Technology advances such as light detection and ranging (LiDAR) are allowing drones to go to dangerous environments they couldn’t before without the need for GPS.
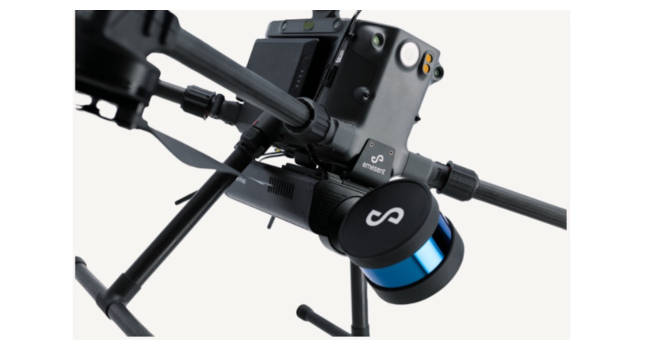
Learning Objectives
- Drone technology has expanded and they are being used in environments that are dangerous for humans.
- Light detection and ranging (LiDAR) data helps create accurate 3D point clouds and also provides advanced autonomy capabilities./li>
- Technology advances can let drone pilots navigate a dangerous area such as a mine through a tablet.
Drone inspection and mapping technology has expanded in the past decade with the advancement of lightweight batteries, drone flight controls, autonomous navigation and high-resolution digital cameras. Inspection applications have grown rapidly in agriculture, oil & gas, building and bridge construction, electric utility vegetation management, fire and rescue, surveying and many other inspection tasks. GPS-guided drones using digital cameras have created new service markets for many inspection and surveying tasks that were impossible to accomplish with other methods.
Empowering drones with autonomous navigation has greatly improved the ability to collect useful data and reduce the need for, and costs associated with, skilled pilots. Most of us take GPS for granted today when traveling by car or even hiking in the mountains. GPS is an integral part of many drone surveying and inspection activities. However, there are some environments like mines, warehouses, tanks, underneath bridges and other covered spaces where GPS is not available or reliable. To address this challenge, Emesent has developed proprietary LiDAR-based drone autonomy technology that can survey and inspect previously inaccessible spaces or assets.
A traditional drone survey refers to the use of a drone, or unmanned aerial vehicle (UAV), to capture aerial data with downward-facing sensors, such as RGB or multispectral cameras and light detecting and ranging (LiDAR) payloads. During a drone survey with an RGB camera, the ground is photographed several times from different angles, and each image is tagged with coordinates. 2D and 3D maps can be created using GPS and photometric techniques.
The Emesent Hovermap solution is LiDAR-based and does not require GPS. Instead, it uses a simultaneous localization and mapping (SLAM) algorithm to estimate the drone’s position and orientation from the LiDAR data itself and create high-detail, accurate 3D point clouds and also provides advanced autonomy capabilities. It allows the drone to fly autonomously, self-navigating around obstacles even in GPS-denied environments and beyond line-of-sight and communication range.
This lets the drone be used for mapping in underground mines, underneath bridges or platforms, tanks, and other covered spaces; the modular camera can be removed from the drone and mounted to a ground robot or used for walking scans.
Measurement technology adds data that can’t be gathered from a camera
The basic idea is to measure and regulate key variables when controlling a process. When new technology allows you to measure important variables, there is an opportunity to improve the control of that process. With accurate 3D point clouds from the new high precision lightweight LiDAR, models can be produced to provide great insights into both surface and subsurface mining, structures like industrial processes, warehouses, buildings, bridges, tunnels and subways.
Hovermap’s rotating LiDAR provides an omni-directional field of view, ensuring 3D data is collected in all directions. These maps are useful for review of erosion, tree measurements, and stockpile volumes. The acquired data can be combined with data from additional sensors, such as cameras or hyperspectral imaging for further data analytics.
One of the possibilities for autonomy is flying drones below the forest canopy for accurate growth assessment. This is useful to cover large areas of new plantings without trudging miles or fear of GPS interruptions.
Partnering with mine planning software providers
Emesent’s ambition to help mining customers boost productivity and improve outputs has led to alliances with major mine planning software vendors. These alliances make it easier for mining companies to adopt new data capture technology by leveraging existing surveying capability. Through seamless import of Hovermap scans into these platforms, users are able to use the data for geotechnical analysis and condition monitoring, as-built surveys, volume reporting and design updates.
Data from previously inaccessible areas is bringing new insights and an additional level of detail to mine operations. Partnering with key technology providers in the vanguard is helping make a digitally-driven mining ecosystem a reality.
Keeping workers away from danger
Underground mines contain large open voids that are critical to the efficient and safe operation of the mine. These unsupported voids are a source of ground falls that can endanger personnel, underground infrastructure, and equipment. The traditional method of scanning an open void is for a surveyor to operate a boom-mounted LiDAR sensor near the edge of the void, which is time-consuming, produces poor quality, shadowed, incomplete scans and endangers personnel.
Hovermap pilots can fly an entire mission, from take-off to landing, using only a tablet. Data is processed on-board in real-time to stream a 3D map back to the operator. Tapping on the map will set smart waypoints, and Hovermap takes care of the rest, navigating to the waypoints while avoiding obstacles and completing the mission autonomously.
Drone technology advances make humans safer
New market segments have developed as drones coupled with a variety of sensors have fed a seemingly insatiable demand for fast, easy access to detailed asset information. Drones can provide quality images and improve the operation of agriculture, building and bridge construction, offshore platforms, pipelines, transmission lines, disaster response and many other industries.
Drone technology continues to improve the capture of useful data with the advancement of LiDAR. The SLAM-based autonomy now provides the ability to operate in GPS-denied environments using lightweight precision LiDAR carried by a drone. This autonomous capability means LiDAR can operate in previously unmapped dark, confined spaces like mines with minimal human involvement. This ability can improve mine operations and gather valuable data without putting humans into hostile environments or work on dangerous tasks.
Rick Rys is a senior consultant at ARC Advisory Group, a CFE Media and Technology content partner. Edited by Chris Vavra, web content manager, Control Engineering, CFE Media and Technology, [email protected].
MORE ANSWERS
Keywords: machine vision, drone mapping, LiDAR
CONSIDER THIS
What benefits could your facility gain from drone mapping?