How sophisticated signal processing and advanced applications are expanding the measurement palette.
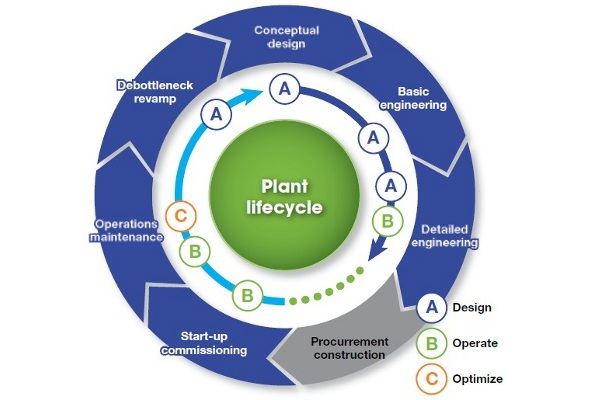
For more than 100 years, process instrumentation has provided the basic measurement of condition and physical properties that enables process control. We measure pressure to control pressure, and we measure temperature to control temperature. In the 1930s, when Foxboro engineers invented the d/p cell and added flow to the mix of process variables, the requirements changed significantly.
Measuring flow with the degree of precision needed for control requires a much more complete set of engineering data. In addition to temperature and pressure, we must also measure parameters like fluid properties, pipe diameter, pipe material, and temperature to determine the primary element of the measurement, the size of the orifice through which the liquid would pass, and all the wedges, elbows, venturis, or other components necessary to create measurable flow. And once we determine those components, to get the right product in the right application and build the model code, we still have to choose from four or five measurement devices and at least 20 different options. And we are not finished yet. We must also know how to install the devices to make them work, and must rely on rule-of-thumb information on impulse lines and snubbers or precise calculations for the installed effects of diaphragm seals. This knowledge base is necessary to build a plant that produces as expected. But what happened back at the design stage?
Plant designers typically begin with requirements to produce a specified amount of product. Looking at plant design from design/build-operate-optimize (DOO) plant lifecycle model (see graphic), at the design phase, we must determine which and how many product measurements will be needed to control the process and measure the quality at the operate stage. Most measurements will be of a process condition, but some of will measure the product directly. Designers will often reduce the number of measurements to save construction costs, thinking that the user can add them later, if needed, when the plant is operating.
This can work out fine if you are taking only simple condition and product measurements, but recent integrations of advanced process control technology and instrumentation—especially flow instrumentation—expand significantly the repertoire of strategic measurements that companies can implement. Ignoring these at the design phase can result in lost opportunity to improve processes and ultimately profitability.
In addition to simply supplying measurement of condition or physical properties, we now have a tremendous opportunity to glean much more information from our instruments. Why not, for example, have a distillation measurement? We could derive this by using advanced software to combine readings from all the sensors delivering condition and physical properties, drawing on the same modeling expertise that is used to design the plant. Such advanced measurements, as we call them, combine the functionality of advanced applications, state-of-the-art field devices, and process measurement methods. Expanded use of flowmeters in measuring HF alkylation, custody transfer, and net oil and gas illustrates a variety of ways in which we can extract new value from field instrumentation.
Safe, cost-effective measurements
HF alkylation monitoring is a good example of an advanced measurement that can have significant payoff. Hydrofluoric acid (HF) is a common catalyst used in petroleum processing, and accurate analysis of how much HF is recirculating within the process contributes significantly to maximizing the yield rate of crude stock. Early approaches to HF monitoring involved taking manual samples and analyzing them in a laboratory; however, that sample approach offers limited accuracy and exposes lab workers to toxins. More recent FTNIR (Fourier transform near infrared) analyzer techniques are very accurate, but adaptation for real-time online monitoring is complex and costly. A better solution is to replace conventional manual sampling and FTNIR analysis with a measurement system that monitors HF levels in real time by analyzing differential responses from online sensors.
Although the measurement is new, it depends on a collection of instrumentation that has been around for years. Advanced analytical software reads the response spectrum that is directly analogous to the data produced by traditional FTNIR. This measurement and control solution contributes also to maintenance cost reduction by minimizing the potential for corrosion, and supports environment and safety excellence by eliminating any potential sample exposure for plant and laboratory personnel.
Irrefutable bunkering transfers
A combination of Coriolis metering and advanced applications enables irrefutable bunkering transfers. The majority of bunker fuel for world shipping is delivered to ships by barge. Trapped air, held in suspension within viscous bunker oil, artificially increases its volume. This effect has been a major and hitherto unsolvable problem for the shipping industry. The measurement of the supplied quantity currently involves dipping barge tanks before and after delivery and undertaking various calculations and corrections to convert the tank volume measurement into a delivered mass. This process is fraught with difficulties, errors, and personnel hazards. Coriolis measurement offers a workable alternative.
While custody transfer operations do not typically feature rotating pipes, oscillating a section of pipe is required to exploit the Coriolis principle for flow measurement. Oscillation produces the Coriolis force, which can be sensed and analyzed to determine the rate of flow. To use Coriolis force for measurement, a Coriolis meter has two main components: an oscillating flowtube equipped with sensors and drivers, and an electronic transmitter that controls the oscillations, analyzes the results, and transmits the information.
Reliable Coriolis measurement depends on consistent, reliable oscillation, which is determined by four factors: the density of the liquid, the balance of the tubes, the dampening caused by the flow stream itself, and the physical isolation of the tubes from the environment.
Compromising even one of these factors will degrade Coriolis meter performance, and two-phase flow compromises every one of them. Consequently, applications involving even negligible amounts of entrained gas—as little as 2% volume—have been poor candidates for Coriolis measurement. This has been particularly troubling for those running batch operations, where reliable, highly accurate flow measurement can confer considerable bottom-line advantage, but where it is also necessary to begin with an empty or partially filled flowtube.
Advanced digital Coriolis meters have now changed all that. Microprocessors in their transmitters run advanced digital signal processing techniques that provide useful measurements of both mass flow and density, ensuring stable operation in either single- or two-phase flow conditions, such as those found in bunker fuel oil transfer.
Dairy custody transfer
The same principle applies well beyond bunkering. Dairy processors must comply with numerous stringent standards in operations, ranging from procuring raw resources to delivering final product. However, milk processing plants have not had a standard for custody transfer systems. Advanced flow measurement applications can reduce costs and improve material accountability. One large West Virginia dairy with custody transfer accuracy requirements tighter than ±0.2% installed a Coriolis flowmeter-based system, which uses advanced digital technology to compensate for variations in the amount of gas or liquid in a flow, something that had been impossible using traditional Coriolis meters. The system surpassed the customers’ reliability and accuracy requirements, delivering demonstrated accuracy of ±.02%.
Measuring net oil and wet gas
A new generation of advanced applications extends two-phase flow measurement to multiphase flow measurement, which can enable accurate measure of net oil and wet gas in upstream applications. Currently, most oil and gas fields rely on a gas-liquid separator to measure the output of each well. They separate gas from oil and water to measure the flow rate of each component. These gas-liquid separators are very expensive to own and operate. They must be supplemented by tanks to store the separated liquids and equipment to enable water re-injection at the site. An operator may also have to pay for a second pipeline for the gathering facility or for trucks to take the condensate off-site, which again requires a lot of hardware, space, and land. Furthermore, these separators can report information daily at best, but optimal reservoir management requires real-time data.
An advanced application involving a Coriolis flowmeter uses advanced software to enable measurement of flow containing gas, oil, and water directly from the wellhead without first having to separate them. This delivers huge cost, productivity, and environmental benefits. To measure net oil, a Coriolis flowmeter is equipped with an oil and water probe. A remote terminal with an HMI is used to integrate the readings from the probe to an advanced net oil computer (NOC) application.
Net gas is a little more complicated because gas fields first produce gas before they start producing liquids. When a phase transition to liquid production occurs, it may be necessary to install additional liquid handling equipment. Another measurement challenge with wet gas applications is that the production stream is mostly composed of gas with slugs of liquid water and condensate. Multiphase Coriolis measurement enables such measurements to be made real time in situ at the well head. Most reservoir models are based on long-term steady-state situations. Oil wells are typically reported on via well tests once a month, whereas gas wells typically report daily averages. Now with real-time measurements, producers can understand well production better and optimize field operations.
A new age of instrumentation
Most of the examples we have given here involve flowmeters, but they suggest the possibility of building a new knowledge base in which data from conventional field devices is combined with applications expertise, modeling, and advanced process control software to enable measurements that could not have even been imagined as little as 20 years ago.
There is already a significant and growing knowledge base of expertise that helps manufacturers build plants, maintain processes, and keep them operating. Attention is now turning to optimizing plant processes and business systems. As the pace and complexity of business continues to grow, forming clear distinctions between what is simply good know-how and what provides a truly strategic advantage is becoming more difficult. The challenge for automation vendors is to apply that knowledge to help customers achieve excellence in control, asset management, productivity, and environmental challenges that they face.
– Tobias Scheele is vice president of advanced applications for Invensys Operations Management.
iom.invensys.com