Reliable flow control equipment plays an essential part in the control of many manufacturing and industrial processes.
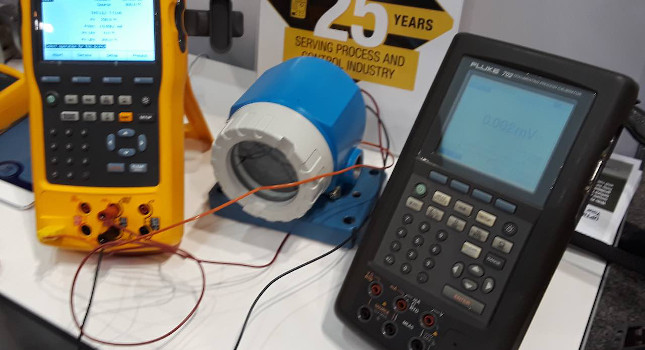
When managing a liquid, gas or powder process, flow control equipment, such as actuators and instrumentation, are vital. Pneumatic actuators have long been an integral part of actuation solutions.
Low emission instrumentation
Valve actuators are designed to automatically and remotely control valves. They can be pneumatically, hydraulically or electrically powered. Pneumatic actuators are well suited for use in critical high-speed fail-safe or emergency shutdown (ESD) duties in extreme or hazardous locations. There are also many instruments that are powered pneumatically that can be used as part of a smart, efficient and reliable flow control system, solenoid valves, controllers, positioners and regulators.
Low emission pneumatic controllers and an overall carbon footprint reduction are increasingly important requirement for electro-pneumatic control systems. Natural gas is an abundant pressure source, so this gas is often used as the supply for pneumatic instruments. It is normal for pneumatic devices to bleed some natural gas into the atmosphere, but the allowable emission levels of natural gas from controllers is highly regulated. The bleed rate or emissions level will mostly depend on the design of the device used.
Leonardo Ongetta, product manager: limit switch boxes and positioners at Rotork, said: “Pneumatic flow control equipment and associated instrumentation can emit fugitive emission, so there is an increased focus within the industry on efficient and innovative equipment that can reduce this as much as possible. Low emission instruments that assist in efficient use of pneumatic flow control are becoming increasingly popular.”
Valve positioners
Valve positioners play a key role within process control applications to control the position of a modulating valve. They are especially useful in process control applications thanks to their precision. They enable a rapid response to position the valve when a command signal is received from a control system. When a control signal is different from the actuator’s position, the positioner changes the actuator to the correct position.
Valve positioners are usually mounted on the yoke or top casing of a pneumatic actuator for linear control valves or on top of the actuator for rotary control valves. Positioners can be pneumatic or electro-pneumatic. Some have ‘smart’ digital technology with additional capabilities such as diagnostic, auto calibration and tuning functionality as well as connection to a current loop network.
Smart positioners
Pneumatic positioners receive pneumatic signals – usually 3-15 psig – from a control system. The positioner then supplies the valve actuator with the correct air pressure to move the valve to the required position. As they don’t have any electrical source, they are considered a fully mechanical-pneumatic device, following specific simplified regulations for hazardous area applications. Electro-pneumatic positioners convert current control signals to equivalent pneumatic signals.
Digital/smart positioners use a microprocessor to position the valve actuator, while monitoring and recording data. They are accurate and allow for online digital diagnostics. Pneumatic smart positioners employ continuous monitoring and graphic display of valve position and set point target over time within linear and rotary applications. A smart positioner like this can be used for both control and on/off valve applications and is suited to use in critical applications in chemical/petrochemical processes. The steady state deviation analysis that smart positioners of this type provide can detect friction in the valve or actuator, leakage in pneumatics and instances where there is insufficient supply pressure, helping to prevent inefficient usage and excess gas emissions through leakages.
“A digital smart positioner is well suited to pneumatic valve systems for linear and rotary applications, as it provides precise control as well as enhanced diagnostics, detecting friction in the valve or actuator, leakage in the pneumatic supply and insufficient supply pressure,” Ongetta said. “They constantly check the integrity of the system, raising alarms if something is out of specification. Additionally, with online and offline automated testing procedures, the user can evaluate valve package health and compare with commissioning data.”
Controllers
Controllers act in a similar way to a conventional positioner but control different final pneumatic elements. They are an essential component in the control of electro-hydraulic and pneumatic valve actuators.
I/P converter
I/P (electric current to pressure) converters are a key control interface for many natural gas applications, such as large compressor skids. Low emission I/P convertors convert electrical signals into accurate, stable and repeatable pneumatic pressure for equipment such as an actuator. Controllers like this maximize efficiency and control all pneumatic components on a site in an effective and reliable way. They usually receive an analogue input signal of 4 to 20 mA delivered from the controller.
Conclusion
Reliable flow control instrumentation plays an essential role in many industries, such as pharmaceutical, oil and gas, power, water and chemical applications. Many of these instrumentation systems are pneumatically powered. This is largely because natural gas is often used in the application and is therefore easily available. Excess fugitive emissions that can be associated with using natural gas can be managed through innovation in the design of efficient pneumatic instruments. Such designs include low emission I/P convertors and digital smart positioners.
This article originally appeared on Control Engineering Europe’s website.