MGP saved an estimated $3 million with an upgrade using virtualization, compared to a rip-and-replace alternative.
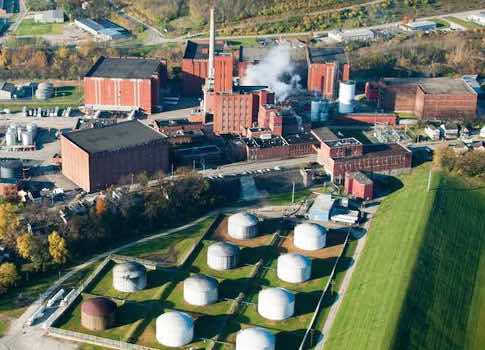
Those who have worked with a virtualized system would not want to go back to conventional control because of cost savings, increased quality, consistency of process, and more efficient use of time.
The automation vendor involved helped create a three-step migration path using virtualization that would ultimately save more than $3 million over the rip-and-replace option with another vendor.
MGP Inc.’s rye whiskey distillery in Lawrenceburg, Ind., produces the bulk straight rye whiskey with a 95% mash bill, popular with bottlers and consumers. Demand is high and continuing to grow. There isn’t time for interruptions in the plant’s continuous, 24/7 operation.
The control system at the distillery has been upgraded several times to keep up with demand. From 1994 through 2001, a distributed control system (DCS) was used to control most major plant functions, including the boiler/utilities, dryers/evaporators, cooking, distillation, and fermentation.
The prior DCS performed well and helped build the distillery’s reputation as the top U.S. producer of brown and white alcohol goods. After more than a decade of success using DCS, the system needed an upgrade to continue growth as the DCS lifecycle was coming to an end, and the human-machine interface (HMI) program in use was no longer available or supported.
The decision was between ripping and replacing or adopting a phased migration plan. Considering that downtime costs five figures per hour, keeping the plant up and running was a top priority.
Considering options
While the DCS served the application well, continued upgrades were needed to help production. The application needed a smooth migration with everything up, tested, and worked out before releasing the upgrade to the tag servers.
Migration creates concerns. The idea of spending the money and time to migrate was stressful. Planning for the migration showed the long-term cost savings. As the migration strategy continues, it will spread investment costs, keep downtime at a minimum, meet the requirements of multiple parties, and ensure that data is available over a corporate network for supervisory control and data acquisition (SCADA). It also will eliminate the potential for extended outages because a new system failed.
Virtualized migration
Possibly the most important part of the migration is often overlooked—virtualization technology. Virtualization approaches control from the IT side. Operations, engineers, and maintenance have been hardwired to deal with physical clients and are comfortable working with physical wires. Virtualization eliminates the need to control through those physical elements. Instead, virtualization emulates the hardware, operating systems, data storage, and networks through virtual operating systems within a host operating system.
The virtualization system chosen uses software that runs on the main host server with process control system. Virtualization allows multiple operating systems to share one host server. The client-based virtualization controls the host processor and efficiently allocates server resources, while allowing each system, or virtual machine, to operate independently in its own shell while communicating with each other. Virtualization software allows users to aggregate separate physical components into a pool of sharable resources that can be dynamically delivered to applications when and where needed.
The virtual machine sits on top of the hypervisor, is independent, and focuses only on its own needs. Instead of taxing the physical server for one purpose, multiple virtual machines run on top of the physical host.
There was no virtualization expert on staff upon beginning the migration. For those with maintenance and operations expertise, there was a large learning curve to understand how a hypervisor and the architecture work. Attending classes through the virtualization software vendor and watching online videos provided more information on virtualization and its potential benefits.
Systems for the boiler/utilities and dryer/evaporator areas have been turned into virtualized systems. Fermenters and yeast rooms are next to be followed by the stills and cookers. Virtualization simplified the migration. It helped achieve the goal of having everything up, tested, and worked out before pushing it out to the tag servers.
Workstations, servers, thin clients
The virtualized computer architecture replaced three workstations and two OS servers with two redundant host servers and six thin clients. Having an engineering station, two tag servers, and five Web-client servers run through a firewall eliminates the need to interact with the thin-client network. There is no hardware support to manage. For example, if the C-drive goes out on a client, there’s no need to work on the physical machines. MGP only had one host operating system to work on and re-create the client. It helps keep everything consolidated so there is only one source instead of numerous people working on different physical machines. Having everything hosted from one source provides greater control of the end product.
Additionally, the virtualized environment uses hosts that communicate with different networks, including a terminal bus, management bus, redundancy bus, and a plant bus. The networks use an industrial Ethernet module that breaks up and simplifies communications. There is added value in security for the control side of the networks because they are independent. There is the ability to set up a second network and run the old system side-by-side with the new system while operators get used to the new dashboard. This provides more safety and more availability.
Redundancy in the control room is important. If something goes wrong with one network another network will take over. A couple of clients are kept in each control room with network redundancies, throughout both the hosts, so if one host goes down everyone will still have a client running on the other host. A hard drive storage configuration backs up the system, so if something goes wrong, just a drive can be replaced, rather than the whole system.
Time, cost savings
Virtualization provides benefits. The instrumentation and controls specialist works at only one station, instead of multiple machines to make changes to any plant area, which brings the DCS under a higher administrative control. As a result, maintenance and hardware costs are way down in comparison to a standard hardware setup. Licensing pays for information, or intellectual properties. Instead of purchasing physical machines a thin client can be purchased for a few hundred dollars (not thousands of dollars for an entire client).
The real cost savings are in installation, implementation, and the hardware no longer needed. After pulling network lines, the thin client is dropped into the operator station, which is much less expensive and easier.
The automation company’s virtualization service was used, helpful for the first experience integrating IT technologies into the industrial environment. The automation company took responsibility for the selection of the software and hardware components, including virtualized server setups, configuration of the virtual machines, installation and configuration of the operating system, and installation of the process control system software.
Support for the system included hosts and thin clients, virtualization software, and the prebuilt virtual machines with operating systems installed and licensed, including the process control system, helping to reduce lifecycle cost and ensure future upgrades.
Costs are also significantly lowered without maintenance of conventional hardware, as compared to virtualization hardware requirements.
Migration pays off
The migration strategy using virtualization is well underway and on track for completion in 2020. The migration focused first on areas of highest vulnerability to the least, starting with HMI and ending with input/output (I/O) connections. Boiler/utilities and dryers are migrated. 2016 will address the fermenter and yeast rooms, and next year cooker and stills will get an upgrade.
Migration began in 2014 and includes upgrading 200 HMI screens. Now underway is replacement of eight prior DCS controller nodes with redundant process control system controllers. The migration will end with Ethernet or device communications to 7,300 I/O points, swapping out more than 260 I/O cards. A process historian and an information server will support long-term archiving and reporting needs this year.
Virtualizing the plant has reduced costs because of fewer computers to manage and repair. A central location administers control systems. The instrumentation and controls specialist can take care of anything in the plant from the office, and about 20% less time is spent working on hardware issues. It also has helped to improve the longevity of the control system. Most applications have about a 5- to 7-year lifecycle. With a software package running, that life span has increased to 10 to 15 years before it becomes antiquated and needs to be modified.
Jason Singleton is instrumentation and controls specialist at MGP Inc., Lawrenceburg, Ind. Edited by Mark T. Hoske, content manager, CFE Media, Control Engineering, [email protected].
MORE ADVICE
Key concepts
- Virtualization allows orderly DCS migrations without rip-and-replace shutdowns
- Less hardware is required with virtualization
- Centralized process control design saves time.
Consider this
If virtualization can make DCS migration less painful, haven’t you waited long enough?
ONLINE extra
Learn more about the products used in this case study in an article linked below.