Clean-in-place (CIP), sterilize-in-place (SIP) requirements decrease when a Coriolis flowmeter uses a replaceable sensing tube, especially useful for skid-based life sciences and pharmaceutical production, as explained at Automation Fair 2023, a conference and show by Rockwell Automation.
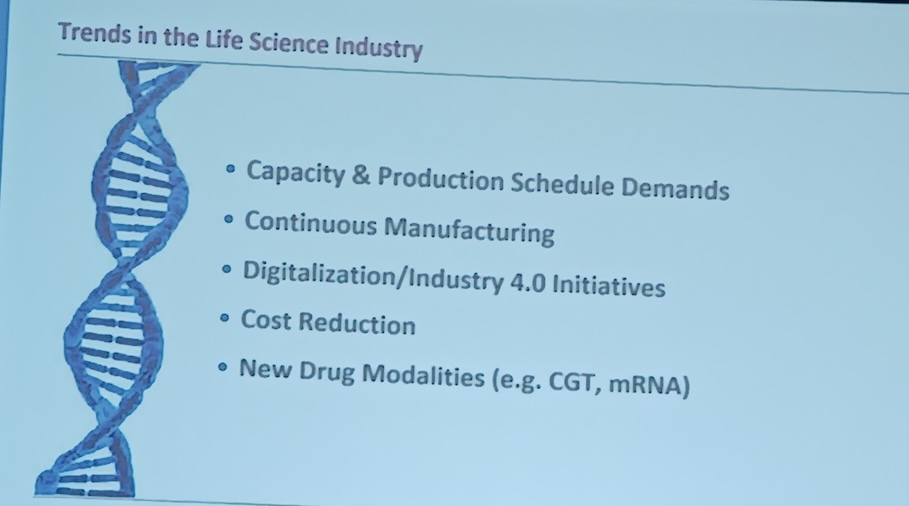
Learning Objectives
- Understand trends in life sciences that are changing process sensing requirements and changes in analytical instrument designs, including flowmeters.
- Review flowmeter application specifications and requirements.
Life science sensing insights
- Life science trends are changing process sensing requirements and along with analytical instrument designs, including flowmeters.
- Flowmeter designs, specifications and requirements need to match application needs.
As pharmaceuticals get more specific with smaller quantities produced, and as pharmaceutical manufacturers seek more flexibility, skid-based pharmaceutical production has increased. To avoid or reduce clean-in-place (CIP) requirements, a single-use Coriolis flowmeter with replaceable sensing tubes is under development from a process sensor and instrumentation manufacturer, as explained at Automation Fair 2023 from Rockwell Automation.
Trends in life sciences are changing process sensing requirements
Key trends in life sciences industries include increased capacity and production schedule demands, continuous manufacturing, digitalization and Industry 4.0 initiatives, cost reduction pressures and new drug modalities. Drug designs are changing with cell and gene therapy (CGT) and messenger RiboNucleic Acid (mRNA)-based treatments, according to Bethany Silva, industry manager – life sciences and Lauton Rushford, product marketing manager – flow, both with Endress+Hauser, in the Automation Fair session, “Flowmeter instrumentation enhances reliability in the life science industry.”
With these changes, original equipment manufacturers (OEMs) and skid designers for life sciences and pharmaceutical manufacturing seek options for increased flexibility and faster changeover times along with avoiding hazardous and wasteful cross contamination. A skid or line requiring CIP or sterilize-in-place (SIP) processing can delay production for up to a week, they said.
Flowmeter application-related specifications
Other OEM or end-user considerations in flowmeter application specifications include mass and volume flow accuracy, repeatability, wetted part materials, current good manufacturing practice (cGMP) calibration compliance, physical space and environmental needs, handling, pharmaceutical compliance, required certifications and approvals, communications abilities and design flexibility. Coriolis flowmeter designs include sensing elements, processor and analytics capabilities, a human-machine interface, and abilities to securely store and transmit data and information. Most modern Coriolis flowmeters, like some other modern process sensors, avoid the need for field calibration.
The Endress+Hauser Coriolis flowmeter, Promass U 500 with disposable sensing tube is expected to be available in first half of 2024, they suggested.
Mark T. Hoske, is content manager, Control Engineering, CFE Media and Technology, [email protected].
KEYWORDS: Process sensing, flowmeters, life sciences manufacturing
CONSIDER THIS
How can new sensor designs, capabilities improve manufacturing workflow?