Sulfate esterified cellulose nanofiber can be a biodegradable replacement for many materials, but its full potential is yet to be realized.
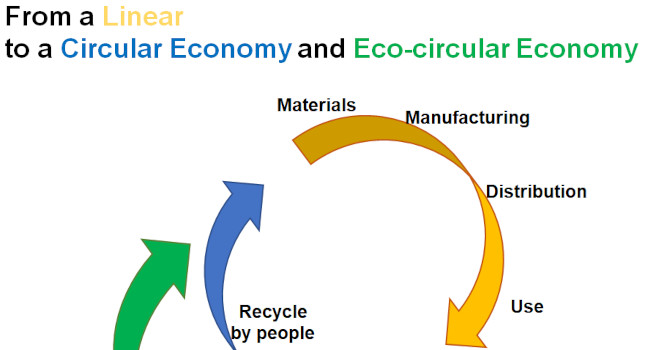
Products made from fossil fuel feed stocks are all around us: cosmetics, the ink in ballpoint pens, paints, films, plastics and many others. However, as the world sets its sights on decarbonization and seeks substitutes for non-renewable fossil fuels, attention is turning toward biomass materials for feedstocks, which is a renewable resource that can be cultivated in many countries around the world.
One biomass material, cellulose nanofiber (CNF) made mainly from wood pulp, is garnering heightened interest. In the process of creating wood pulp for paper manufacturing, wood is chemically pulled apart into fibers that are rearranged to create many products. Wood fibers, approximately 20 nanometers (nm)in width, are composed of smaller fibers, from 3 to 4nmin width. The smaller fibers are CNF, which can be made into a wide range of products. Since CNF is a nano-sized material, it exhibits interesting properties related to rheology, such as thixotropy, which means it becomes less viscous when subjected to an applied stress. This makes it very useful for ink or paint production.
CNF itself is five times stronger than steel, but has one-fifth its mass, so stronger resin can be formed when mixed with CNF. Its size and shape do not change when it is heated, making it suitable as a base material in electronic components and optical materials. When turned into sheets, it has excellent oxygen barrier properties, needed with many types of packaging materials. Moreover, biomass-derived CNF is expected to be biodegradable (Figure 1).
CNF is difficult to artificially synthesize and is mainly derived from plants, particularly forest waste resources. Since CNF provides various beneficial characteristics, it may prove to be fungible, allowing it to be applied in much the same way as general-purpose fillers. Sulfate esterified cellulose nanofiber (S-CNF)improves many characteristics of CNF, which is necessary for use in a wider variety of applications. (Figure 2)
In addition to having the same characteristics as standard CNF, in a gel form S-CNF can be dried to produce a powdered substance that has 1% of the volume and weight of the gel. This powder costs less to transport and store. Its physical properties can be restored by blending it with water. By adjusting the blending ratio, the physical properties can be altered to suit specific applications and handling requirements, such as fine-tuning thixotropic characteristics for applications where high-shear rates are necessary.
Research to production
S-CNF is available for use in the chemicals and materials industries.
Companies have shown a great interest in CNF because:
- It is amenable to material rheology control and demonstrates attractive thixotropic characteristics.
- It is a strong, lightweight, and highly transparent material that is resistant to deformation when exposed to heat.
- It provides an effective barrier against oxygen and other gases while enabling relative smoothness on its film surface.
- Its production and disposal have low environmental impact. An advanced process breaks down CNF and produces S-CNF while consuming less energy than other CNF production processes in part due to more moderate chemical processing conditions.
A solution for constrained resources
Much of the research on CNF is taking place in Japan, which has been dealing with material and energy constraints for centuries. Wood is one of the few materials Japan has domestically with some degree of abundance, so this development has appeal. Products made from wood also fit well into a circular economy where waste degrades easily and has no net increase of carbon release.
One of the researchers collaborating with Yokogawa Bio Frontier is Takuya Kitaoka, a professor in Kyushu University’s Graduate School of Bioresource and Bioenvironmental Sciences, and a specialist in tree-derived biomass materials. He believes industrial users are beginning to recognize the potential ways S-CNF can be applied as well as the positive environmental effects it can have.
“We must envision a world where, just like wood and paper, CNF is in regular use in many different ways,” Kitaoka said. “For example, the paper cartons and packets with internal aluminum linings that are used to hold soy milk, juice, soup, pasta sauce, and other such products could be replaced with packaging that is made entirely from biomass-based CNF, which, owing to its high oxygen barrier properties, would prevent contact with air and ensure freshness. These biodegradable and recyclable materials would have a small environmental impact. In addition, sulfated polysaccharides are substances that exist in abundance as biological matrices (fibrous connective tissue) between cells in our bodies, and they have bio-functionality. While we can’t say for certain yet, I think that S-CNF can be suitable for use in cosmetics and medical applications.”
Given the sustainability and environmental concerns growing within manufacturing today, the selection of materials must be evaluated on its aftereffects as well as its suitability for the immediate need.
Working within a carbon-neutral economy
“All around the world, people are talking about being carbon neutral and building a circular economy, but I believe that negative emissions and something that I call an ‘eco-circular economy’ will become keywords in the future (Figure 3),” Kitaoka said. “Being carbon neutral means there is no net release of CO2into the atmosphere, and this is accomplished by balancing emissions with the absorption and elimination of emissions. Reducing CO2means having negative emissions, and there will be no decrease at all unless more CO2is absorbed than is emitted.
without human assistance. Remains of the bottle will be metabolized by the next tree which will then be turned into additional CNF. Courtesy: Yokogawa Bio Frontier Inc.
“What makes this possible is ecological material science. In the Edo period in Japan (roughly 1603-1867), people made use of natural materials that could be circulated and recycled in the natural ecosystem. One example of this was the wrapping of items with bamboo leaves and paper-thin sheets of wood. Ecological material science is a modern version of this, exploring how the design of materials [can be] based on the idea that materials and energy can circulate and be recycled in the natural ecosystem. From the viewpoint of an eco-circular economy, I believe that the use of wood as a nanomaterial has wide-reaching potential,” Kitaoka said. As important as it is to find biodegradable replacements for plastic, this is only the beginning of the possible discoveries. Before long, creative companies will develop new products that take advantage of S-CNF’s unique characteristics, resulting in high value-added products that can only be manufactured from this material.
Dr. Mitsuhiro Iga is CEO of Yokogawa Bio Frontier Inc. Edited by Chris Vavra, web content manager, Control Engineering, CFE Media and Technology, [email protected].
MORE ANSWERS
Keywords: cellulose nanofiber (CNF), Sulfate esterified cellulose nanofiber (S-CNF)
Learn more about Yokogawa Bio Fronter Inc. https://www.yokogawa.com/ybf/
CONSIDER THIS
What benefits could your company gain from using CNF and S-CNF?