Reduce or eliminate unnecessary cables through pluggable I/O terminals and one-cable strategies in control cabinets and machines.
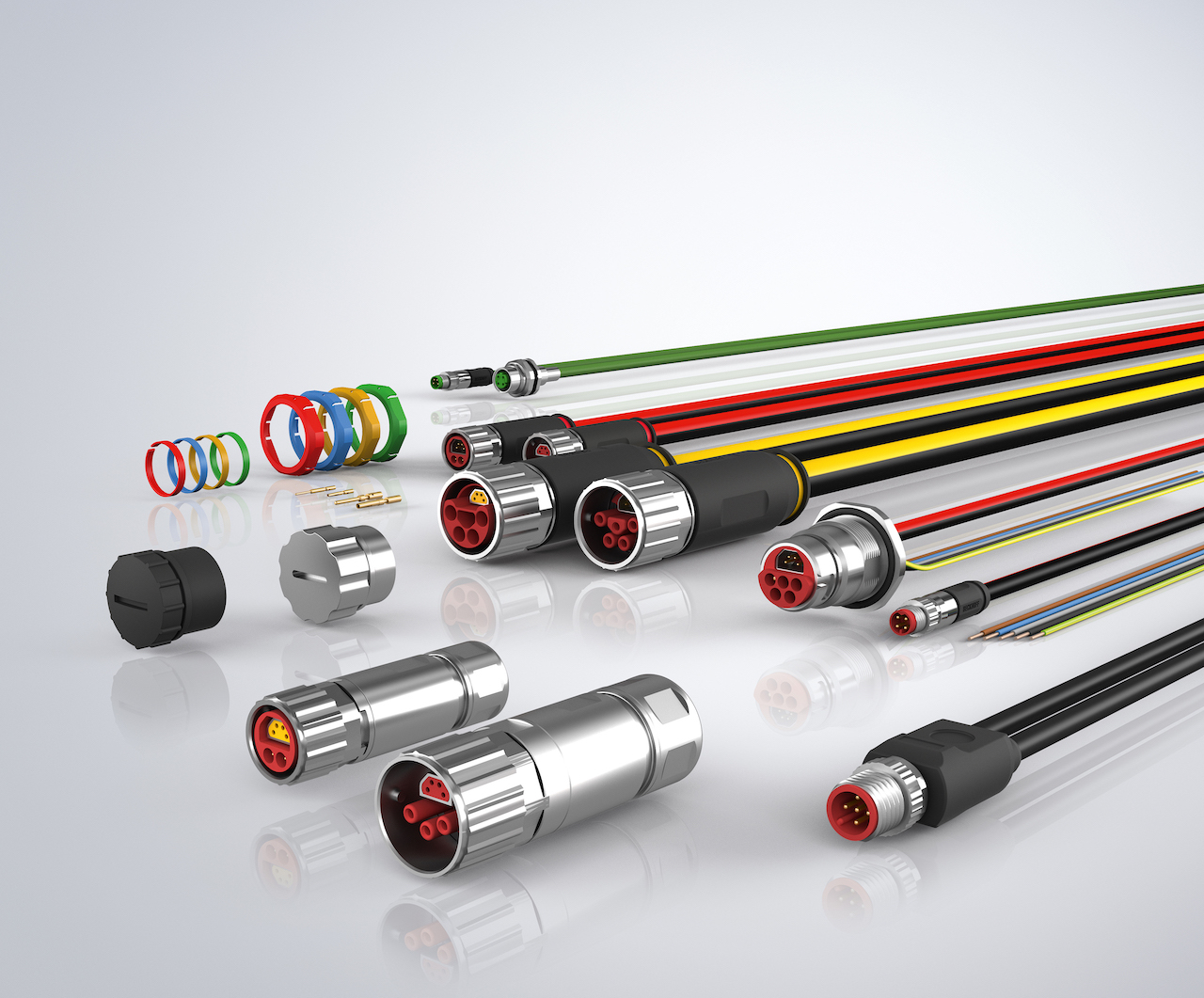
When designing a new machine or retrofitting a legacy system, cable management is typically an afterthought. It’s possible to bundle wires and add a conduit to keep them in place, but ignoring the effects of required cabling until the end of the design process increases expenses and overall equipment footprint. Engineers will likely spend more time wiring a system during the commissioning phase, tracing wires during troubleshooting, and adding costs by not having the correct cable lengths.
Assessing the impact of cabling before commissioning provides significant benefits beyond creating better-organized enclosures and a cleaner plant floor. Strategic cable management planning in the design phase can result in a cleaner system that reduces cable count and eliminates potential errors and points of failure.
The most effective cable management strategy starts with selecting intelligent components. Engineers should implement input/output (I/O) terminals, fieldbus systems, motion control devices, and other machine components that minimize cabling requirements in the application.
Reducing cable requirements
It is important to remember that most cabling in factory settings provides either power or networking signals. Although these are not minor tasks, having a tangle of wires connecting sensors, control cabinets, and other equipment isn’t necessary.
Figure 3: EtherCAT P provides uses one-cable technology (OCT) to communicate with provide power to EtherCAT box I/O in the field. Courtesy: Beckhoff Automation[/caption]
When attempting to improve a system’s cable management, it is important to identify the available fieldbuses and individual components that require fewer cables to get the job done. Engineers should first consider fieldbus and I/O systems and give preference to those that provide flexibility in topology and eliminate switches.
The EtherCAT industrial Ethernet system offers flexibility in topology without using additional nodes. EtherCAT also integrates a wide range of third-party devices, from drives to I/O and field devices, and shares data to the main controller. Also, gathering data from legacy devices on other protocols without running cables back to the controller is easy to accomplish over EtherCAT. System-integrated hardware and software gateways can bring data from all manner of fieldbuses and industrial Ethernet systems into the EtherCAT network.
Choosing a fieldbus based on these concerns is the first step, but the network provides the best results when paired with cable-reducing components. One-cable technology (OCT) and pluggable I/O terminals are two important pieces.
Providing power and data with one-cable technology
While it may be difficult to eliminate all cables in the field, it is possible to significantly reduce the number of cables; OCT provides an important tool to accomplish this.
Various products have been introduced over the years to provide power and a signal through one cable. Power over Ethernet (PoE) has been an IEE 802.3-IEEE Standard for Ethernet standard since 2003, and the technology has been used in industrial applications. Other cable types combine power with USB 2.0 and a DVI signal for human-machine interface (HMI) hardware. There are also types that provide power and feedback from servo drives to servomotors or directly from the control cabinet or a distribution module to servomotors with integrated drives. Because these cables can span up to 100 m, they must offer a rugged wire jacket to ensure they withstand wear and tear in industrial environments and reduce the chance of damage and potential points of failure.
For example, EtherCAT + Power (EtherCAT P) can supply power to applications from 24 to 400 V ac or 600 V dc and carry currents up to 64 amps, as well as provide two voltages for both EtherCAT slaves and connected sensors or actuators. In this case, the two voltages—US for system and sensor supply and UP for peripheral voltage for actuators—are electrically isolated from each other and can each supply up to 3 amps to connected components.
Streamlined motion architectures, such as distributed servo drive systems, can be daisy-chained, but may require a separate distribution module. However, some distribution modules can supply a signal from the control cabinet to as many as five drives. EtherCAT I/O modules with an IP67 rating can be installed outside the enclosure and closer to the machine, so the cable run is confined to a smaller area while providing signal and power for multiple EtherCAT P slaves.
EtherCAT P (EtherCAT Ethernet communications with power, ECP) technology supports multiple connector families, including ECP (EtherCAT with integrated 24Â VÂ dc power supply) and ENP (EtherCAT Ethernet with no power, ENP, without integrated 24 V dc power supply). The designs are very similar with a trapezoidal power core element for the power supply and several points for a signal. ECP cables work in EtherCAT environments with high voltage demands. ENP cables work with any Ethernet-based protocol, such as EtherNet/IP or Profinet, as an open solution. Both types reduce cabling efforts when used with components powered through OCT.
Pluggable I/O terminals reduce cabling in cabinets
Beyond eliminating cables and switches in the field, simplifying the control cabinet cabling also promotes a cleaner system with fewer points of failure. When numerous I/O points are involved, cabinets become crowded, which complicates wiring and increases the likelihood of errors. A wireless I/O terminal that plugs directly into the signal distribution board is an important advancement.
Using prefabricated cables with application-specific plug connectors and power and control signals are distributed from the routing circuit board to the plug-in terminals. The approach offers an especially good return on investment (ROI) for production machinery integrated in series. This method is designed to eliminate point-to-point wiring within cabinets through a compact, application-specific electromechanical design. By embedding the I/O system into the machinery, machine builders and end user manufacturers also minimize cable management efforts, labor costs, and potential wiring errors.
These pluggable terminals are often more compact than DIN rail-mounted I/O—as much as 50% smaller in some cases. Combined with the wiring reductions, this makes reduced equipment footprint an additional benefit of the plug-in terminal approach.
This demonstrates how effective fieldbus and I/O technology can mitigate cable management concerns in electrical enclosures. However, circuit board-based I/O systems are best suited for new installations rather than retrofits. Reducing cables in the field via OCT is just as amenable to brownfield and greenfield applications.
Smart cable management and smart machine design
Innovative networking technologies eliminate extraneous cables. By considering these factors during the early phases of a retrofit or new machine design, engineers are far less likely to face cable management issues later on. Many of these cable-reducing strategies are still emerging technologies. While they already offer numerous benefits, their capabilities will increase as the technologies mature.
Plug-in I/O terminals and one-cable solutions empower engineers to build control cabinets with drastically reduced cabling and to design fieldbus architectures with power and data in single-cable runs.
The automation industry is quickly churning out streamlined products for each step in the engineering design and implementation processes. Cable management should not be an area that gets tangled up in hindsight.
Sree Potluri is an I/O application specialist at Beckhoff Automation. Edited by Emily Guenther, associate content manager, Control Engineering, CFE Media, [email protected]