Advantages of industrial software are explained at the 2023 Aveva China User Conference, including more effective digital transformation, data management and analytics and use of artificial intelligence, among other future benefits.
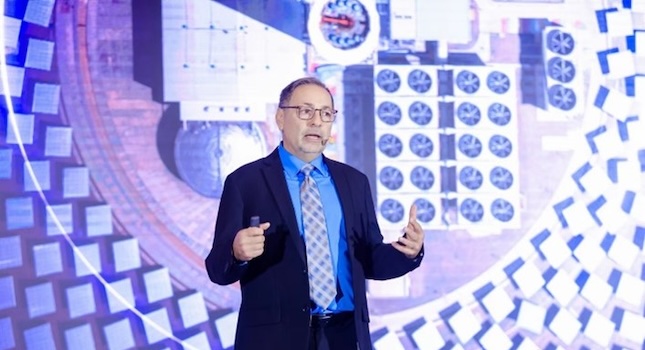
Learning Objectives
- Understand the challenge and benefits of industrial digitalization and how to more effectively manage engineering and operational data.
- Learn three benefits of implementing digital enterprises with full lifecycle digital twins.
- Embrace AI to lead the innovative development of industrial software.
Aveva China User Conference insights
- Challenges remain but benefits of industrial digitalization are strong. Open industrial software helps to more effectively manage engineering and operational data.
- Implementing digital enterprises with full lifecycle digital twins can result in 10% profitability improvement, 300% return on investment and 20% energy efficiency improvement.
- AI improves innovative development and implementation of industrial software, including 10 to 20 times improvement in training efficiency.
Industrial software, as an encapsulated product of industrial technology and knowledge programming, is said to be the soul of industrial digital transformation. Future industries will be structured on a wide variety of industrial software to help 1) digital transformation, 2) data analytics and 3) industrial artificial intelligence (AI). In the global industrial software marketplace, an industrial software company named Aveva has gathered many resources. In January 2023, Schneider Electric completed the 100% acquisition of Aveva, and Aveva became a leading global industrial software company worth more than $10 billion, the company said.
Challenge and benefits of industrial digitalization
During the 2023 Aveva China User Conference, the industrial software giant’s strong industry influence and industry-leading product and technology strength provided a clearer understanding of the future development of industrial software.
Although the digital transformation has been proposed for nearly a decade, enterprise digital transformation still faces heavy challenges: 70% of the world’s industrial enterprises in the digital transformation encountered failure. However, rewards of successful digital transformation can bring:
-
10% profitability improvement
-
300% return on investment
-
20% energy efficiency improvement.
More effective management of engineering and operational data
How can we ensure that enterprises successfully realize digital transformation?
Harpreet Gulati, senior vice president and the head of global information management business at Aveva, said, “Based on the Aveva Connect open platform, which enables effective management of engineering data and operational data, Aveva can establish digital twin models covering the entire life cycle and comprehensive visualization and analysis for industrial enterprises applications.” Gulati said the platform supports Aveva applications and third-party applications and can help users leapfrog “from digital twins to digital enterprises through the establishment of cooperation across the industrial chain.”
The new paradigm of industrial intelligence mentioned by Gulati refers to the use of digital twins across the plant lifecycle, including engineering design, production operations, and performance optimization, to unify and integrate the engineering data of the asset lifecycle (also known as static data), and the real data generated by the plant’s production and operation (also known as kinetic data), into an open platform. The virtual factory can be created by integrating the engineering data of the entire asset lifecycle (static data) and the real data generated by the production operation of the factory (dynamic data), into an open platform to create a virtual factory corresponding to the real factory in real time.
Implementing digital enterprises with full lifecycle digital twins: Three benefits
The benefits of digital twins throughout the entire lifecycle are self-evident.
-
It breaks down the information and process silos in industrial enterprises, and connects departments of differentsystems through a complete and unified digital process.
-
By transmitting engineering design data through digital twins to the factory operation end, real-time operational production data can be combined to continuously optimize operations, share information and insights, support customer scientific decision-making, tap into data value, and improve engineering and operational efficiency.
-
The factory digital twin system also provides data and architecture support for the mutual call between engineering data and real-time data, data governance and visualization, equipment early warning monitoring and predictive maintenance, mechanism model construction, big data analysis and other areas.
The digital twin of Aveva’s entire lifecycle is built on the “dual database,” which is the engineering asset data base, which is the steady-state design parameters and other data of equipment on the engineering design end, and the production and operation data base, which is real-time data from various production links, layers and systems. The data dual base is implemented by Aveva Asset Information Management (AIM) and Operations Information Management (OIM), also known as PI System.
Gulati said Aveva can provide a full lifecycle digital twin different from other industrial software companies because after more than 50 years of development, continuous acquisition and integration, Aveva has formed a digital product portfolio covering the lifecycle of factories. The software products from factory design and construction, transfer to operation and optimization enable Aveva to become a seamless integrated platform through internal integration, Gulati suggested, allowing data to flow and generate value, to achieve digital transformation.
Embrace AI to lead the innovative development of industrial software
In a survey conducted by Aveva, engineers in factories spend up to 40% of time searching for data, and if generative AIcan be used to complete the search, it can save 10% to 15% of the time, which will be a significant improvement in work efficiency. Gulati stated that Aveva is currently actively embracing AI technology, including the latest generative AI technology, which will be a disruptive technology in future industrial software.
“When we apply generative AI, we must be very careful with these technologies and ensure the security of customer data, which will not leak into the OpenAI model,” he added.
In addition to generative AI, currently more AI applications are based on machine learning for predictive maintenance and reinforcement learning for AI autonomous operations. Aveva has mature solutions in both areas. For example, in a successful case in Japan, the automation control of a common distillation tower in the chemical industry uses AI for autonomous production control of the distillation tower.
For Aveva, using AI technology has natural advantages. Gulati believes that the complete product portfolio of Aveva can help enterprises create digital twins throughout the entire lifecycle. Therefore, virtual digital twin factories can be used in a closed-loop and secure environment to provide massive operational data for artificial intelligence models for reinforcement learning training. This mode can ensure the provision of accurate real-time data without interfering with the production control of real factories. Moreover, since it is in a virtual environment, it can train multiple models simultaneously and even accelerate time, greatly improving training efficiency with a speed of 10 or 20 times, ultimately obtaining an AI model that can do practical work well.
“We will usher in a wave of technological revolution, such as the current AI industry,” Gulati said. “However, the manufacturing industry itself is a highly fault-tolerant industry, and its development is generally progressive. Therefore, Aveva will actively embrace these new technologies and accelerate the pace of industrial enterprises’ application of new technologies with safe, mature and reliable solutions.”
Stone Shi is executive editor-in-chief, Control Engineering China; Edited by Mark T. Hoske, content manager, Control Engineering, CFE Media and Technology, [email protected].
KEYWORDS
Open industrial software, digitalization, industrial AI
CONSIDER THIS
Is open industrial software helping you with digitalization, analytics and AI use?
ONLINE
www.controleng.com/international
https://www.controleng.com/digital-transformation/