Simplified electric motion, intelligent motion terminal flow control, decentralized I/O modules are among products shown at the Festo booth at Pack Expo Las Vegas, Sept. 27-29.
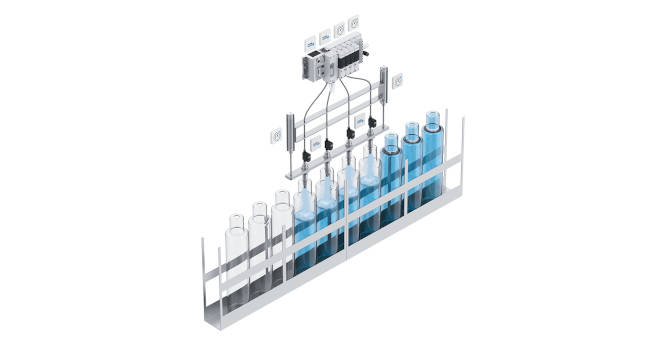
Learning Objectives
- Simplified Motion Series Electric Motion bridge the gap between pneumatics and servo motion.
- Nitrogen dosing solution for filling lines is based on the Festo Motion Terminal and apps for multi-channel flow control and selectable pressure.
- Ethernet-based CPX-AP-I Decentralized I/O gives remote I/O greater capabilities.
Among Festo products at Pack Expo Las Vegas, Sept. 27-29, are the Simplified Motion Series Electric Motion to bridge the gap between pneumatics and servo motion; a solution for nitrogen dosing on filling lines based on the Festo Motion Terminal and apps for multi-channel flow control and selectable pressure; and Ethernet-Based CPX-AP-I Decentralized I/O to give remote I/O greater capabilities. More about each follow from Festo, Islandia, N.Y.
Festo Simplified Motion Series Electric Motion
The Festo Simplified Motion Series (SMS) new features for all-in-one integrated-drive axes is IO-Link control that can be used for cost-effective, multi-position applications. SMS combines the simplicity of pneumatics with the benefits of electric automation. SMS takes proven ball screw axes, toothed belt axes, mini slides, electric cylinders, piston rod, and rotary actuators and integrates them with an onboard servo drive. Users commission two-position functionality via onboard push buttons without additional software needed.
When controlled with IO-Link, which is a standard communication feature of SMS axes, positioning along the axis length is infinitely variable. When used like this, SMS axes offer an alternative to more expensive and complex traditional servo motion. It is lower in cost compared to traditional servo motion solutions. Setup is as simple as pneumatics. This opens SMS to applications that have previously been cost-prohibitive to electrics, including conveyor material handling, and applying electric motion in mobile applications.
Via IO-Link, technicians can remotely adjust movement parameters, including infinitely variable positions and speed. They also can copy and backup functions for parameter transfer and read functions of essential process parameters.
More details about SMS actuators
SMS actuators are applied in positioning, indexing, clamping, feeding, and cut-to-length tasks where electric automation adds proficiencies and value. Ordering, inventory, and replacement are streamlined; all components are integrated into one unit with a unique part number. Units in the series include: ELGS-BS ball screw, ELGS-TB toothed belt axis, EGSS mini slide, EPCS electric cylinder, EPCE compact electric cylinder, ERMS rotary drive, and ELGE toothed belt axis.
Festo applied 50 years of experience with simple motion based on pneumatics and applied it to electric motion for an equivalent level of ease of use. SMS opens the door to creative new solutions that benefit from the flexibility of low-cost and easy-to-commission electric motion.
Both Digital I/O (DIO) and IO-Link control come standard with each unit. With DIO control, there are two positions available – home and a configurable end point. As stated above, IO-Link offers flexible positioning along the axis, like a traditional electromechanical axis.
PLC set up for DIO control is identical to programing a digital pneumatic valve with two digital outputs and two digital inputs. One digital output extends the axis and the other retracts it. And the digital inputs indicate when the axis has reached the extended position or the retracted position, just like proximity switches would function on a pneumatic actuator. This similarity to a pneumatic valve simplifies PLC programing, reduces the number of I/O often required for servo-controlled motion, and speeds up installation of single and multiple units. Integrated position feedback eliminates the need for proximity sensors.
Since the electronic components and modules are onboard the integrated drive, these actuators are machine mountable. There is no external servo drive to mount in the control panel, which means minimal control panel overhead associated with these electric drives.
Festo wanted to maintain the similarity between simple electric motion and pneumatics, so software is not required for teaching movement. Commissioning is based on pushbuttons located on the drive.
Key commissioning parameters include:
- Speed for the extend (“out”) and retract (“in”) movement
- Force of the axis in the “out” position
- Setting the reference end position
- Teaching the position for the start of force-controlled movement
- Demo mode, which can be used to test the movements from the keypad.
The SMS axes offer motion characteristics that simplify commissioning for gentle cushion retraction, press-fitting, and clamping functions. Simple electrical connection is accomplished via a M12 plug design with 4-pin power and 8-pin logic.
With this new series of electric actuators, engineers can choose between pneumatic or electric actuation for a machine and have a basic equivalency for cost and installation overhead. Each type of actuation offers its own motion and force profiles, as well as other operational factors, giving engineers a broader set of solutions to apply to machine design challenges. For simple linear and rotary motion applications, the Simplified Motion Series axes represent an important opportunity for original equipment manufacturers.
Solution for nitrogen dosing on filling lines
A new Festo solution to help with nitrogen dosing on packaging filling lines is based on the Festo Motion Terminal and apps for multi-channel flow control and selectable pressure.
Two Festo apps, when used in combination, improve the efficiency, flexibility, and energy savings of nitrogen gas dosing on filling lines. These and other apps for the intelligent Motion Terminal provide machine builders with the ability to shorten time to market, reduce components and develop distinctive designs for customers.
The Flow Control Motion App enables nitrogen flushing on up to eight containers simultaneously through four valves. The flow rate, up to 600 l/min, ensures rapid dosing. The system detects percentage deviation from the specified volume, which creates the opportunity for fine tuning to achieve greater precision. Exact filling decreases nitrogen consumption.
The Selectable Pressure Level app moves multiple filling nozzles through the dosing process accurately. Flexible parameterization shortens cycle time. After filling, the nozzles are retracted from the containers with reduced pressure to save energy. A third app, Leakage Diagnostic, ensures the system is operating at peak sustainability through early detection of compressed gas or air leakages.
The Motion Terminal is an intelligent valve that changes functionality based on downloadable apps. Machine developers can create a basic machine type using the Motion Terminal and then select the relevant Motion Apps to equip it with various functions and features per customer requirements. The ability to copy and transfer parameter sets makes planning easier and shortens time to market. Assigning functions via software has the added benefits of preventing tampering and protecting intellectual property.
Ethernet-Based Festo CPX-AP-I Decentralized I/O
Expanded capabilities for the Festo decentralized I/O solution gives remote I/O designs greater capabilities. For instance, on long conveyor systems, decentralized I/O moves valves closer to cylinders for improved performance.
Festo CPX-AP-I enables expanded capabilities to be incorporated cost-effectively to packaging machines and long-length conveying systems without the expense and time associated with extensive wiring and installing control cabinets.
CPX-AP-I decentralized I/O is an Ethernet-based system consisting of intelligent bus nodes rated IP65/IP67 for versatility in mounting outside of a control panel. CPX-AP-I decentralized I/O bus nodes are compatible with the major communication protocols and offer simple integration into the controller of choice via EtherNet/IP (from ODVA), Profinet and Profibus (from PI North America), EtherCAT (from EtherCAT Technology Group), and ModbusTCP (from the Modbus Organization).
CPX-AP-I makes it easy to apply IO-Link enabled intelligent devices for fast and simple installation, improved control, and enhanced system diagnostics. CPX-AP-I increases the performance of pneumatic systems by moving valves closer to actuators on large-scale systems.
During the past 20 years, Festo advancements in electronics have transformed pneumatics allowing faster cycle times, greater capabilities, and diagnostics. Among Festo’s more important recent electronic advancements in pneumatics has been CPX-AP-I decentralized I/O. CPX-AP-I builds on the benefits of remote I/O. Communication and voltage supply come from two separate connection cables that enable the creation of voltage zones. Because CPX-AP-I is based on Ethernet, data bandwidth and speed exceed remote I/O.
CPX-AP-I features:
- 2 Kbyte I/O process data
- More than 80 modules per bus node
- Parallel data processing of real-time and non-real-time data
- Bus cycle times < 250µs for rapid production processes
- Enhanced diagnostics and condition monitorin
CPX-AP-I I/O topology example
The topology image illustrates the range of solutions of CPX-AP-I. The upper left shows the IP65/IP67 Ethernet-based decentralized I/O bus nodes connected to the controller of choice. In the center, there is a daisy-chain branch of digital and analog input blocks, valve manifold, and IO-Link master module with IO-Link enabled sensors. At lower left, a valve terminal starts a second decentralized branch, which includes another valve manifold and digital and analog input blocks.
Each CPX-AP-I system can accommodate more than 80 digital and analog input blocks, valve manifolds, and IO-Link master modules per system, with cable lengths up to 50 meters between modules.
Because of the extended distances available between modules, CPX-AP-I is ideal for large scale material handling, packaging, and processing systems where moving valves closer to actuators is essential for reducing cycle time. For example, moving a valve with 8 mm tubing from 4 meters to 2 meters away from the cylinder reduces pressurization time from 40 milliseconds to 20 milliseconds – a 2 times improvement in performance.
CPX-AP-I comes standard with Integrated IO-Link master and IO-Link device tools that allow intelligent sensors to be added to the systems. As the technology matures, additional solutions will include the incorporation of vision systems and pressure and flow sensors within the CPX-AP-I architecture.
Plug-and-play capabilities support Industry 4.0 concepts of modularity and fast, simple, and cost-effective reconfiguration and reuse of assets. With IIoT gateways and data contextualization, end users can employ dashboards for anytime/anywhere real-time analysis, troubleshooting, and predictive analytics.
CPX-AP-I decentralized I/O represents the latest development in lowering the cost of remote I/O while obtaining the increased benefits of faster and easier installation, greater system capabilities, and improved performance.
– Edited by Mark T. Hoske, content manager, Control Engineering, CFE Media, [email protected].
KEYWORDS: Pneumatic motion control, electric motion control
CONSIDER THIS
Is it time to refresh machine design with updated motion controls?
ONLINE
Mechatronics and Motion Control
https://www.festo.us
ODVA | Industrial Automation | Technologies and Standards
PI North America – The leader in Industrial Ethernet & Fieldbus
EtherCAT Technology Group | HOME
Online extra
More about Festo: Festo is a leading manufacturer of pneumatic and electromechanical systems, components, and controls for process and industrial automation. For more than 40 years, Festo Corp. has increased the state of manufacturing with innovations and optimized motion control solutions that deliver higher performing, more profitable automated manufacturing and processing equipment.