loop tests on the drum level loop, being careful to start small. Evaluate the response for a number of step tests. Figure 12 shows a well-behaved drum level process without any dead time.
The lambda tuning method for controllers usually provides stable control loops. The blue line in Figure 13 shows the response provided by lambda tuning to correct for a disturbance. The lambda value (λ) is the arrest time where the level deviation is maximum and represents 1/6 of the total recovery time. The lambda tuning equation is
where
TARR is the arrest time, which is equal to lambda. The greater the process dead time, the greater the lambda value that is required.
Feedforward is generally set up to maintain a 1:1 mass relationship between steam flow and feedwater. If both flow meters are set up for the same span in engineering units, e.g., pounds per hour, then the feedforward gain is normally set to 1.0. Also, consider accounting for other input and output flows that consume steam, such as soot blowing and blow down. A dynamic feedforward approach may be more beneficial than a straight gain.
Handling disturbances
Various types of disturbances can create level control challenges for the control engineer. For example, Figure 14 shows a disturbance caused by variations in process steam demand. In this particular application, the steam flow disturbance is an inherent part of the process so it cannot be corrected. The three-element drum level control is kept busy reacting to the variations in steam flow to maintain the drum level at a relatively constant value. Substantial variations in the level are seen when the drum level control goes into manual.
If a steam flow increase causes the drum to swell, the level will increase but the feedforward signal will cause the feedwater to increase, potentially compounding the problem. Most boilers do not show appreciable shrink or swell from feedwater because the feedwater is heated and drum baffling is used. The level controller will attempt to counteract the effect of the feedforward. The solution in many cases is to filter or delay the feedforward steam signal. This accommodates the change in boiler inventory that is occurring.
Conclusion
Drum level control problems can cause production inefficiencies, product quality issues, and production limits, and in some cases can even create safety risks. In extreme cases, level control problems have resulted in costs of millions of dollars per year. Proven methods are available to substantially improve drum level control. The control engineer can perform a simple but systematic analysis of the control system to establish the root cause of the control problem and reestablish effective drum level control.
Andrew W.R. Waite is principal process control consultant for Emerson Process Canada.