Motor drive advice was offered in a write-in question in the Control Engineering motor drive research, summarized in the September issue.
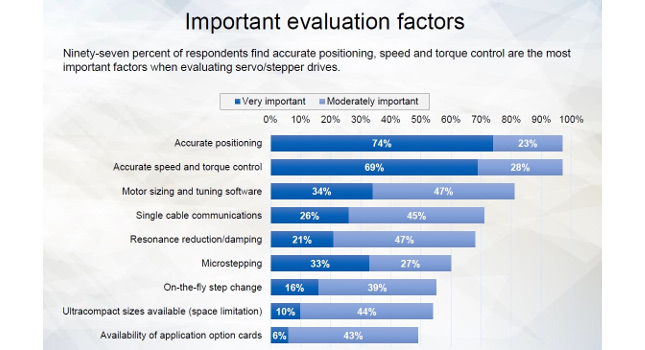
The 2019 Control Engineering Motor Drives study from Control Engineering, asked respondents, “Based on your experiences and knowledge, what’s the best advice you can offer?” Some of the responses follow, lightly edited for style.
Drive application advice
Applications are critical to reliability and the selection of wiring type and input and output filters.
Check for temperature rise on motor, how harmonic contents spread into the grid, and the overall efficiency at partial load.
It doesn’t matter which brand of drives you choose for your application. Most important are quality of the product, availability, and standardization. Standardization is a big one because it can reduce the stock of spare required and helps support personnel understand the drives used.
Know the specific details of your applications requirements before specifying the drive. For example, know peak velocity usage, not just average velocity. Similarly, know the maximum torque that the application demands. Consider all of this with the motor’s performance in light of the specific drive to be used. Failing to do the pencil-work prior to specifying the drive is almost a guarantee of disappointing performance later on.
Know your application before selecting a drive.
Limit the number of drive suppliers so that you can ensure supportability and the ability of in-house staff to service drives.
Make sure motor is matched to the application and motor drive. Beware of application limitations due to long cable lengths to the motor.
Make sure that the motor/drive selection works well with the PLC controls being used.
No universal drive: be specific on which application you would use it and select accordingly for your best performance and cost effectiveness.
Prepare for dirty power.
Read the spec and test to verify.
Correct drive sizing
As efficiency standards change for induction motors, watch for inrush currents and breakdown torque and breakdown current changes. Inrush currents are rising and can cause challenges with electronic overloads. Know your application, particularly high friction and/or high inertia starting. To get the full use of your available motor torque, the drive must be correctly sized. For very large motors performing heavy-duty cycle work, be certain that the transformer and conductors do not cause large voltage drops when the application is at its greatest demand. For large hammer mills using wound rotor motors and liquid rheostats, we target <5% Voltage drop at the motor at 200% full load amps (FLA). It’s very common for engineers unfamiliar with the application to undersize the transformers and conductors.
Choose the right drive for the motor for optimum performance.
Do the design work up front, such as motor sizing, because it is easier and faster to take the time upfront than to guess and then have to replace a motor or drive later.
They should always be specified to be of the high-efficiency type and be loaded at 70% or higher during normal operations.
Products, parts, support
Replacement parts need to be available.
Be open to new products.
Buy from someone with good technical knowledge and a lot of hands-on experience. Hire and kept good technical support people on staff.
Check compatibility before ordering, if you’re not using similar products.
Check your local supply chain for products before committing to them. There are plenty of vendors out there so don’t be fooled by the sales pitch. If you can’t get the product, or replacement, in a timely manner, then it isn’t worth the money you might save at the outset.
Don’t make assumptions. Do your homework, and don’t be afraid to ask a real person whether something is doable or not.
Don’t pay extra for factory start-up if you have a knowledgeable tech in-house. Factory techs sent to start-ups I’ve participated in have ranged from only marginally knowledgeable to completely unqualified. Not worth it.
Double-check specs and requirements for motor and drive selection.
Drive pricing, quality
Buy the best you can afford. Keep your equipment in good shape. Know that all machines will break down at some point (mostly at the worst possible time).
Cheap stuff usually doesn’t work well, breaks down easily, and/or has bad technical support.
Do not get hung up in all of the bells and whistles. Most settings will remain factory default, and work fine.
Investigate total cost of ownership.
Lower cost is not always the best solution.
What is the cheapest?
You get the quality you pay for.
Design, maintenance, retrofit
Don’t think you can delay or skip preventive maintenance.
It is always nice to read drive manuals before installation.
Keep an open mind, standardize as much as possible, make sure you keep up with your manuals, and keep your schematics up to date for follow-up/replacement.
On retrofit or replacement, ensure the motor is capable (especially insulation). The drive should have predefined application parameter setups for easy start up, and a starting point for tweaking if required.
Pick a standard and standard set of parameters to make setup/replacement easy.
Specify correctly, understand the application well. Beta test prior to using. Understand the long-term cost of software used, such as the cost of renting software, cost of purchasing software and cost of being able to competently use software for commissioning, troubleshooting and repair.
Understand how all the different manufacturers’ drives are programmed. Find a drive that is easy to interface with. Work with drives where the manufacturer doesn’t charge to learn how to program their drive. Be able to do your own start up and not pay/rely on a “certified tech” to do all your programing and leave you in the dark if there is a problem, or removes the warranty if you do the start up.
When looking at drives, consider the customer support the company provides. When developing novel products, the drive vendor may be your best source for new designs.
General advice, support
Two principles have worked for me over the years. The first is to keep it simple. The second is the old adage that proper planning prevents poor performance. If you can keep these in mind you should be able to do most anything asked of you.
Make sure your selected vendor has accessible and knowledgeable support.
Most builders provide similar things in its products, but not all offer similar support to its products and to its users.
Pick a reputable brand, get to know it… then stick with it.
Research thoroughly before making a decision to purchase.
Reliability and simplicity are most important for me. I’m far too busy to try and learn a million options on every piece of equipment. Choose a reliable platform with a straightforward programming philosophy. I don’t need a programmable logic controller (PLC) in a drive. I already have a short list of PLCs I’m familiar with, and if I need to control something small, I will choose a small PLC I already know and trust to marry with the drive.
See what company is authoring the articles.
Servos are good, but steppers make small position moves better in many cases. Variable frequency drives (VFDs) have come a long way and can replace servos in some application, but if you want to go fast with good control, nothing beats a servo.
Standardize as much as is practical.
The simpler the better.
Use a highly regarded brand, and off the shelf is usually best.
Survey managed and data compiled by Amanda Pelliccione, CFE Media and Technology research director. Edited by Mark T. Hoske, content manager, Control Engineering, CFE Media, [email protected].
KEYWORDS: Motor drives, servo drives, variable speed drives, medium voltage drives
Motor drive survey respondents provide advice.
Lowest price might not be lowest lifecycle cost for a drive.
Filtering and harmonics are important.
CONSIDER THIS
Is it time to upgrade motor drives or install additional drives to save energy and reduce motor wear?